Top: Holden Village is surrounded by the Glacier Peak Wilderness Area in the North Cascades of Washington State. Image courtesy Eric Bosell
Holden Village is an isolated mountain community located within a keyhole of land (created by a former copper mine) that is surrounded by the Glacier Peak Wilderness Area deep in the North Cascades of Washington State. On-site disposal of any garbage is not allowed. Instead, it must be transported by a combination of truck and barge via Lake Chelan (one of the largest and deepest lakes in the region) to a regional landfill — a practice that costs over $1,000 per trip. Holden Village is comprised primarily of a retreat center, with a peak population in the summer months of about 450, and about 7,000 visitors annually. “A large percentage of our trash is food waste,” says Nathan McClure, Holden Village’s “Garbologist,” who is responsible for managing all the village’s waste. “The center had been using two Green Mountain Technologies (GMT) Earth Tubs with total capacity of 6 cubic yards (cy) to compost food scraps. But the units weren’t large enough to allow our volumes of food waste to break down fully before needing to empty them and start a new batch.”
The center worked with GMT to design an in-vessel system comprised of three aerated bunkers, each with 6 cy of capacity, for a total of 18 cy of food waste and wood fiber collected within the village. The system was built inside an enclosed utility/shop building, with exterior access doors to allow loading and unloading of feedstock using a truck or tractor. The bunkers are positively aerated; process air is pulled through a biofilter housed in one of the repurposed Earth Tub located outside the building. “The new system gives us the capacity to create finished nutritious compost, which only takes about eight to ten weeks,” adds McClure. ”We expect to process approximately 35,000 pounds/year of compostable material with the new composting system.”
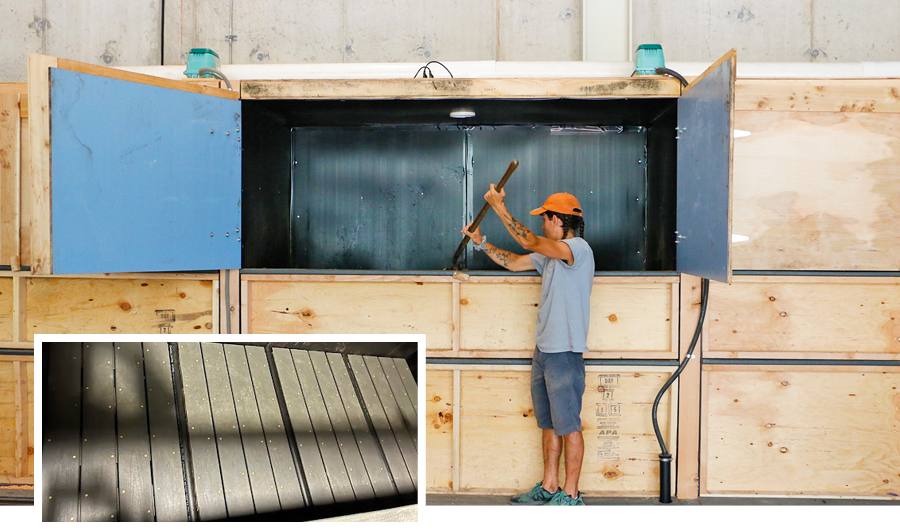
The outer walls and framing of the bunkers are made from plywood boards. Cross hatched composite decking boards allow leachate to drain to the floor (inset). Photos courtesy Green Mountain Technologies
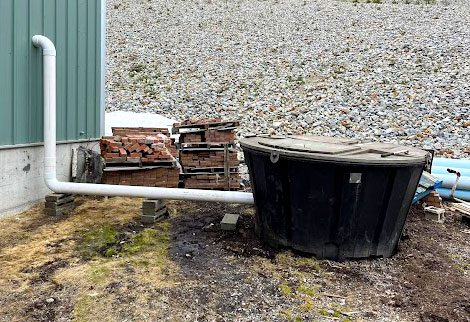
Process air is pulled through a biofilter housed in a repurposed Earth Tub located outside the building.
He explains that the outer walls and framing of the bunkers are made from plywood boards (2×4-ft/2×6-ft). The inside walls are lined with corrugated plastic to prevent the bunkers from “decomposing.” The corners are sealed with Gorilla tape. The floors of the bunkers have cross hatched composite decking boards that allow leachate to drain to the floor without the compost sitting in it. “We created a shower pan with the corrugated plastic that catches the leachate so it doesn’t leak all over the floor, or saturate any of the wooden boards,” notes McClure “We keep sawdust in the shower pan ‘maintenance port’ to soak up the leachate so it doesn’t overflow over time. This maintenance port is also where the ABS (black plastic) piping — placed in between slats of the composite decking — is connected to a blower fan. The fan is on a 30 minutes on/15 minutes off timer cycle running around the clock. This allows enough air to oxygenate the pile, but not so much so that it dries it out completely. When loading the bunkers with food scraps, we put porous woody material in between the layers so the oxygen has space to pass through.”
Capital costs for the new system were about $18,300, according to Eric Bosell at Holden Village. The compost is used within the village and the surrounding area, which includes mine remediation, as well as an area impacted by a relatively recent forest fire.