Haulers, as well as manufacturers of trailers, floors and lifts used to collect and transport food waste, are experiencing growing demand for their services and equipment.
Nora Goldstein
BioCycle July 2013, Vol. 54, No. 7, p. 33
As part of its global sustainability initiatives, Walmart set a goal of diverting all food waste generated by its grocery stores from landfills. Rollout in the U.S. began aggressively in 2010. The company contracted with Quest Recycling to implement the program; in turn, Quest recruited contractors around the country to collect and transport the food waste. Today, the largest percentage of the food waste collected is used for animal feed, followed by composting.
While other supermarket chains had been source separating their nonedible food waste for diversion to composting for many years, the scale and rapid implementation of Walmart’s program — the goal was to achieve the nationwide rollout over the course of 2010 — quickly ramped up demand for collection and transport strategies. Contractors selected by Quest examined options. For example, one company decided that the most efficient way to service the stores was to use a battery operated pallet jack to bring the food waste container to the truck, versus waiting in line to pull in and unload the container using the lift on the truck. This method enabled the hauler to service stores in an average time of 30 minutes.

Travis Trailer’s Organics Trailer Tote Dumper is an all-aluminum, self-loading and unloading unit with a bucket that has 4,000 lbs lifting capacity. A battery-powered pallet jack — used to bring full containers of food waste to the truck — is transported in the bucket between stops.
“We have sold a lot of the Organic Trailers to contractors for Walmart food waste collection,” Hughes adds. “We didn’t have to make dramatic changes to make it work for that purpose. The primary change was with the bucket itself so it would accommodate different size containers. In the beginning, we couldn’t get a good feel for what the commodities would weigh, as this trailer had been used mostly by the rendering and grease industries. We narrowed it down to a weight per cubic yard, and a 60 cy trailer has pretty much worked in every instance. Most states have a legal payload limit of 80,000 lbs, which includes the weight of the truck and trailer — about 32,000 lbs. That leaves 48,000 lbs of carry capacity, but you don’t want to fill it to the top due to the ‘slosh effect’ of the payload. Most of the time organic waste has enough water in it to seek its own level in the trailer.”
As the trailers were put into use for food waste collection, contractors experienced some spillage as the containers were being unloaded. That led Travis to design and install aluminum “fins” on the sides of the lift, which have been very effective in preventing any food waste from spilling out.
Containers And Lifts
While conducting interviews for this article, there was consensus among the equipment suppliers that food waste collection and transport is a rapidly growing sector of the hauling industry. However, among the organics haulers, opinions were varied as to the preferred way to provide the service. For example, one preferred trailers because they could maneuver better, i.e., they can jackknife, to reach the containers. Another preferred a straight truck with a front-loading lift due to safety, i.e., drivers do not have to get out of the truck at stops with higher traffic.
And then there are the variables that can impact the truck purchase. One variable is the type of generator being serviced, e.g., restaurants in an urban setting with containers set out in alleys versus loading docks with plenty of access at corporate cafeterias and supermarkets. Another variable is the types of containers used by the generators — anywhere from multiple totes up to 6 cy to 8 cy. “For our varied customer base, we made a decision to go with containers that range in size from 1-cy to 8 cy, depending on what is being set out,” notes Carla Castagnero, president of AgRecycle, Inc. in Pittsburgh, Pennsylvania. AgRecycle, a composting company, began offering food waste collection in 2006 with only the preconsumer stream, then expanded the service two years later to include postconsumer food waste as well. “Three 65-gallon toters is roughly equivalent to a 1-cy container, so a store setting out 2 cy would need 6 totes,” she explains. “We have found that 6 totes takes up more space than a 2-cy container. In addition, many of our customers don’t generate enough cardboard to warrant a separate pickup, so we have them put the corrugated in with the food waste. With totes, the cardboard has to be folded up to fit inside. It is much easier just to place it in the container.”
AgRecycle needed to figure out the collection method before determining the type of truck it would need for collection. “Once we decided we were only going to use containers, our only choice was a front or a rear-load truck,” says Castagnero. “And we only wanted a straight truck, not a trailer.” The company uses a Heil truck body with leak-proof seals, and a lift arm with forks to pick up the containers. At the time they were shopping for a lift arm, they were unable to procure one that could accommodate totes as well if that became a necessity for a customer.
As it turns out, such attachments were available, but were not being marketed for food waste collection at the time AgRecycle began its service. Perkins Manufacturing Company’s D6064 Front Loader Attachment options — designed to work with totes and containers — are a case in point. For example, its D6064D attachment is a hydraulically operated grabber that picks up 32-gal, 64-gal or 96-gal carts; the arms rotate all the way open to pick up containers using the forks on the attachment. “We have been making our D6064 attachments for over 20 years,” says Cheryl Hoppe Waite, president of Perkins Manufacturing Company, located in Romeoville, Illinois. “We came up with this design so the front load garbage trucks could do commercial and residential routes without changing trucks to complete their route for the day. In the last 3 to 4 years, we have sold more of the lifters for food waste hauling.”
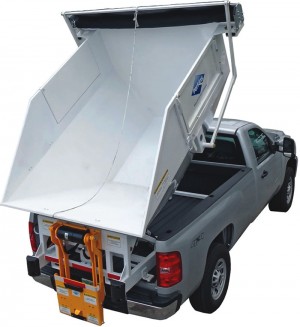
Perkins Manufacturing is introducing a pick-up truck insert that will facilitate collection of food waste in smaller communities and at resorts, parks and institutions.
That ability to have one lifter attachment that can unload multiple sizes of carts and containers is a feature of the D6064E front loader attachment. The D6064A is designed for carts only. “It has one, two or three plates for up to three 32-gal or 64-gal carts or up to two 96-gal carts,” she explains. “The unit has a total weight capacity of 900 lbs, e.g., two 96-gal carts each weighing 450 lbs.”
Perkins also has been manufacturing its Candy Cane lifter since 2007. The canes can be mounted to sideloaders, rolloff containers or dockside stands that can tip heavy carts into collection vehicles or rolloff containers. “We’ve also seen an increase in the Candy Cane lifter being used for food waste pick up over the last three to four years,” adds Waite. “As far as what trends Perkins has been seeing, there are more requests from haulers who are looking at ways to convert one or more of their current trucks to a food waste truck. And more of our customers are interested in and purchasing our Cane application to use on their rolloff sideloader trucks.”
This month, Perkins is introducing a pick-up truck insert that will facilitate collection of food waste in smaller communities, as well as larger resorts and institutions such as universities. The Perkins Satellite Lifter Systems mount to the rear bed of any standard 8-foot pick-up truck. It is available in 3 cy and 6 cy sizes, as well as 60/40 or 70/30 split-body configurations, although the 60/40 is not available with a lifter option. “We are manufacturing the insert here, so it can be custom-made to fit the needs of the haulers,” says Waite. “It is manufactured from steel and power painted and protected, as well as fully sealed. A tarp is available. The unit itself weighs about 1,400 lbs and works with our lifters for hook style and European Comb carts or barrels. It is the perfect size for collecting food waste and organics in small volumes from local generators.”
Customized To Fit
Because of the diversity in the food waste collection and transport landscape, Brown Industrial, based in Botkins, Ohio, takes a custom design and manufacturing approach to service organics haulers. Brown Industrial is a third generation company founded in 1936. “We’ve been working in the rendering industry since the 1940s,” says Craig Brown, grandson of the founder, who manages and owns the company with his brother Chris Brown. “We are probably the only full-line rendering manufacturer in the market today. We were sought out by food waste collection companies because of our long experience with rendering.”
Brown Industrial sells both stainless steel and aluminum trailers but steers customers toward its 409 Stainless steel bodies for food waste collection. “There is a perception that aluminum is a lot lighter than stainless steel but it isn’t really,” explains Brown. “For hauling food waste, we think it provides better durability.” Overall, he adds, the company puts its emphasis on building arms and lifting devices, and then customizing a trailer that fits those components. “We don’t do one size-fits-all. For example, even though the container industry says the placement of holes for the forks are standardized, we’ve found they can vary by 20 inches in some containers. We can make modifications to service the containers in use by food waste generators.”
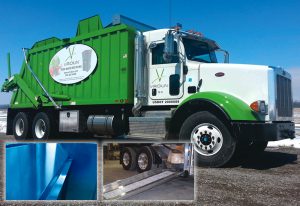
To service food waste generators in Ohio, Viridiun purchased Brown Industrial’s straight truck trailers. Features include front and rear splash pans (inset, left) to direct the “splash” back into the trailer when the driver starts and stops, and a storage container under the truck to transport a pallet jack and tools (inset, right).
Similar to Perkins Manufacturing, Brown Industrial is seeing some haulers get their feet wet in food waste collection by adding lifts to their rolloff trucks. “At lot of haulers have rolloffs in their fleet, so we build and install food waste units to get them started, without them having to invest in new trucks,” he notes. “We anticipate exponential growth in this sector in the next 5 to 10 years. Once Walmart rolled out a program nationwide, we knew it was going to be happening more.”
Live Floor Option
Live-floor trailers are not new in the waste hauling business, but having a floor designed for food waste transport is a fairly recent development. Hallco Industries, Inc. introduced its Leak-Proof Live Floors™ for food waste collection several years ago. “We use a front-mount drive with the slats bolted to the unit,” explains Charley Russell of Hallco. “It comes through the front bulk head and the cylinders and rods move the slats in a certain direction to make it unload. A pan is installed underneath the floor to capture the liquid that comes through the slats, which is why the drive can’t be mounted on the bottom like it is for other hauling applications. If we don’t let the floor leak a little, the slats are too tight to move properly.”
The floor is customized to fit the trailer size. Most trailers these days are 102-inches wide, notes Russell. The slats are made from extruded aluminum, which can be affected by the acidity in food waste if the floor isn’t maintained. “In addition to washing down the inside of the trailer at the end of the day, we recommend something as simple as soda ash to neutralize the acid,” says David Lowry of Hallco, who is based on the West Coast and has sold a number of the live-floor units for food waste hauling. “You can sprinkle it all over the floor and let it sit for a half-hour or so. It really does prolong the lives of the floors.”
When asked if the high liquid content of the food waste makes it difficult to “walk” the load out of the trailer, Lowry notes that hasn’t been an issue. “The commingling of different types and structures of the food hold it together and push the material along,” he notes.
Variety In The Fleet
Viridiun, a food waste recycling company based in Atlanta, Georgia, started in January 2010. Its initial focus was on hauling, although it also is involved in the receiving and processing end of the business. “We are primarily a hauler, which is where the majority of our business and revenue comes from,” explains Jeff Beatty, Vice-President of Sales. “But we also recognize the value in the backend process and whatever that technology ends up being for the future, Viridiun wanted to have a part in that as well. Currently, we own and operate feed mills, leasing property on the farms where the food residual is processed and fed to the animals on those farms.”
The company offers hauling services in 13 states, predominantly in the Southeast. Recently, it opened an office in Ohio. Grocery stores represent about 80 percent of the food waste generators serviced, with the remainder split between food manufacturers and restaurants. “We are limited somewhat to taking only preconsumer food waste because we primarily make animal feed for cattle, and can’t include meats and some other food scraps,” says Beatty. “In Ohio, however, we are all postconsumer, servicing grocers, restaurants and manufacturers.”
Viridiun’s clients are mostly serviced with 3-cy metal containers made by BWE (Bakers Waste Equipment). It also uses BWE’s 6-cy metal containers in some cases, as well as smaller 64-gal totes. The majority of collection and transport vehicles in its fleet are 35-foot trailers supplied by Travis Trailers. “We also have a handful of Brown Industrial trailers, and recently purchased two of their straight trucks for servicing food waste generators in Ohio,” he adds. “It is essentially the same trailer, but shorter. We are picking up at smaller sites and needed to make it easier to access the containers.”
In general, trailers with more capacity work better with Viridiun’s business model, as drivers run 8 to 10 hour routes and typically do not unload until the end of the day. “All of our trucks have scales, and drivers use hand-held units to enter the weight of each load, as well as how long they were at each location and who they spoke with,” notes Beatty. “We use Road Net software to capture the information we need. All of our routing is done in Georgia. When a driver gets to work he logs in on a handheld device and downloads his route for the day. We can make changes to that route during the day, e.g., if a store has an emergency and needs an unscheduled service. Overall, we have 30 trucks on the road in any typical week.”
Most of the company’s challenges in the beginning were with capacity of the lifts. “Rendering trailers were made to pick up trash can-type containers, not full dumpsters,” he says. “Early on, I think everyone in the industry was surprised about how heavy containers loaded with food waste are.” In terms of drivers, Viridiun seeks people who are qualified to drive tanker trucks, as they have experience hauling wet loads. Finally, preventive maintenance on the trailers is critical, including thorough clean out to prevent corrosion. “We work hard to make sure the trucks we have are always on the road,” Beatty concludes.