Top: Food waste and amendment are tipped into the mixer (above left) then conveyed into the composting drum. Facility photos courtesy of New Hanover County Environmental Management.
Nora Goldstein
In 2012, New Hanover County, North Carolina conducted a waste characterization study and found that about 75% of what was going into its landfill could be beneficially used in some way. One of the biggest components in the waste stream was food waste. The county didn’t have a composting site where it could divert the food waste stream. “All yard waste was chipped up and hauled away or used as cover on the landfill,” says Andrew Mulvey, Environmental Specialist with New Hanover County. “We decided to build a facility, but were running out of land on the footprint. So we opted for an in-vessel drum composting system instead of windrows.”
The county installed a DT-Environmental EnviroDrum in-vessel composting unit with 60 cubic yards of operating capacity. The facility opened in November 2017. Capital cost for the in-vessel composter was around $340,000. Accepted materials include yard trimmings, all food waste, pet food and any bags, plates, flatware, straws or cups marked “BPI Certified Compostable.” The facility services residents, businesses and institutions in the county. Residents can bring unpackaged food waste to the county’s facility, or drop it off at the “HazWagon,” a mobile household hazardous waste unit stationed at three locations each week. Drop off is free of charge.
The first higher volume food waste generator to tip at the facility was the University of North Carolina (UNC) Wilmington. The campus had wanted to divert its food waste to composting, but a nearby facility wasn’t available. “I was hired as the Sustainability Coordinator in 2014, and the first thing my boss told me was that she wanted to start composting campus food waste,” recalls Kathryn Pohlman, now UNC Wilmington’s Chief Sustainability Officer. “I started talking with this group that eventually became the Coastal Composting Council (see box), and we decided to approach the county about opening a facility at the landfill. Joe Suleyman, Director of New Hanover County Environmental Management, had been trying to start a composting program, so the timing was excellent. The county was given the budget to purchase the in-vessel composter and UNC Wilmington helped to write the permit application.”
The university had installed a food waste pulper at its Wagoner Dining Hall to remove the moisture and reduce its trash hauling bill. Both plate scrapings (done by kitchen staff) and kitchen prep food waste are pulped. As part of the permitting process in 2016, Pohlman, Marie Davis — a graduate student at the time and now Sustainability Manager with Aramark at UNC Wilmington — and others helped sort loads of the pulped food waste at the landfill to assess the amount of contamination. They were able to identify the sources and work with the dining hall to eliminate it. “We did the sorting several additional times with just the Campus Dining team and eventually included a visit to the operation with our entire management team,” says Davis. “I still have members of my team tell me how impactful that experience was for them!”
Prior to campus closure and the current gradual return of students due to the COVID-19 pandemic, the student population was around 17,000. About 3 to 4 tons/month of food waste are collected and emptied into a compactor, which is hauled twice a month by Green For Life to the composting facility. From when it started sending its food waste to the New Hanover County composting facility on November 16, 2017, through August 2020, UNC Wilmington has diverted 160 tons of pre and postconsumer food waste, notes Davis.
The Wagoner Dining Hall has switched for the time being to using BPI-certified compostable serviceware instead of reusables since students have returned for the fall semester. “It’s an additional safety precaution due to the COVID-19 pandemic,” she adds. “Since virtually everything is compostable right now in the front of house, we have halted use of the pulper for the time being. We are using our dish return area in a whole different set up where food waste and compostables are just collected and put directly into the compactor.”
In July 2018, Riley Alber launched Wilmington Compost Company, a subscription food waste collection service catering to businesses, institutions and households. Alber had been working on an organic farm, which sold produce to restaurants and other outlets in Wilmington. Some of the businesses expressed interest in being able to divert their food waste. “That gave me the idea to start a community collection service,” says Alber. “Having the composting facility in the county — which had capacity that wasn’t being fully utilized — enabled all the pieces to fit together. We divert upwards of 5 tons/week now. Prior to the pandemic, it was in the 25 to 30 tons/month range. Tonnages are increasing again as we continue to expand the collection service.”
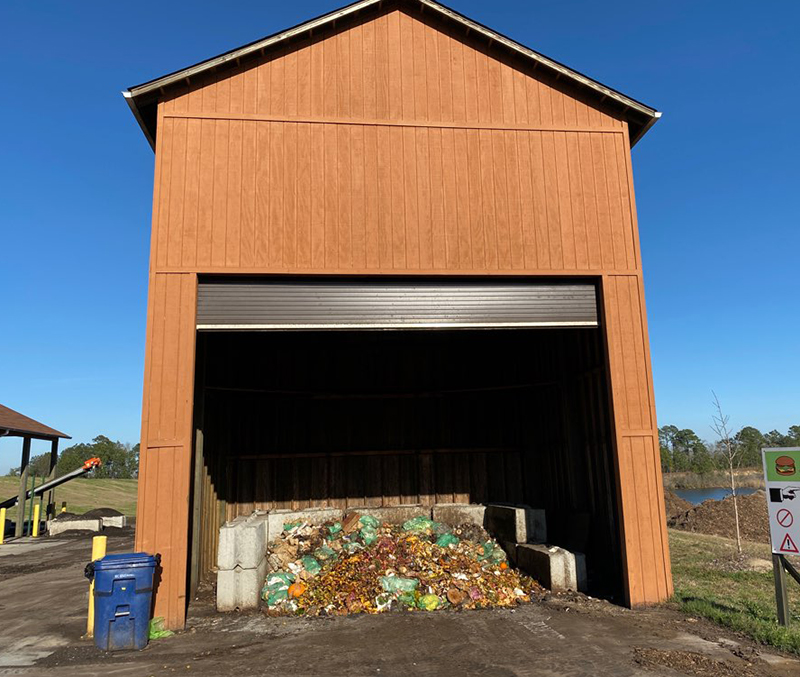
Food waste tipping building at the New Hanover County composting facility. Photo courtesy of Wilmington Compost Company
Facility Operations
Food waste is tipped into a receiving area at the composting site where contaminants can be removed by hand. The quantity varies depending on the feedstock, notes Mulvey. “Sometimes it’s too much and sometimes it’s too little. UNC Wilmington was the first to bring food waste here, which dropped off due to the pandemic, but is ramping up again. Wilmington Compost Company, fortunately, has been collecting an increasing amount. If we have enough food waste on hand, we will load 8,000 to 10,000 lbs/day — a portion in the morning and the remaining amount later in the day.”
The drum is 40-feet long and 8-feet in diameter, and has the capacity to process 6 tons/day of organics with as much as 50% shrinkage by weight during composting. Food waste is loaded into a 4-auger horizontal mixer, along with the ground yard trimmings — one-third food waste to two-thirds amendment. On occasion, horse manure is dropped off at the facility and added to the mix. Moisture content of the mix is 50% to 55%. From the mixer, the material is conveyed to the EnviroDrum. The rotating motion levels the material as new feedstock is added, and an equivalent amount spills out from the other end. “The drum is installed ‘dead level,’ which contributes to the effectiveness of the process,” explains Steve Peerce with DT-Environmental/Daritech. “There is a blower on the entry end of the drum, which pulls fresh air from the exit end, flowing countercurrent to the flow of material. The airflow provides fresh oxygen to the bacteria, and removes moisture being created. Negative air pressure is maintained in the drum at all times, preventing the escape of offensive odors. All exhaust air is captured in the pipe coming off the blower, which runs on a 1 hp motor. A booster is needed when a biofilter is required. The New Hanover County facility does not have a biofilter.”
Retention time in the drum is a minimum of 3 days, but varies depending on the quantity of feedstocks being put through, says Mulvey. The temperature in the drum is maintained at 55°C or higher for three days or more. To document that PFRP (process to further reduce pathogens as required by the permit) is achieved, the drum has sampling ports for temperature checks. As a default, adds Peerce, air temperature is monitored exiting the drum, which typically runs 5° to 10° cooler than the material inside.
Compost exiting the drum falls into a trommel, supplied by DT-Environmental. Screened material falls on to an exit conveyor. The overs, such as large pieces of yard trimmings, are collected and put back into the drum for reprocessing. “All of the compostable utensils and other compostable products break down in the drum,” notes Mulvey. “They are completely disintegrated in the three day retention time in the compost drum.”
The county built 4 concrete-walled bunkers for compost curing (photo below). Minimum time for curing is 11 days but is typically longer. The county has a policy to not sell any of the finished compost. A portion is used by the New Hanover County Parks and Gardens department. Wilmington Compost Company distributes the compost to school and community gardens and other “soil enthusiasts,” says Alber. Customers participating in the company’s collection program receive compost as part of the service.
Mulvey performs maintenance on the drum about once a week. “For the most part, it’s greasing the mixer, the rollers and chains on the drum and the ends of the drum that have grease fittings,” he says. “We also sweep out under the conveyor belts. The whole process takes about an hour. We change the oil bath on the mixer every 6 months.”
Organics Collection, Contamination Management
Wilmington Compost Company is the main supplier of food waste to the New Hanover County composting facility. Its residential collection service provides households with a 5-gallon bucket lined with a compostable bag that is picked up once a week. Customers pay a monthly fee to participate.
Commercial accounts (about 75% of the company’s business) receive a 64-gallon wheeled container(s) with a bungee strap lock system for the lid. Liners are not required for the carts, but are available to customers who want to use them. Filled carts are swapped out for clean ones. Wilmington Compost uses a 16-foot box truck to do the hauling. Commercial accounts are billed monthly; collection frequency varies from weekly to more frequently depending on the customers’ volumes. “We don’t have a set rate for the commercial collection as it is adjusted to the volume and frequency of pick ups,” notes Alber. “Some customers have been able to reduce the size of their trash containers by diverting their organics. For example, one business got rid of its 4 cubic yard dumpster and now has two 95-gallon carts for trash. Residents have told us in a 3-month timeframe of diverting their food scraps, they’ve reduce the size of their trash cart from 95 gallons to 35 gallons, which saves them money because the City of Wilmington has a Pay-As-You-Throw rate structure.”
Training is offered to new commercial customers; Alber meets with staff to discuss what composting is and why it is important to participate, review what can be composted, and do a walk through to set up the internal source separation stations. “We talk about transitioning their Slim Jim from landfill to compost — educating where we can and raising awareness,” explains Alber. “Businesses and other establishments are given signage and a logo to put on the front door or window stating they are participating in the program.”
Wilmington Compost can supply entities that want to use certified compostable serviceware with cups, plates, utensils and other products manufactured by Eco-Products. It also procures bin and cart liners from BioBag. This enables the company, a distributor for Eco-Products, to ensure that products are being used that do disintegrate in the New Hanover County composting system.
The company charges a fee for visible contamination in the carts. “I reach out to customers and give them a warning, explaining what shouldn’t be put in with the food waste,” says Alber. “If it continues after the warning, we charge a fee but still take the carts and separate the contaminants out in the tipping area at the composting facility.”
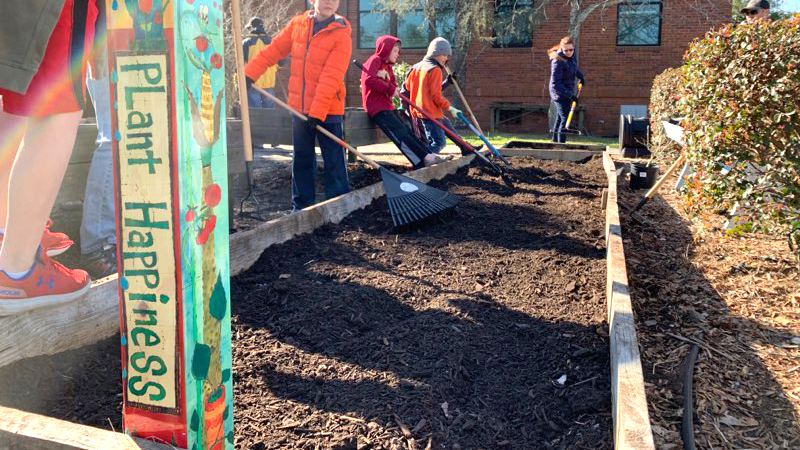
Compost is distributed to school (above) and community gardens and other “soil enthusiasts.” Photo courtesy of Wilmington Compost Company
Without a doubt, providing food waste composting capacity in New Hanover County fulfilled a demand for diversion. Households, businesses, the university and a school in the county (see box) are all contributing to the flow. The Coastal Composting Council (see box) assists with education and outreach, not just on food waste recycling, but also food recovery. And outlets for the finished compost are abundant. “Soils here are very sandy, with less than one percent organic matter, so the ability to amend the soils really drives home the importance of composting,” notes Alber.