Groundbreaking held in June for 180,000 tons/year anaerobic digester that will generate up to 3,000 dekatherms/day of renewable natural gas.
Craig Coker
BioCycle August
The Wasatch Resource Recovery (WRR) project in North Salt Lake City, Utah broke ground last month for an anaerobic digestion facility that will convert food waste into biogas to generate renewable energy and fertilizer. The first phase of the project will process 180,000 tons/year of source separated organics; the second phase will increase the capacity to 250,000 tons/year. Phase I will generate up to 3,000 dekatherms a day of renewable natural gas (RNG).
Once both phases are operational, WRR will supply enough RNG to meet the needs of approximately 15,000 homes. Capital costs for the new facility are estimated at $43 million ($239/ton of installed capacity). Facility start-up is expected in late summer 2018.
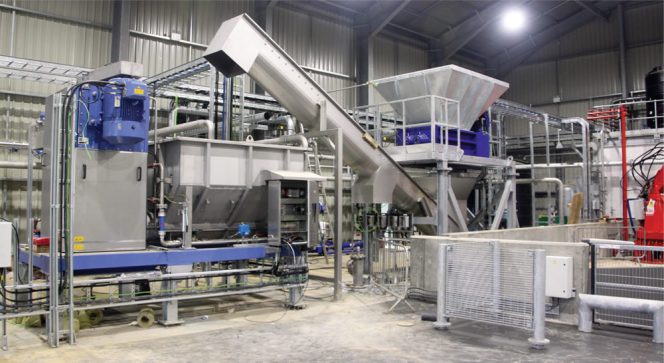
Solid food waste feedstocks will be depackaged, decontaminated and slurried to 10 to 14 percent solids in the Re:Sep system (example installation above). The unit includes a vertical paddle mill with 2 sizes of screen mesh.
WRR selected General Electric’s Monsal advanced anaerobic digestion technologies to provide the main components of the digestion system, including GE’s Re:Sep 2.0 separation technology for removing contaminants from the food waste, sequential gas mixing technology for keeping contents mixed in the continuous stirred tank reactors (CSTR), a pump mixing system for liquid waste storage tanks and heat exchangers for the heating process. The digesters will operate at mesophilic temperatures.
“The WRR project will produce energy from waste organics including prepared and packaged foods, fruit and vegetables, meat and dairy, fats, oils, grease, expired beverages, screened curbside wastes and liquid organics from major food processors in the area,” explains Eric Alder, vice president of operations at Alder Construction, a member of the consortium building the project. “The facility will be the first in Utah.”
Feedstock Preprocessing
Incoming wastes will be received in an enclosed hall, with the building air routed to a biofilter for treatment. Liquid food wastes can either be directly fed to the digesters or be used as dilution liquid in the Re:Sep. In all cases fats, oils and grease (FOG) go directly to the digester.
Solid food waste feedstocks will be depackaged, decontaminated and slurried to 10 to 14 percent total solids in the Re:Sep system, which includes a vertical paddle mill with two sizes of screen mesh. The slurried feedstocks are routed through a hydrocyclone to remove grit and heavy inerts, then fed into a buffer tank with a 3 to 5 day residence time. Feedstock from the buffer tank will be metered into the CSTRs for a 20 to 22 day hydraulic retention time. Because all the biogas will be upgraded to RNG for pipeline injection, there will be no source of waste heat. Instead, the reactors will be heated by dual fuel (biogas and natural gas) boilers.
Plastics, metals and glass will be recovered at a containerized liquids receiving station “It is a separate line that can accommodate beverages in plastics, aluminum or glass,” says Alder. “It will be loaded via a forklift, with the wastes/recyclables being loaded into bins for recovery.” Glass will go to a local recycler and the plastics and metal to local materials recovery facilities.
The biogas cleaning system is being supplied by DMT Clear Gas Solutions, using the company’s Sulphurex®BR regenerative technology to reduce hydrogen sulfide (H2S). This is an upflow water scrubber based on microbial conversion of H2S to sulfuric acid and elemental sulfur. Carbon dioxide removal is done by DMT’s Carborex®MS technology, a dry membrane filtration system. Moisture is removed both by condensation and as an ancillary benefit of the CO2 membrane filtration system. “We elected to design the system to make RNG rather than electricity because there is an existing natural gas pipeline adjacent to our site,” said Bowerman.
Digestate from the CSTRs will be dewatered with a screw press. Solids will be used for land reclamation to improve organic material content in the predominantly alkaline soils common in the Salt Lake basin. The effluent from dewatering will be routed to the wastewater treatment plant next door.
The WRR project is a joint venture between ALPRO Energy and Water, a joint venture between Alder Construction and Aqua Engineers, and the South Davis Sewer District. Sewer District staff will operate the WRR AD facility.
Craig Coker is a Senior Editor at BioCycle and CEO of Coker Organics Recycling (www.cokercompost.com) near Roanoke, VA. He can be reached at ccoker@jgpress.com.