Compost made from short paper fiber and other industrial organics has been key to growing corn and hay crops in a former gravel pit.
Robert Spencer
BioCycle December 2012, Vol. 53, No. 12, p. 39
Mass Natural Fertilizer Co. (MNFC) in Westminster, Massachusetts, was one of the first fully permitted solid waste composting facilities in the Northeast, opening in 1987 as an adjunct operation for an 800,000-hen egg farm. Realizing it needed a full-time manager of the composting operation, Bill Page, Sr. was hired by Westminster Farms, the egg company, to be the composting facility manager. Within a few years, Page had purchased the egg business, however due to stiff competition from much larger, out-of-state egg producers, he decided to close it in 2002 and focus on expansion of the composting operation as MNFC.
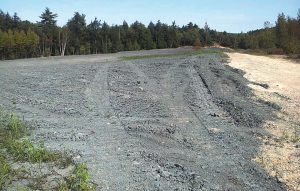
Approximately 5 acres of the gravel pit received 6 to 8 inches of compost that had been aged for several years. A bulldozer was used to spread the material.
Initial investments in developing a residential subdivision on a portion of the gravel pit were abandoned as the housing market collapsed in 2007 and 2008. Although water lines were installed to part of the proposed subdivision, the owner of the pit decided to allow Foster to reclaim a portion of the pit and plant corn and hay crops.
The decline of the housing industry impacted Page as well. He began to investigate other local markets for MNFC’s compost product. “Five years ago we were selling our Top Shelf loam for several hundred new lawns per year, but in the past few years that market has almost totally collapsed,” says Page. “I have known Bill Foster for many years and I knew his cousin owned this large gravel pit just a few miles away from my composting operation, so we agreed to conduct a demonstration project using our unscreened compost.”
One of the primary feedstocks processed at MNFC is paper mill sludge, or short paper fiber (SPF). To compost SPF, a variety of industrial waste materials were blended with it, such as cranberry hulls, juice manufacturing sludge, coal/wood ash, stump grindings and whole tree chips. MNFC is required by the Massachusetts Department of Environmental Protection (MassDEP) to have new feedstocks approved on a case-by-case basis. Laboratory results are reviewed by MassDEP and MNFC before a new source of organic waste is delivered for composting.
Such pretesting has enabled MNFC to develop a high quality product from a wide range of input materials, and the resulting compost and organic loam has been marketed to garden centers in the metro Boston region for 26 years. Other markets include landscaping, gardens, athletic fields, landfill capping and wetland construction.
Reclamation Pilot
In the first year of the gravel pit reclamation pilot, Foster covered the trucking costs and applied the compost. Approximately 5 acres of gravel pit received 6 to 8 inches of compost that had been aged for several years. A bulldozer was used to spread the material, and Foster used no-till planting to put in corn for animal feed. Herbicide and fertilizer were also applied, and within a few weeks the corn was growing. “I was pleasantly surprised to find that, with a minimal investment, I was able to generate a decent corn crop, about 25 tons/acre, and it was a very dry summer,” says Foster. “I’m sure since compost holds moisture that is the main reason we had such good growth of the corn crop, so I decided to continue the project.”
Over the next few years, MNFC and Foster have reclaimed approximately 20 acres of gravel pit. “The fact that we do not have to screen the compost for the land reclamation project, and can deliver the compost as a back haul since our trucks go by the entrance to the pit on a daily basis, it helped me move compost during a downturn in the compost market,” explains Page. “As long as I was getting the cost of loading the trucks covered, I was willing to provide the compost at minimal cost.”
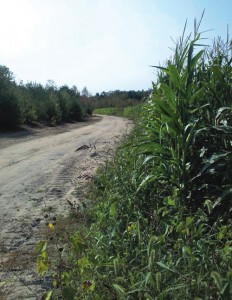
The corn crop yield was about 25 tons/acre the first season. This was encouraging, given that it was a dry summer.
“Land reclamation for agricultural use is a great use of SPF compost in this part of New England,” Poirier explains. “Most of the paper mills use a high percentage of recycled paper and the resulting paper sludge contains paper fibers that are too short to be further recycled into paper or cardboard. To convert the SPF into a soil product that can reclaim land and grow crops is truly closing the loop.”
Poirier adds that MassDEP has approved a number of gravel pit reclamation projects using Type II (Class B) biosolids. “I had direct experience permitting Type II sludges for land application, and those were typically gravel pits that were then seeded with grass. However, due to restrictions on use of the site, the vegetated pits were typically not used for any agricultural purpose, but were being reclaimed to prevent soil erosion.”
In the spring of 2012, Foster decided to plant a hay crop in some of the fields that had previously had corn, and he is pleased with the results. “I am now rotating the fields with corn and hay, and continuing to increase the total number of acres of reclamation,” he says.
Page notes that he is working with Foster and some other farmers to start growing oil seed crops, such as canola and sunflower, on the reclaimed land. “Just as the high cost of diesel fuel has adversely impacted the farming business, it is also hitting composters like me that operate large front-end loaders, trucks and screening equipment,” he says. “I am looking into the possibility of planting oil seed crops so that I can press the seeds to recover oil that can be refined into biodiesel to run my equipment.” Page, who also maintains a herd of beef cattle at his composting facility, explains that after the sunflower seeds have been pressed, the remaining material makes a high-nutrition cattle feed that will further reduce operating costs.
Robert Spencer is a Contributing Editor to BioCycle.