A HAZOP analysis examines each step or unit operation in the AD manufacturing environment to explore possible ways that either partial or total failures can occur.
Craig Coker and Nellie Brown
BioCycle May 2016
Anaerobic digestion (AD) is a biological manufacturing process whereby organic feedstocks (wastes, animal manures, sludges, cultivated energy crops, etc.) are transformed by microorganisms through a multistep process to make immediate products such as biogas and future products like digestate. As with any manufacturing facility, there are health and safety risks due to moving equipment, operating machinery and human error.
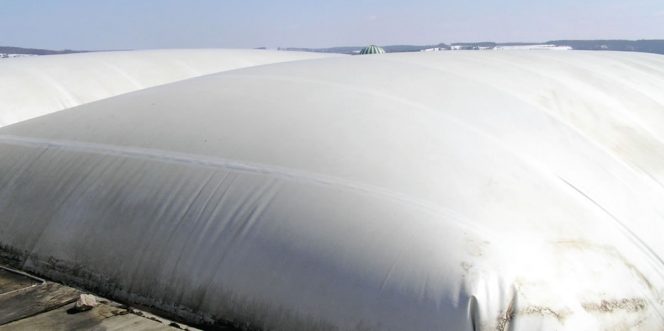
A HAZOP attempts to answer the question, “how can things go wrong here,” e.g., location of a flammable hazard near an anaerobic digester’s rubberized gas storage bladder. Photo courtesy of Nellie Brown
The particular nature of biogas production requires consideration of environmental, health and safety issues that go beyond just moving machinery and electrical lock-out/tag-out to include measures to avoid asphyxiation hazards, fire and explosion hazards, and accidental releases of biogas or digestate. These types of hazards, along with the conventional hazards of manufacturing, can be addressed in a Hazard and Operability Analysis (HAZOP) and in a Job Safety/Hazard Analysis. This article explores how to do a HAZOP Analysis.
What Is A HAZOP?
HAZOP is a process failure analysis technique that examines each step or unit operation in the AD manufacturing environment to explore possible ways that either partial or total failures can occur. Essentially, it attempts to answer the question, “How can things go wrong here?” HAZOP analyses examine manufacturing from both an operations and a maintenance perspective separately, and for each component, consider potential causes of problems (called a “deviation” in HAZOP language), the possible consequences of those problems should they occur, and what preventive measures or actions might be warranted to minimize the possibility that a deviation will occur. Potential causes of a deviation include: human error, design problems, fire or explosion, natural disasters, power failure, sabotage or vandalism, and terrorism. Potential consequences of a deviation would include: human injury or illness, environmental contamination, damage to property, lost or contaminated product(s), monetary losses and loss of time.
Standards exist in European countries for doing a HAZOP analysis. The International Electrotechnical Commission (IEC) published the HAZOP standard in 2001, and the second edition updated version was published in March 2016. In the U.S., the Occupational Safety and Health Administration (OSHA) requires HAZOP analyses every five years for processes involving “highly hazardous chemicals”, however that list of chemicals does not include methane (see 29 CFR Part 1910.119 Appendix A). OSHA also publishes several guidance documents for conducting a HAZOP analysis.
When To Do A HAZOP
The timing of a HAZOP study is determined by the objectives of a study, which in turn, determine the benefits that may be gained. A project may be studied several times during the development process and during operations. The concept design of a process may be examined to highlight any major omissions or significant features. As further design work is carried out, e.g. when the process design is complete, the full study may be appropriate.
“We approach this via our overall project execution model called XPM (Xergi Project Model),” explains Michael Hansen, Sales Manager for the Danish AD technology provider, Xergi. “This model describes what we do over the lifetime of an AD project from contract/initiation through final commissioning. There are a number of gates with conditions that need to be fulfilled before entering the next phase. For example, in the Detailed Design phase, a HAZOP is part of the design review to meet the Gate 5 Criteria. Our HAZOP is done according to IEC/EN 61882 ‘Hazard and operability studies (HAZOP studies) – Application guide’.”
Operating procedures may be examined to ensure that all eventualities have been considered. Modifications, including so-called “minor modifications,” can benefit from a HAZOP analysis. An apparently simple, uncomplicated modification can offer insights to a greater problem than the original modification was intended to solve. Existing plant operations and new equipment are other examples of topics that may benefit from analysis.
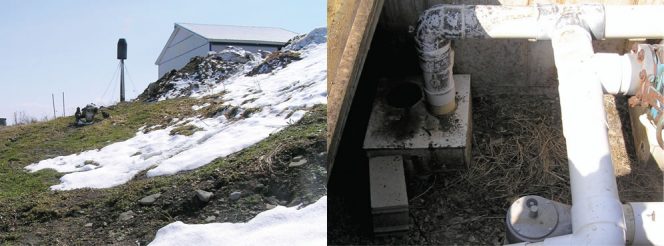
Incidents, such as an episode of reverse gas flow from the biogas flare (left) igniting and scorching PVC gas piping (right), illustrates how a unit can deviate from expected performance. Photos courtesy of Nellie Brown
HAZOP Techniques
The HAZOP technique consists of using plant layouts or process flow diagrams for future or existing processes, then breaks down plant operations into units, describes how a unit can deviate from expected performance, explores the causes and consequences of deviation, and explores corrective actions to prevent the deviation from occurring.
A diverse team of individuals is usually assembled to conduct the HAZOP, including management, design engineers and scientists, operations personnel, and maintenance staff. For each process in the manufacturing environment — e.g., materials receiving and preprocessing, anaerobic digestion, biogas capture and conversion — the team evaluates operational questions such as: “If this operation were successfully done, how would you know? Similarly, how would you know if this operation was not successful due to partial or total failure? How could people be injured, made ill, or otherwise be adversely affected by partial or total failure of this operation? What environmental impacts could be anticipated from partial or total failure of this operation?” Corresponding questions would be evaluated with regard to both routine and nonroutine maintenance of the equipment used in that particular process.
The HAZOP technique explores both quantitative and qualitative failure modes, and aims to stimulate the imagination of participants to identify potential hazards and operability problems; structure and completeness are given by using guideword prompts. In order to identify deviations, the team applies (systematically, in order) a set of guide words to each section of the process. Guide words should be chosen which are appropriate to the study and neither too specific (limiting ideas and discussion) nor too general (allowing loss of focus). A fairly standard set of guide words is shown in Table 1.
HAZOP-type studies may also be carried out by considering applicable guide words and identifying elements to which they are applicable or by considering the parameters associated with plant elements and systematically applying guide words to them. Table 2 gives an overview of commonly used guide words — parameter pairs and common interpretations of them.
This sequential and structured approach is applied to each step in the biological manufacturing process. For example, one of the processes in AD is the distribution of biogas from gas storage to biogas conditioning. Table 3, prepared by Unison Solutions for representation purposes only, shows how these guide words are used to evaluate and assess various “what if?” scenarios for biogas conditioning systems.
The HAZOP process is not without its critics, which is not unusual for any multiperson, multitask team planning effort. Common complaints about the process include: failure to identify potential hazards early in the design process, excessively long checklists, lack of team agreement about the scope of a HAZOP analysis, and classic multiperson team issues (poor listening, defensive attitudes, etc.).
Notwithstanding these criticisms, a HAZOP analysis is time well-invested to ensure that an AD facility can be designed, built and operated with minimal potential for a health and/or safety incident. This type of analysis can also help local first responders understand how to deal with emergencies at the facility. HAZOP can be used to capture the knowledge of a workforce before people retire (taking their experience with them), as well as to train new hires who can benefit from the knowledge of experienced coworkers, as well as see a process from a variety of points of view.
Craig Coker is a Senior Editor at BioCycle and a Principal in the firm Coker Composting & Consulting (www.cokercompost.com), near Roanoke, Virginia. He can be reached at ccoker@jgpress.com. Nellie Brown is a Certified Industrial Hygienist and the Director of Workplace Health and Safety Programs for the Worker Institute at Cornell University’s School of Industrial and Labor Relations. She can be reached at njb7@cornell.edu.