Municipalities in this Minnesota region offer food scraps collection to households using a voluntary participation approach.
Dan Emerson
BioCycle May 2017
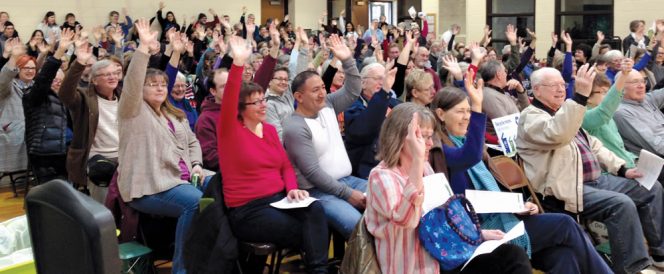
Residents at a Minneapolis open house raise their hands if they signed up for the city’s residential curbside organics collection service. Households receive a 32-gallon organics cart.
In 2016, 13,100 tons of food waste and food-soiled paper were collected. Almost all came from the commercial sector. To increase the quantity diverted, the county plans to allocate more of the recycling funds it receives from the state for the purpose of organics recycling. “By 2020, half of our funds will be available for organics recycling, compared to 8 or 9 percent in 2016,” notes Knudson. “That’s the direction we want to go in.” To provide an incentive for haulers, the tipping fee for food waste at the Brooklyn Park Transfer Station is $25, compared to $55 for trash.
The county’s food scraps recycling program for businesses offers technical assistance, signage and grant funding to help add or improve recycling or organics programs. Institutions, multifamily units and office buildings are included in this program.
Several municipalities in Hennepin County have dabbled in curbside collection of residential food scraps for many years. Several, including Minneapolis, now offer curbside service citywide. More recently, additional municipalities have launched residential programs.
Evolution In Minneapolis
Organics recycling in the City of Minneapolis began in 2008, with a pilot project requested by a group of residents in the Linden Hills neighborhood, according to Kellie Kish, the city’s recycling coordinator. Food and food-soiled paper, compostable products, and other items such as tissues, cotton balls and Q-Tips were collected. The City distributed 64-gallon vented carts for the pilot program. In 2009 and 2010, the pilot program was expanded to parts of seven additional neighborhoods to utilize one collection vehicle every day of the week. By the end of 2010, about 2,500 of the 5,000 neighborhood households eligible to participate were separating their organics for composting.
In 2014, Minneapolis decided to expand the program citywide in phases, based in part on its experience rolling out a single stream recycling program in 2013, Kish notes. “During that process we found there was big value in doing it in phases — some in the fall and then in spring. We found out about any small issues and made a plan to correct them during the winter.” In 2015, 25 percent of Minneapolis households could receive curbside collection; in 2016, it was rolled out citywide for residents who want to opt-in for curbside service.
“Before purchasing carts for the citywide curb and alley collection program, we surveyed those in the pilot areas to determine if a 64-gallon cart was necessary or if they would prefer a smaller cart; 72 percent of respondents said they’d prefer a smaller cart,” explains Kish. “Based on this information and feedback from collection crews, we selected 32-gallon carts for program expansion.” The City delivered 32-gallon carts to all households who signed up to participate with one to two dwelling units and automatically delivered a 64-gallon cart to properties with more than two dwelling units. Residents in one to two unit buildings could request a 64-gallon cart if they preferred.
City staff spends “a lot” of time and energy going to neighborhood events and developing big educational campaigns and doing direct mailers, she adds. This has paid off, based on the “very clean” condition of the City’s organics. Plastic-lined paper items pose the only potential glitch. “For the most part, residents really understand the program,” Kish says. “And with it being an opt-in program, people want to do right thing. We’re also lucky to have two-person collection crews. They look in every single cart and if there is contamination, they leave an educational tag so the resident will know there was an issue and what it was.”
The program has a 41.7 percent signup rate, which equals about 44,500 households, with more people signing up daily. The City mails out a welcome kit with how-to tips, a starter set of compostable bags and coupons to buy more bags, kitchen collection containers or compostable food service items. Minneapolis also opened residential drop-off sites for residents who do not want curbside service but want to divert their food scraps (see sidebar).
Collected organics are transported to a private transfer station, then hauled to Specialized Environmental Technologies’ (SET) composting facility in Empire Township in the southeast Twin Cities metro area. Achieving a cost-effective volume of organics has not been a problem for SET’s facility, Kish adds, since it receives “a lot” of commercial organics as well. A portion of the compost SET produces is returned to the city, for use in community gardens.
At this time, Minneapolis is not considering mandatory organics diversion, Kish notes. “We are in the initial stages of developing a zero waste plan and there are many other aspects that need to be addressed before considering mandatory organics collection for all residents. For example, residents are not currently required to recycle. It’s possible the topic may be brought up for high quantity organics generators in the near future, as the state and counties work on their Solid Waste Master Plans.”
St. Louis Park
The Minneapolis suburb of St. Louis Park has the second largest organics recycling program in Hennepin County. Since launching the program in the fall of 2013, St. Louis Park has slowly seen participation increase to about 15 percent of households — about 2,300 out of 12,300 residential solid waste program customers, according to Scott Merkley, public works services manager. The city’s goal is to double participation in 2017. Each household contributes an average of five to eight pounds of organic material each week. And effective January 1, 2017, the city made a program change to include organics recycling as part of the base cost for garbage collection and eliminated the additional $10/quarter cost for organics recycling.
One element that makes the St. Louis Park program unique in the county is that residents are also allowed to deposit food scraps and food-soiled paper — contained in compostable bags — with yard trimmings in the curbside carts supplied by the city. Residents can choose either a 30, 60 or 90 gallon cart for weekly pick up; most have opted for the 30 gallon carts, if they are not also using the cart for yard trimmings. Organics collection also is being done at city buildings.
St. Louis Park’s contractor, Advanced Disposal, cocollects organics and yard trimmings weekly. The material is brought to the SET facility in Empire Township to be composted. Twice a year, SET delivers compost to the city. It is first offered to residents who participate in the organics recycling program, and then to residents in general.
“As with any educational program, we recognize that we have to continue to educate people; it takes a lot of different ways to keep a new idea at the forefront for people,” Merkley explains, adding that face-to-face communication at community events has been the most effective method. The city has no plans to make organics recycling mandatory, and intends to keep it as an opt-in program. “We believe opt-in participants will do a better job in keeping the organics recycling stream clean from contamination,” Merkley notes.
The Hennepin County suburbs of Wayzata and Medina use the Blue Bag Organics program to collect organics. Residents put food scraps in compostable blue bags and place the bags in with the trash. The bags are sorted from the trash after delivery to a transfer station and then sent to a composting facility. Medina’s assistant city administrator, Jodi Gallup, explains that the city originally tried a cart system, with collection done by a dedicated organics truck. Starting the Blue Bag Organics program in 2013 has enabled the city to have “one less truck on the road, a huge selling point,” she says. “And, residents really like having the Blue Bags instead of carts.”
SET Composting
Food scraps composting at SET’s 37-acre facility in Empire Township takes place on a 4-acre area with an impervious clay liner, according to Anne Ludvik, SET’s director of organics policy development. Except for St. Louis Park, food scraps are collected separately from yard trimmings. Commingling has caused some challenges with SET’s process and equipment. “Under state regulations, just one bag full of food waste mixed in a truckload of yard trimmings would require handling on the 4-acre pad with the clay liner,” Ludvik explains.
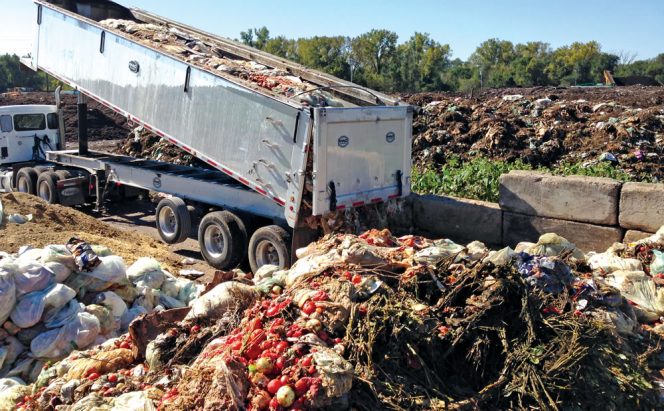
An organics load from Hennepin County is tipped at the Specialized Environmental Technologies, Inc. (SET) composting facility in Empire Township.
SET’s rejection rate due to contaminated material has been as low as 1.5 percent, but as more organics recycling programs have come on-line, that has increased by two to five percent. “Last year it was 11.9 percent, so we have hired a full-time load inspector,” Ludvik notes. “We’re also changing some policies with some additional fees on the waste haulers. Some of it is due to the need to reeducate people about not including plastic and wax coated paper and cardboard.”
To facilitate contaminant removal, SET uses a Penta agricultural feed mixer to blend the food scraps and yard trimmings. The mixer spins at a slower speed than a grinder, so plastic and glass are easier to remove before they are shattered into smaller pieces. “If someone has thrown a glass or plastic bottle into the material, the ag mixer keeps it intact so we can remove it,” she says. The site has been handling about 16,000 tons of food scraps, food soiled paper and BPI-certified compostable foodservice items annually. That quantity is expected to increase with expansion and reconfiguration of the site, Ludvik adds.
SET positively aerates its windrows containing food scraps, which are about 12-feet tall and from 150- to 175-feet long, handling up to 12 at a time. Positive aeration eliminates the need to turn the material during the most active phase of composting, and prevents odor problems. Screened, unfinished material is used to cover the top of the pile, acting as a biofilter. “We haven’t had any odor complaints in six years and we only had one prior to that,” Ludvik notes. The mixed material is placed on 6-inch perforated PVC pipes used to aerate the material, for about 45 days. To save energy, the system blower has a timer that turns it on and off as needed. The temperature of the pile is checked daily to make sure it meets pathogen reduction requirements. After material is taken off the aeration pipes, it is cured for an additional 3 to 4 months; material is turned about 3 times with a front-end loader.
BPI-certified compostable plastic products break down in the first phase of composting (when temperatures are higher). Paper products continue to break down later in the process, at lower temperatures. SET’s policy of accepting these materials helps divert more food waste to composting, Ludvik adds.
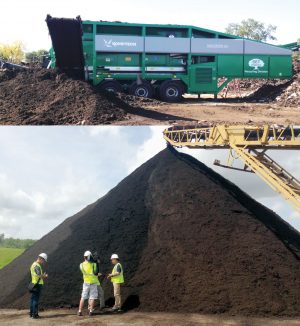
Finished compost (above) is screened to a half-inch using a Komptech L3 Multistar Screener (top left), but SET can go smaller if customers have specific requirements.
SET has worked with a few local retailers to sell its products in bulk at their locations. It’s also sold in bulk to some retailers that bag and package it under their own brands, locally and nationally.
Joswiak has been working with the Minnesota Pollution Control Agency and Minnesota Department of Transportation, to amend their compost specifications — which currently do not allow compost made using food residuals as part of the feedstock — for erosion and storm water management applications. This end product sometimes has more contaminants or “inert” material than yard trimmings compost, but it still falls within the current guidelines for their yard trimmings only specification, Joswiak explains.
He is also trying to spread the word about compost’s role in water conservation and the vital soil-water connection. Filtering pollutants from runoff water, e.g., from construction sites, and also improving soils’ ability to retain water and reduce the need for fertilizer, are just a few of the many benefits of utilizing compost on a bigger scale, he adds.
New Minnesota composting regulations will make it easier for SET to expand its facility’s food scraps composting capacity. The new rules will allow SET to move its curing pile off of its 4-acre impervious surface, as long as it meets the state’s maturity requirements. “This will almost double our capacity for processing source separated organic materials, without the need to add additional impervious surface,” Ludvik explains.
Dan Emerson is a Contributing Editor to BioCycle.