Forty-year old farm and composting operation is guided by the intention of creating a place to grow food and make a product that enriches the soils of New England.
Nora Goldstein
BioCycle May/June 2019
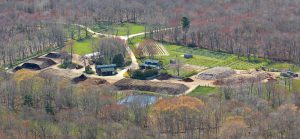
The composting site at Earth Care Farm is on 3 acres of the 30-acre farm. Photo courtesy of Earth Care Farm
Last fall, Jayne Merner Senecal of Earth Care Farm wrote a letter to Sally Brown after reading Brown’s Connections Column, “Back To Composting School” (September 2018). The column reviewed the “3 T’s” — temperature, turning and time — that are the keys to making high quality composts. “I have noticed a shift (or maybe a split) in the compost industry’s intentions from making a well-made compost to waste handling,” Senecal wrote. “It’s a small difference but has a major impact on how the site is treated and the product is created.”
Senecal runs her family’s 40-year old, “high quality compost farm” in Charlestown, Rhode Island. “My father, Michael Merner, started the farm with the intention of creating a beautiful place to live, grow food and make a product that would enrich the soils of New England,” she continued in her email to Brown. “He has done just that. I am honored to live here with three generations of family and continue his work. We take in approximately 75 tons/day of varied feedstocks ranging from food scraps, manures (from farms and zoo), fish, shellfish, seaweed, leaves, wood chips, coffee grinds, tea leaf and bedding. We use our own system similar to a windrow system although we have larger block piles and we turn using front-end loaders rather than a windrow turner. We find the slower turning method leads to more biological diversity in our end product.”
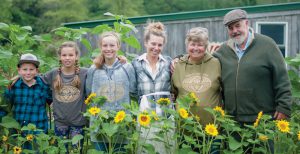
The 40-year old family business was started by Michael and Betty Merner (far right), and is now owned by their daughter, Jayne Merner Senecal (3rd from right). Also pictured are several of the Merner’s grandchildren (from left to right, Cooper, Caitlyn and Kaleigh). Photo by Taylor Cann
Michael and Betty Merner bought the 30-acre farm in 1977 during the back-to-the-land movement. Although Merner studied turf management at the University of Rhode Island, his formal education was at odds with the social and environmental mindset in the 1970s. He started a landscaping business after buying the farm but turned an ear to the prechemical, older farmer generation, reading publications like Organic Gardening and Mother Earth News. Merner was struck by the message that soil health is the foundation of plant and human health. His focus was on building healthy soil through making compost. .
The landscaping business changed in the early 1980s to using only organic practices. Merner built a reputation for his creation and management of beautiful, chemical free lawns. As a result, recalls Senecal, “he needed to make more compost.” Merner phased away from the landscaping business to begin manufacturing compost on a full-time basis in 1990. At the time, the state of Rhode Island did not have any licensing or regulations for composting operations.
“My father spent a lot of time in the 1990s helping the Department of Environmental Management (DEM) draft composting regulations and standards,” notes Senecal. As an agricultural operation, Earth Care Farm has its license to compost from the state’s Division of Agriculture, which is within DEM.
Senecal grew up on the farm, and started a CSA (community supported agriculture) on the property. In 2002, she launched Golden Root Gardening, a landscaping and garden maintenance business. “We tend over 50 gardens in the local area,” she says. “I’ve always been fortunate as I’ve had an abundance of compost to use!”
In 2016, Merner began the transition of passing ownership of the farm to Senecal, starting with becoming business partners. In 2018, she took over full ownership of Earth Care Farm. The company has 5 employees for the composting operation — 4 full-time and 1 part-time. “We manufacture about 5,000 cubic yards (cy) of compost annually, and are edging toward processing 100 tons/day of material,” she explains. “We have a steady stream of landscapers, farmers, businesses and towns bringing us material, and not all loads coming in are weighed. The rich marine inputs of seaweed, shellfish and fish scrap, as well at the local zoo’s animal manure and bedding, are some of the inputs that are unique to our compost.”
Compost Manufacturing Process
Three acres of the 30-acre farm are used for the composting operation. Senecal outlines Earth Care Farm’s composting manufacturing process, which consists of 6 areas: Staging, Mixing, Turning, Maturing, Screening, and Sales. The company’s Production Goal, she says, is “to create a highly nutritious soil amendment that will enrich gardens without adding weed seeds or pathogens. Compost product sales comprise 72 percent of our income, with 28 percent generated by tipping fees.”
Staging Area. Primarily carbonaceous material is accumulated. This material varies slightly depending on season and availability, but includes wood chips, leaf/yard material, sawdust, animal bedding, spent coffee grinds and tea leaf, and coffee bean chaff.
Mixing Area. Carbonaceous material is formed into a pad for nitrogen rich material to be unloaded onto on a daily basis. Nitrogenous material feedstock consists of shellfish/fish gurry, food scraps, seaweed, and manures (manures are primarily received premixed with bedding and are accumulated in the carbonaceous material Staging Area). When the nitrogenous material is dumped, it is visually inspected for potential inorganic contaminants such as plastics, glass and metals that are removed by hand.
Using loaders, the nitrogenous feedstocks are covered and blended with carbonaceous material. These are bulked up with more carbonaceous material as they are incorporated into the Turning Area pile, until a general ratio of 25:1 to 30:1 carbon to nitrogen is achieved. A carbon biofilter layer is then applied to the outer surface of the newly mixed material to prevent odors and fly problems. The resulting piles, created by loader bucket, end up being block shaped with dimensions of approximately 100-feet long by 70-feet wide by 12-feet high. Pile size varies depending upon the amount of material accumulated in 3 to 4 months.
Turning Area. Composting material is turned using a large block/windrow style system. Earth Care Farm uses front-end loaders with buckets that hold 5 cubic yards of material that is picked up in the bucket, slowly dumped in place twice to aerate it, and then brought to the already aerated portion of the pile. This aeration results in thermophilic conditions. The piles are turned using this method approximately every 3 weeks for 4 to 6 months.
During the initial turning stages, operators record representative sample temperature data by probing a portion of the composting material with a 3-foot Reotemp temperature gauge. Soon after turning, temperatures of the composting material rise to 131° to 160° F for a minimum of three days. These thermophilic temperatures ensure sterilization of weed seeds and pathogens.
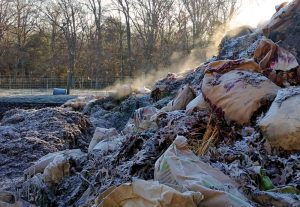
Primarily carbonaceous material is accumulated in the staging area. It is used to form a pad for nitrogen rich material that is unloaded on a daily basis. Photo courtesy of Earth Care Farm
Maturing Area. Compost is stored in the maturing area once it has transitioned from thermophilic to mesophilic temperatures. The mesophilic compost is turned about once a month for 6 months to keep conditions aerobic.
Screening Area. Finished, mature compost is run through a Komptech M2 multistar screener. Screening is performed at mesophilic, or lower, temperatures. Coarse material (larger than a half-inch in particle size) is mechanically separated by size exclusion from fine material.
Sales Area. Fine, screened compost is brought to the sales area for further maturation time (2–6 months) and ultimately sold via bulk wholesale or retail. Coarse material (tailings) is either rescreened or used as fill for revegetation in local gravel banks.
General Site Management
The general site management goal, explains Senecal, is to “maintain a composting site that is efficient for production, manages water flow with respect to the surrounding environment, and is safe.” She outlines key elements of Earth Care Farm’s practices to achieve that goal:
Berms and Swales. Intentionally designed mounds and grades of gravel that determine where the rainwater flows. Must be regularly monitored for effectiveness and added to as they wear down over time. Berms around the pad keep runoff water flowing off the compost piles and into the site’s retention ponds.
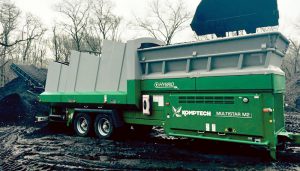
Purchasing a Komptech star screen was a “game changer” for Earth Care Farm, says Senecal, enabling the operation to screen year-round instead of only in July and August. Photo courtesy of Earth Care Farm
Pad Maintenance. Earth Care Farm’s pad is made out of “lots of sandy gravel,” notes Senecal. “It’s approximately 3-feet thick after this many years in. We like a finer, silty gravel that packs well. Our pad requires a lot of regular maintenance with all the heavy equipment driving on it. I am always on the look out for better pad options.” She adds that Earth Care Farm has “a pretty good trade system with local gravel banks where they take our tailings, and use them to revegetate the gravel banks in exchange for giving us gravel.”
Two key pad maintenance steps are used:
Front Blading: Process of skimming the top of the pad with the flat bucket of the loader. Front blading should be done to remove excess compost from the pad at the end of each day — before back blading begins.
Back Blading: Process of smoothing out the areas around the compost piles to avoid divots where rainwater can collect and treads where mud can freeze in cold weather making a bumpy pad. Should be done regularly, and daily in wet conditions. “”Standing water that puddles around the feet of the piles creates anaerobic conditions for the compost so we do a lot to prevent that,” says Senecal. “Those puddles also become mosquito and fly habitat that we don’t want either.“
Pond Maintenance. Included in the plan are:
- Pump regularly onto farm pastures to keep water level low in ponds.
- Monitor bottom of pond for filling. Will need to be dredged every few years.
- Monitor pond retaining walls. Walls will need reinforcement periodically.
- Order new parts for pump as needed.
Weed Management. Monitor and remove/mow/graze vegetation that has seed heads that could blow into the finished compost. (Earth Care Farm has 7 acres of pasture grass where the beef angus cattle it raises are grazing.) Also monitor compost piles weekly for weeds growing on the edges and tops of piles.
Litter Control. Police the loads coming in and the existing piles on a regular basis for inorganic litter. Inform feedstock sources if persistent inorganic litter is found within the incoming material.
Compost Markets
Purchasing the Komptech star screen in 2016 was a game changer for Earth Care Farm. “Screening was a bottleneck for us for years,” explains Senecal. “We were only able to screen in July and August. Now, we can screen year round and can change how fine we want the screening based on the speed of the PTO (power take-off).”
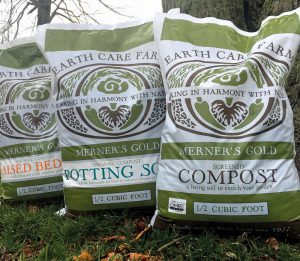
Primary markets for the farm’s OMRI-certified bagged products are in Rhode Island, Massachusetts and Connecticut. A Rotochopper Go-Bagger unit is used to fill the bags. Photo courtesy of Earth Care Farm
Demographics and land development have led to changes in the farm’s compost customers. There are fewer farms in the area, so fewer buyers in the area for bulk wholesale compost. “Another change is that for years, everyone owned a pick-up truck,” she says. “Now, fewer people do.”
These changes led Earth Care Farm to focus more on retail sales. In 2016, the company purchased a Rotochopper Go-Bagger unit. It previously had been bagging compost by hand. “We can get a bigger reach this way,” notes Senecal, adding that it wasn’t until 2018 that the farm really began to focus on bagging. “We bagged about 120 cy of compost, and plan to do more in 2019. Our primary markets are in Rhode Island, Massachusetts and Connecticut. Bagged compost and blends are available in a 0.5-cu.ft. bag and 1-cy sling. In addition to selling its OMRI certified organic compost, Earth Care Farm has a Raised Bed Mix, Potting Soil and Kind Earth (a cannabis grow blend).
Bagging also makes sense from a profit margin standpoint, she adds. “We have an intentionally slower, craft style of making compost with great diversity of feedstocks. It’s difficult to compete with the prices of the composts made only from municipal yard materials. Our price on the bulk material ($66/yard) is more than twice the cost of the Rhode Island Resource Recovery Corporation’s (a quasi-public agency) yard trimmings compost, and we have a slim profit margin even charging so much more. Most people recognize that you get what you pay for. Bagging has allowed us to have a healthier profit margin.”
Last December, Earth Care Farm had a booth at the Bionutrient Food Association’s annual Soil & Nutrition Conference. Senecal brought along a sample of the farm’s compost and produce (carrots and greens) to be analyzed for bionutrient content. “Nutrients identified correlated with some of the feedstocks we compost,” she explains. “For example, a high level of calcium was detected, which is likely due to composting shellfish.”
Reflecting on her journey from her childhood on the farm to where she is today as owner of Earth Care Farm, Senecal goes back to why she reached out to Sally Brown last fall after reading her Connections column in BioCycle: “I have the same intentions my Dad has always had — to make a very good quality compost that is used extensively on our own farm. To us, the fundamental question we all must ask is: ‘Do we see ourselves as waste managers or stewards of our planet’s health?’ This question will affect the way our sites look, the employees we attract, our long-term economic health and the quality of our finished composts. At Earth Care Farm, we have intention behind what we do, versus operating as a waste handler that takes organic materials. The consequence of manufacturing compost in an intentional way is to make the best end product.”