Housed inside a 100,000 sq. ft. building at the southern edge of the San Francisco Bay, a dry fermentation AD system with composting bays is processing commercial organics from the City of San Jose.
Nora Goldstein
BioCycle March/April 2014
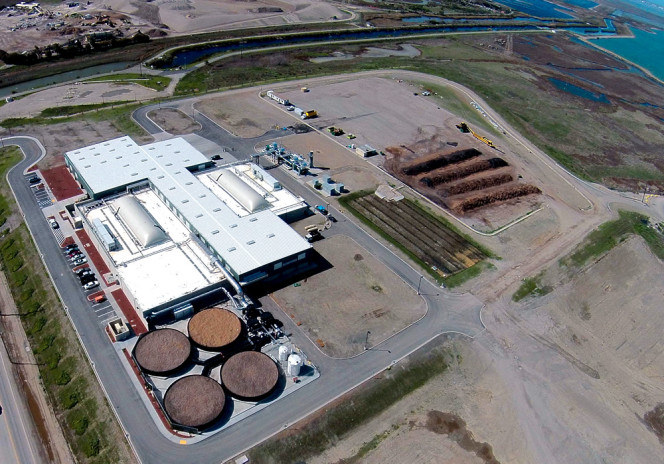
Aerial photo highlights the processing building, biogas storage bladders (on left and right on roofs in center of photo) and the four circular biofilters (bottom of photo) treating building air. The outdoor windrow composting curing pad is on far right.
A facility that marries dry anaerobic digestion and composting under the same roof to process the organic fraction of municipal solid waste opened for business late last year at the south end of the San Francisco Bay in San Jose, California. Zero Waste Energy Development Company (ZWEDC) — developer and owner of the 90,000 tons/year facility — recognized the benefits of colocation to enable extraction of the energy value of the food waste, followed by composting of the digestate. The plant, comprised of 16 high-solids dry fermentation digesters and four in-vessel composting tunnels, began receiving organics from the commercial sector in San Jose in mid-December.
ZWEDC was formed in 2011 by Green Waste Recovery, Inc. (GreenWaste) and Zanker Road Resource Management (Zanker) to bolster organics recovery infrastructure in San Jose. “We already operate the second largest composting facility in California that processes a large portion of the city’s organic waste stream,” explains Rich Cristina, president of GreenWaste and Zanker, referencing its Z-Best Composting Facility in Gilroy, about 30 miles away from San Jose. “Extracting and utilizing the energy value of the organic materials to power our other resource recovery operations here in San Jose was the next evolution for our family of companies.”
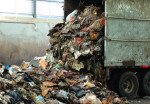
Commercial organics that have been processed by Republic Services at its MRF on Newby Island arrive in walking floor trailers and are directly loaded into the digesters.
Biogas from the anaerobic digesters powers a combined heat and power (CHP) plant that wheels electricity to Zanker Road Resource Recovery Operation and Landfill (ZRRROL), which recycles and processes wood waste, asphalt shingles, sheet rock and other segregated materials. Zanker underwent an electrification project at
ZRRROL, as well as its nearby Zanker Materials Processing Facility. Older diesel-powered stationary processing plants were replaced with electric powered equipment. ZRRROL is utilizing electricity from the CHP for its electric-powered equipment. “We are able to wheel power to ourselves without acting like a utility,” notes Emily Hanson, GreenWaste’s Director of Business Development and Communications. “The plan is for Zanker’s materials processing facilities to use 100 percent of ZWEDC’s peak power after the AD/composting plant covers its parasitic load. When the Zanker plants are not operating, the excess power will be sold to the grid.”
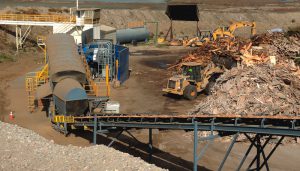
A portion of electricity generated by the CHP units is wheeled to the Zanker Road Resource Recovery Operations and Landfill — which processes segregated materials such as wood waste and asphalt shingles — to power stationary equipment such as the Peterson horizontal grinder on left of photo.
Project History
Origins of the ZWEDC anaerobic digester (AD)/composting plant date back to the City of San Jose adopting a Green Vision goal in 2007 that included diversion of 100 percent of the city’s waste from landfill by 2022 and conversion of waste into renewable energy. At the time, one-third of the City’s landfilled waste stream came from businesses, and city officials recognized that significant changes in this sector were necessary to improve the commercial recycling rate of 22 percent at the time. San Jose had an open franchise commercial waste collection system; over 20 different haulers serviced the more than 8,000 commercial, industrial and institutional waste generators in the city. To help meet its Green Vision goal, the City Council voted to institute an exclusive franchise agreement and select processors for the materials collected. A waste characterization study conducted in 2008 indicated that nearly 79 percent of the commercial solid waste could be diverted through recycling and composting.
Two Requests for Proposals were issued in 2010, one for commercial organics processing and the other for commercial solid waste and recyclable material collection and processing. ZWEDC was awarded the organics processing contract, while Allied (now Republic Services) was awarded the collection and recycling contract. (See “New Frontier For Commercial Waste In San Jose,” May 2011 and “Creating Infrastructure For Commercial Waste Diversion,” August 2011 for details on the RFP process and final contracts negotiated with ZWEDC and Republic). It was anticipated that the new contracts would increase the commercial diversion rate up to 80 percent by 2014, which is 5 percent higher than the city’s goal of 75 percent diversion by 2013.
The official start date for the new collection and materials processing services was July 1, 2012. Republic opted for a wet/dry collection service, providing customers with several options, e.g., one container for wet material (organics) and one container for dry materials (recyclables and everything else). Smaller businesses can use one container — they can either put organic waste in loose in the container and bag the dry trash and recyclables or they can put dry trash and recyclables loose in the container and bag the organic waste. “One of the most significant benefits of the wet/dry system is that all businesses in San Jose are in compliance with AB 341, a California mandate requiring businesses that generate at least four cubic yards of waste per week to recycle,” explains Gil Cheso, General Manager of Republic Services of Santa Clara County. “The only thing businesses need to do is determine if material is wet (organics) or dry (recyclables and everything else) and place it in the correct container.” Processing capacity at Republic’s Newby Island Resource Recovery Facility was expanded to accommodate an organics sorting line for the incoming wet fraction.
The contract negotiated by both Republic and ZWEDC with the City of San Jose established four levels of contamination in the “Organic Material Delivered by the Commercial Collection Franchisee (CCF).” The tipping fee rises according to the level of contamination in the “organics stream” (OS) loads delivered. Contamination levels (by weight) in the OS are divided as follows: OS 1: ∂5 percent; OS 2: .5 percent and ∂10 percent; OS 3: .10 percent and ∂20 percent; and OS 4: . 20 percent and ∂30 percent (similar to unprocessed MSW). The tipping fees range from about $70/ton for OS 1 to the mid-$90s/ton for OS 4. These rates are very competitive in this region of California.
Because Republic launched its wet/dry collection service in July 2012, ZWEDC had to begin processing the organics stream at the same time. The company transferred the wet material to its Z-Best Composting facility in Gilroy, which already is composting a mixed waste stream from GreenWaste’s materials recycling facility. Under its contract with the City, starting on January 1, 2013, ZWEDC was required to achieve a diversion standard for each Organic Stream processed. “The allowable residue per Organic Stream category is based on the maximum allowable contamination in the OS level, plus five percent,” explains Hanson. “For example, OS1 allows 5 percent contamination by weight, so the allowable residue is 10 percent by weight. This is calculated at the end of the year.”
ZWEDC has the right to reject any incoming load determined to contain more than 30 percent contamination, any load containing more than 30 percent paper and/or fiber materials, and any load containing more than 0.25 percent glass.
Digester/Composting Facility Development
Once the contract was signed with the City of San Jose, ZWEDC researched existing technologies and selected Zero Waste Energy, LLC (ZWE), a California-based project development company with the exclusive North American license to the SMARTFERM high solids, dry fermentation anaerobic digestion and in-vessel composting (IVC) technologies developed by Eggersmann, a German company. ZWE installed the Kompoferm technologies in the San Jose facility, which is one of the technology options in its SMARTFERM portfolio. “We were seeking a processing system that was not only a net energy producer, but also required minimal processing, and little water and energy to perform optimally,” notes Hanson. “ZWE’s Kompoferm Plus IVC technology fit that bill.”
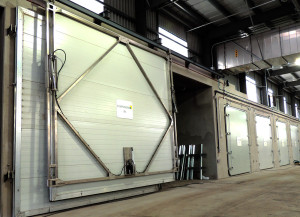
The four in-vessel composting tunnels (one shown on left in photo) are next to one of the banks of digesters (to the right). Content of two digesters fills one composting tunnel.
The ZWEDC team successfully waded through the local and state environmental review and land use permitting and entitlement processes (air, water and solid waste), which covers the current Phase One (90,000 tons/year), as well as planned expansions over the next few years (Phase 2 increases capacity to 180,000 tons/year and Phase 3 — a full build-out of the site — expands to 270,000 tons/year). The project was financed through the California Pollution Control Financing Authority, which issued bonds that were supported by a bank letter of credit, which in turn was supported by the guaranteed 15-year exclusive feedstock contract with the city, and a power purchase agreement with the local utility. “We needed to have these contracts in place to secure the financing and provide assurances that we could service our debt,” says Hanson.
ZWEDC’s organics processing facility is sited on approximately 40 acres of a city-owned former landfill site (known as Nine Par), adjacent to the San Jose/Santa Clara Water Pollution Control Plant and directly between the two existing Zanker processing operations. ZWEDC is leasing the site from the city. “This landfill was a privately owned 166-acre site that operated as an active landfill from 1938-1969,” explains Jo Zientek, Deputy Director of the City of San Jose Environmental Services Department. “The City purchased the property in 1982 to serve as buffer lands for the Regional Wastewater Facility. Changes to the requirements for the City’s wastewater facility negated the need to keep the site for future expansion, and thus enabled development of the Nine Par site. Developing on the site of an older landfill posed many challenges, and the City recognized that it was not in the position to bring the site into a condition where it could be leased for any purpose. The City gave ZWEDC credit towards its rent for the approximately $11 million that the company had to spend to bring the site into a condition from which it could be useable by the City, even if the ZWEDC project did not progress to completion. This way the City would benefit from the site improvements.”
Zientek adds that infrastructure improvements and preparations included topographical and landfill status investigation, design and grading planning, geotechnical reports, wetland delineations, aerial surveys, drainage and irrigation planning, bringing utilities to the site (potable and reclaimed water, power, sanitary sewer, etc.) importing fill and grading the site, installing storm water and forebay protection systems, onsite water treatments, and creating roads and driveways.
Once the credit for site infrastructure improvements is paid back to San Jose, the City will receive about $4/ton of waste into the facility. “Therefore the more material ZWEDC is able to bring into the facility for Phases 2 and 3, the more revenue is generated for the City of San Jose and the other jurisdictions that use the wastewater facility,” explains Zientek.
The receiving area, digester bays, composting tunnels and related operations are housed in an approximately 100,000 sq. ft. fully enclosed building. There are two banks of digesters — eight on each side of the building. Each bank has its own 425,000 gallon percolate tank in the basement and 670 cubic meter (m3) gas storage system on the roof. The building is constructed on a floating base, essentially “rafts” that disperse the weight and prevent the structure itself from getting damaged due to differentiated settlement of the closed landfill. Each digester bank has its own raft, as does the receiving and operations area. (The four composting tunnels are next to one of the banks of digesters.) To allow for percolate tanks under each bank of digesters, the site had to be built up. “Essentially we had to raise everything so that we could dig down,” says Hanson.
The process of meeting the City of San Jose Fire Code was complicated by the fact that dry anaerobic digestion is a new technology in North America with no code precedent. “An occupancy classification of a building determines the construction type and allowable square footages, however since a large portion of our square footage was processing area that would be minimally occupied, we had to come up with some creative solutions to meet fire and building codes without adding exorbitant costs, “explains Hanson. “Working hand-in-hand with the regulatory agencies, we created our own regulatory path by making a distinction between processing areas and occupied areas. The ultimate resolution is that when the digester hatches are closed, the area is classified as ‘processing.’ When the hatches are open, it is classified as ‘occupied.’ To achieve this, the City’s code enforcement officials required additional sprinkler protection in areas that are occupied at all times of operation. Basically, through our negotiations, we have created a model regulatory path for any facility like this in the United States!”
Construction of the facility was accelerated because much of the manufacturing was done in the U.S. “We work with Environmental Solutions Group’s Marathon Division to do our fabrication,” says Dirk Dudgeon, ZWE’s Senior Vice President of Business Development. “In addition, all process controls were assembled in modules and shipped, so it was ‘plug and play’ during installation at the facility. Overall, these steps shaved months off the construction process.”
Design And Operations
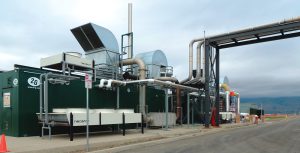
ZWEDC installed two 2G Cenergy 800 kW combined heat and power units. Thermal energy from the engines is used to maintain percolate at thermophilic temperatures.
ZWEDC receives and processes commercial organics six days a week. Each digester tunnel — 18-feet wide by 16-feet high by 97-feet long — holds 350 tons of organic material. Organic Stream 1 loads (∂5% contamination) that are hauled directly from collection routes to ZWEDC are visually inspected for contaminants; some hand sorting is done. Loads that have been processed by Republic at its Newby Island MRF arrive in walking floor trailers. Materials are directly loaded into the digesters with front-end loaders.
Not long after Republic started up the processing line for the wet stream at its MRF, it decided to add a fines screen and a reducer. “The reducer helps size the material and liberates the organics from the plastic bags,” says Cheso of Republic. “All material from that line goes over the fines screen before it is sent to ZWEDC.” The primary contaminants removed are plastic film, food service containers and other plastic items.
For the first six months of operations, Republic has employees on the tip floor working with ZWEDC staff to monitor loads for contamination, and to help gauge the quality of material arriving and properly assign OS classification. In addition, representatives from the City of San Jose visit on a monthly basis to observe operations and monitor material quality. (The city does similar visits to the Republic MRF.)
Because ZWEDC has been processing the commercial organics since July 2012 at the Z-Best Composting Facility, it had a good idea of what to expect in the wet fraction of the commercial waste once the AD/composting plant opened. What was less certain was the how the tonnages to be received would translate into actual volume that would go into each digester. “The digestion tunnels are designed for a volume throughput and a maximum material depth that allow for adequate airspace for both percolate distribution and methane production,” explains Hanson. “This is a projected volume throughput, however, the exclusive feedstock agreement relies on tonnage. The density of the material is going to determine whether the volume throughput is higher or lower than anticipated. The higher the contamination, the lower the density of the material and thus, the weight per unit of volume decreases and the projected tonnage throughput will be reduced. If the material were too dense or wet, however, then a structural/bulking material would need to be added. Currently, the material being delivered by Republic is averaging 800 lbs/cubic yard and the contamination is providing the structure needed, so there is no need to add structural material or bulking agent to the organics going into the digesters.”
The Kompoferm digesters operate at thermophilic temperatures (125°F-131°F) with continuous recirculation of the percolate (liquid rich in anaerobic bacteria that acts as an inoculant to kick start biogas production). After the digester door is sealed, the tunnel operates aerobically to reach the thermophilic range (the initial aerobic process takes roughly 1.5 days). Once at that temperature, the oxygen is purged and the 24/7 irrigation with percolate begins. The percolate tanks are heated with thermal energy from the CHP unit. During commissioning of the plant, liquid manure was brought in as a percolate “starter.” The digester floors have a 1.5 percent slope that helps drain the percolate.
Retention time in the digesters is about 21 days — essentially the amount of time for peak biogas production. Biogas from each tunnel is pushed into the airspace of the percolate tank, combining biogas from each operating digester to yield a homogenous “rich” gas (higher methane content). In turn, the biogas goes to storage bladders on the roof, which then feed two 2G Cenergy 800 kW CHPs. “It is important to maintain an optimal flow of ‘rich’ gas to the CHPs, as that minimizes emissions from the engine, which is critical for our air permit,” notes Hanson.
Composting And Curing
As biogas production decreases, oxygen is introduced into the tunnel; the air is pushed up through the mass to purge all the methane from the material. Volume reduction after anaerobic digestion is about 30 percent. A front-end loader removes the material from the tunnel and takes it to a BHS decompactor designed to both loosen up the digestate and mix in a bulking agent if necessary. ZWEDC also installed a BHS disc screener to remove large contaminants before moving the digestate into the in-vessel composters.
Roughly two tunnels’ worth of digestate fit into one in-vessel composting tunnel. Material is composted in the vessels for four to five days, primarily to remove ammonia and reduce odor compounds prior to curing outside in windrows. The air pulled through the building for air exchanges (3/hour) is forced through the material in the composting vessels to provide aeration before passing through two acid scrubbers designed to treat 35,000 cubic feet per minute (CFM) of exhaust air. The scrubbers use sulfuric acid to chemically react with ammonia from the compost tunnels to produce ammonia sulfate, a liquid fertilizer. Over 90 percent of the ammonia is removed, along with particulate matter and odor compounds. In the last step, air is distributed to one of four biofilters (each 52-feet in diameter) containing a mix of wood chips and finished compost.
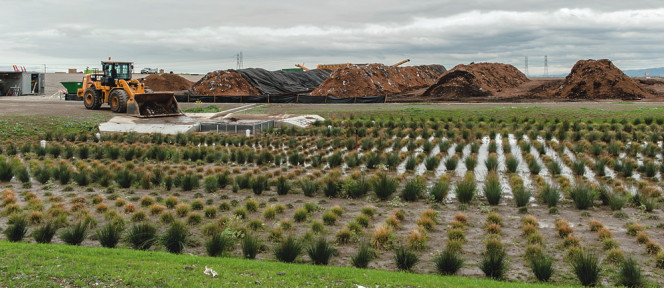
Material from the in-vessel composters is moved to an outdoor curing pad. All water draining from the site flows to a biotreatment containment area (foreground).
After in-vessel composting, material is moved to an outdoor curing pad that is built from crushed recycled rock from the adjacent Zanker resource recovery facility. Compost cures for four to five weeks after which it is screened to three-eighth-inch minus with a Vermeer trommel. All water draining from the site flows to a biotreatment containment area.
Initial Results
As of mid-February, all eight digester tunnels in the initial phase were filled and operating. (The second bank of eight digester tunnels was in the final stages of construction and testing at the time of publication.) Republic Services continues to tweak its collection routes to maximize the number of loads that can be hauled directly to the AD/composting plant versus having to be processed at its MRF. “Our recycling coordinators audit the wet and dry containers, and work with customers — especially those with compactors — to improve separation,” notes Cheso.
Of the incoming tonnages, 95 percent is comprised of about 70 percent organic material and 30 percent nonorganic residuals/contamination. The remaining 5 percent of incoming tonnage is 80 to 95 percent organics and 5 to 20 percent nonorganic residuals/contamination. Currently, no yard trimmings are added to the initial mix (e.g., for structural material) beyond what is contained in the organics received from Republic.
The facility is producing about 375 to 425 m3/hour of biogas with a methane content at or above 60 percent. Approximately 20 percent of the electricity generated is used to operate all aspects of the AD/composting plant, except for the rolling stock. Residue is disposed at Republic’s landfill on Newby Island. “ZWEDC does not pay for disposal,” says Hanson. “We are provided vouchers based on the allowable residue as determined by inbound tonnage per Organic Stream.”
Over time, ZWEDC may be able to receive organic wastes from other sources. Under its contract with the City of San Jose, the company must guarantee capacity for and anaerobically digest the first 5,000 tons/month of “Suitable Material” (i.e., suitable for digestion) during the first year of facility operation, for a total of 60,000 tons/year per year. Depending on how that varies from year to year, ZWEDC could take additional organic wastes to reach its 90,000 tons of annual capacity (Phase One). “This was calculated based on the total amount of organic material delivered from San Jose’s commercial sector, less material delivered that was not suitable for digestion (residue and contamination),” explains Hanson.