Project team evaluates positively aerated static pile method with a finished compost cap. Aeration was supplied by blowers powered by a photovoltaic system. Part I
Robert Horowitz and Dan Noble
BioCycle August 2013, Vol. 54, No. 8, p. 26
To survive in a competitive marketplace with low landfill tipping fees, composters must produce a quality product and control costs. To survive in a competitive marketplace in an air pollution nonattainment district, composters need to do all that plus control air emissions, reduce diesel use, and conserve water and energy whenever possible. A research project undertaken last summer (2012) in California’s San Joaquin Valley (SJV) evaluated an approach to achieving these objectives.

A repurposed, electric-powered potato piler (left) served as the conveyor, moving material from the outfeed of the grinder (right) and unloading it over the aeration pipes on the composting pad to build the piles. Photos courtesy of CalRecycle
Funding for the research was provided by the San Joaquin Valley Unified Air Pollution Control District (SJVUAPCD) through its Technology Advancement Program. The air district covers some 25,000 square miles in eight counties in California’s agricultural heartland. Due to its long, dry summers and the very tall mountains that ring it on three sides, the district has some of the worst air quality in the nation. Sources of air pollution include two busy highways loaded with trucks that run its length, more than a million residents, a thriving agricultural industry producing all manner of crop and animal products, and pollution blowing in from the San Francisco Bay Area and even from China. Because the SJVUAPCD has no clear path to attainment of federal Clean Air Act standards, it employs technology advancement to find new ways of doing things that cause less air pollution.
The air district identified composting as one of its largest unregulated sources of VOCs (Volatile Organic Compounds). In the presence of the strong sunlight that blankets the SJV more than 300 days a year, VOCs react with oxides of nitrogen (NOx) — mostly coming from internal combustion engines — to create ground level ozone. Ozone high up in the atmosphere is necessary for life on the planet; it blocks dangerous radiation. But at ground level, it is damaging to human health, animal health and plant life. Based on U.S. EPA standards, the SJV is in “extreme nonattainment” for ground-level ozone, the worst possible rating. That means VOC emissions reductions are required for every major new or existing source. Ozone is listed in the Clean Air Act as a criteria pollutant, and the EPA sets limits for the amount in the air. SJVUAPCD regularly exceeds this limit and is committed to doing everything reasonable and practically achievable to reduce ozone and its precursors.
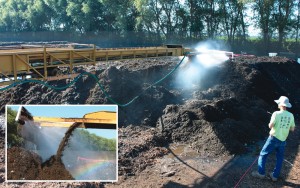
A sprinkler system attached to the outfeed of the conveyor was used to add moisture as the piles were being constructed.
Research Scope, Summary Of Findings
For this project, air emissions reductions were accomplished by using a one-foot thick biofilter layer on top of the aerated state pile. The biofilter layer was comprised of unscreened finished compost and applied using the same conveyor system employed to build the pile. The layer was draped down the pile’s sides to ensure no emissions leaked out. The pile and its biofilter layer were kept wet by a low-tech sprinkler system, rather than diesel-fueled water trucks.
Compared to the windrow control, the eASP reduced VOC emissions by almost 99 percent. Ammonia emissions, a precursor to fine particulate formation, were reduced an average of 68 percent, and greenhouse gases including methane and nitrous oxide (N2O) were reduced by approximately 70 percent (Table 1).
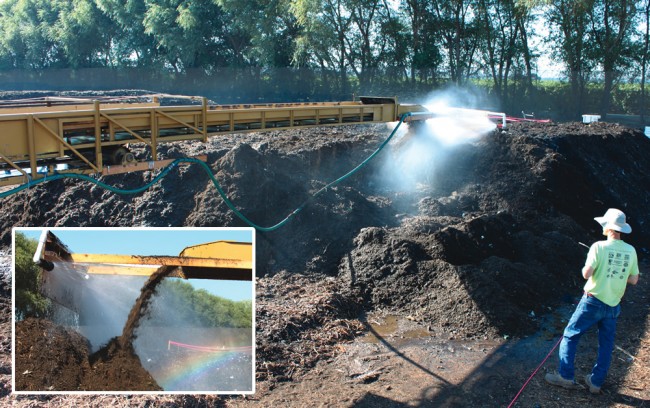
A sprinkler system attached to the outfeed of the conveyor was used to add moisture as the piles were being constructed.
Process Benefits
Because burning diesel is expensive and produces NOx, greatly reducing NOx emissions at the composting site removes a key ingredient for the chemical reaction that produces ground-level ozone. Ozone formation in the SJV is considered to be NOx dependent; there are abundant VOCs from natural and manmade sources in the Valley’s air. Because sunlight is also abundant, reductions in NOx emissions have the biggest impact on ozone formation and air quality in this region.
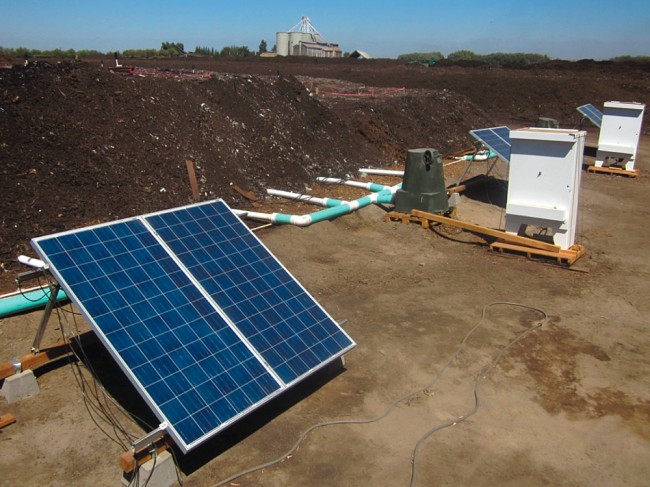
Aeration was supplied by three 1.5 HP blowers, each powered by a photovoltaic system. Excess power generated during the day was stored in batteries so aeration could continue at night.
Composters will likely lose feedstock to low-cost landfilling or direct land application if they charge a high enough tipping fee to pay for commercially engineered aerated static pile systems. Since the SJVAPCD began regulating composting facilities and signaled its intent to require BACT for new facilities, no new composting facilities have been proposed in the Valley. Growth in composting infrastructure in the rest of California has also been anemic over the past few years.
The need for new operations is greatest in Southern California, which already had a dearth of composting facilities and will lose its largest one this fall after a barrage of odor complaints. The closure of California Bio-Mass, permitted to accept 700 tons/day, coincides almost exactly with closure of the giant Los Angeles landfill at Puente Hills, which has been accepting about 1,000 tons/day of green waste as alternative daily cover for the landfill face. Air quality issues in the Los Angeles region, coupled with that area’s population density, make siting composting facilities in urban Southern California extremely difficult.
All of this comes at a time when California is making mighty efforts, spurred by AB 341 (a law passed in 2011), setting the goal of a 75 percent waste diversion rate by the year 2020. CalRecycle, the state agency coordinating the effort to reach 75 percent, estimates California will need to roughly double its organics processing capacity to reach the goal. This will include a combination of composting and anaerobic digestion facilities. The research reported in this article charts a potential path to small footprint facilities, perhaps coupling anaerobic digestion with the eASP. Such a facility could potentially handle food waste and still control odors and emissions adequately enough to be located closer to the urban feedstock source, thereby reducing costly long distance hauling of bulky feedstocks.
Robert Horowitz, a Supervising Integrated Waste Management Specialist with CalRecycle, heads up the Organics Management and Construction & Demolition Unit. Dan Noble is Executive Director of the Association of Compost Producers. In part two of this article, the authors will look more closely at the methods used to construct and maintain the eASP, as well as provide more details on the results of the project.