At the City of Phoenix’s aerated composting facility, air is preconditioned with moisture to mitigate overdrying of the piles, also providing a cooler air stream to the biofilter.
Craig Coker
BioCycle March/April 2019
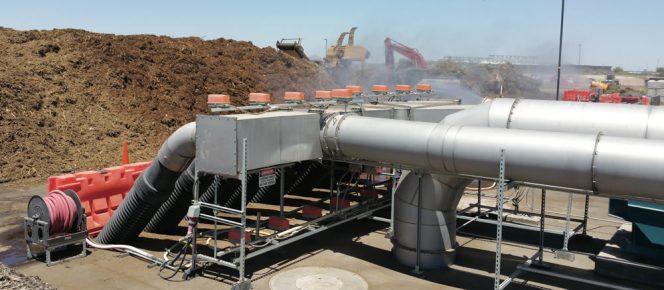
The Phoenix composting facility uses a reversible aeration system with air delivered to, or extracted from, 175-feet long by 180-feet wide extended piles divided into 8 aeration zones.
The City of Phoenix, Arizona’s turned aerated pile (TAP) composting facility went into production mode in June 2017. It was designed by Green Mountain Technologies (GMT) to handle up to 55,000 tons/year (tpy) of mixed yard trimmings and food waste feedstocks. The facility is operated by WeCare Denali LLC. From July 2017 through June 2018, it was processing about 3,100 tons/month of incoming feedstock, of which 97 percent was yard trimmings and 3 percent was food waste. The inbound volumes of feedstocks have been increasing steadily each month since January 2018.
The Phoenix composting system has to manage moisture due to its arid desert environment and dry feedstocks. “The inbound material is usually around 30 percent moisture,” notes Stacy Hettmansperger, Operations Manager for the City’s Public Works Department. “We have strict dust control requirements, so are always thinking about maximizing our composting moisture content.” The piles can be watered while turning them and the facility also has high-powered irrigation guns to keep piles damp.
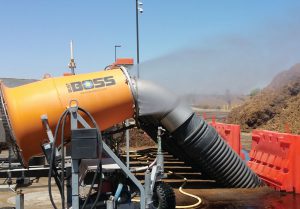
With strict dust control requirements, maximizing composting moisture content and using dust suppression equipment are key to operations in the desert environment.
Composting Configuration
The basic configuration of the Phoenix system was reported previously in BioCycle (see “Phoenix Composting Facility Rises from the Desert Floor,”). It is a reversible aeration system with air delivered to (or extracted from) 175-feet long by 180-feet wide extended piles divided into 8 aeration zones. The concrete aeration floor has nozzles approximately every 5 feet on center, fed by a long network of underground plastic HDPE pipes. The system is designed to turn every pile every 2 to 4 days using a Vermeer CT1010 elevated face turner, moving material 22 feet in each turning event. Phase 1 composting is planned for 27 days, followed by 18 days in Phase 2 and 10 days in curing for a 45-day total production cycle.
The aeration system can be run in all positive, all negative, or in an automatic reversing positive-negative loop, using the differences in high and low temperatures in an individual aeration zone. If the temperature at the bottom of a pile is high, more air is provided in the positive direction; if it is cooler, then the aeration zone reverses to pull air downward to cool the top and rewarm the bottom. Odor management is provided by a 6-inch thick biocover made from screened overs that is placed on piles in the first two zones only, and an 11,750 square foot stand-alone, surface-irrigated biofilter for negative air exhaust.
Cooling The Air
The challenge for this facility was how to cool the hot air coming from the piles at 130°F to the needed operational temperatures for the biofilter at 104°F or cooler. The aeration system has an unusual feature: the positive (forced) air stream is conditioned by misting water before entering the underground pipe network and going into the pile. “We basically installed a ‘swamp cooler’ on the pressure blower,” explains Jeff Gage, Senior System Designer for GMT. The 33,000 cubic feet per minute (cfm) pressure blower is equipped with a misting ring using nonpotable well water to saturate the feed air with cool water at a rate of 7.5 to 8 gallons per minute, which drops the air temperature going to the piles 18°F or more (up to a 30°F drop at times) in hot and dry desert conditions. When the blowers are reversed from positive to negative, the heated compost exhaust air enters the same piping (now cooled) which condenses the moisture out, dropping the temperature.
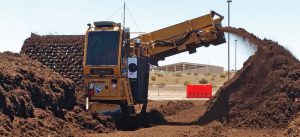
All piles are turned every 2 to 4 days using a Vermeer elevated face turner (above), moving material 22 feet in each turning event.
A “swamp cooler” works on the principle of evaporative cooling. (Moisten your finger and hold it up to feel the wind’s direction. That cooler feeling on the windward side is evaporative cooling). In dry, hot climates like Phoenix, evaporative cooling has been used as a means of cooling, however, it does increase moisture content of the air.
“We designed the system to counter the desiccating effect of summer desert air, which usually has less than 50 percent relative humidity and is 100°F or higher,” notes Michael Bryan-Brown, GMT President. “We thought we might lose as much as 5 percent of the moisture in a pile each day. We decided preconditioning the air with moisture would avoid over drying of the piles, would provide the biofilter a cooler air stream for better removal efficiencies, and would cool the underground piping, which makes it a heat sink and helps to condense the exhaust air when the system is operating in negative mode.”
There is also a separate damper-controlled air duct downstream of the misting ring that can redirect cooled air to the pressure side of the biofilter ductwork. The biofilter is designed for an operating temperature of 104°F, so the misters turn on automatically if the ambient temperatures are above 100°F. If the air flowing into the biofilter from the piles exceeds 104°F, the bypass damper opens to introduce misted air to precool the hot air entering the biofilter. Facility start-up during the hottest Phoenix summer conditions proved that the misting and cooling of the underground pipes was adequate and the redirected cooling air was not needed. This led to decreasing the area of the biofilter needed to treat an increased airflow.
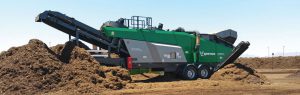
Finished compost is screened using a trommel, and then run through the Komptech Hurriflex (above) to remove film plastic and stones.
The negative aeration manifold drains to a 4,000-gallon concrete vault, which then overflows into a 50,000-gallon fiberglass tank for condensate reuse. The vault and tank include a coarse bubble diffuser to aerate the condensate to reduce the Biological Oxygen Demand (BOD) and potential odors. Fines vacuumed into the system by the negative aeration accumulate at the bottom of the vault, which the contractor can clean out with a vacuum truck. Water from the storage tank and the storm water pond is used by the CT1010 turner to water the piles while turning.
“Air preconditioning on the pressure side works here because of the size of the aeration system,” adds Bryan-Brown. “Smaller aerated static pile facilities usually have individual blowers on each pile, and it would be challenging to develop plumbing and control systems to precondition the air from each blower at that type of site.”
Craig Coker is a Senior Editor at BioCycle and CEO of Coker Composting & Consulting near Roanoke, VA. He can be reached at ccoker@jgpress.com.