Ability to meet stringent air quality emissions rules, “plug and play” interconnection and ease of maintenance are among features attractive to digester operators at WWTPs.
Diane Greer
BioCycle August 2012, Vol. 53, No. 8, p. 54
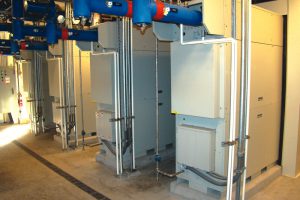
The Janesville, Wisconsin WWTP replaced two 200 kW engines with four 65 kW microturbines. The facility produces about 105,000-scfm of biogas. (Photo courtesy of Unison Solutions)
The enclosed, compact microturbine assemblies come with built in interconnections, switch gear and relay protection. “The power electronics already built into the units has predominantly been preapproved by the utilities so it is really plug and play,” explains Dave Broihahn, vice president of Unison Solutions in Dubuque, Iowa. “This makes the installation, approval process and the interconnection process much simpler.”
Microturbines manufactured by Capstone Turbine Corporation in Chatsworth, California and FlexEnergy in Irvine, California meet the strict emission requirements of the California Air Resources Board. Some of California’s more stringent rules are spreading to other states, such as Massachusetts, Connecticut and New York, which are clamping down on emissions. “WWTP operators are looking to put something in that will be compliant for the next 10 to 25 years,” says Andy Freeman, western region sales manager for FlexEnergy, which purchased Ingersol Rand’s microturbine line in 2010. “That is pushing people toward clean burning technologies.”
Janesville, Wisconsin
In November 2010, the City of Janesville WWTP replaced its two circa 1998 biogas-fueled 200-kW reciprocating engines with four 65-kW Capstone microturbines and subsequently added a 200-kW Capstone microturbine in January 2012. The facility, which treats 12.5-million gallons/day (mgd) on average, produces about 105,000-scfm of biogas. Prior to the Waukesha engines, the facility employed Caterpillar generators. “We had been through the whole system of engine generators and were looking for something more efficient that required less maintenance than an engine,” explains Joe Zakovec, Janesville’s wastewater superintendent.
On a good day the gas engines, capable of producing 200-kW, never produced more that 170- to 175-kW of power, he adds. “With the microturbines if it is cool outside they are going to run at [their rated power production of] 65-kW or 200-kW.” The only time the microturbines produce below their rated capacity is when it is hot. (The electrical output of microturbines is based on the density of air. Electrical output drops during hot, humid weather.)
“Time wise there is a lot less maintenance cost with the microturbines than with the engines,” Zakovec says. The engines needed oil changes every 700 hours, requiring 65-gallons of oil and $200 worth of filters. “We had to change the spark plugs quite often and the air cleaner. All the microturbine has is an air cleaner and the maintenance on the gas conditioning skid.”
Gas conditioning is essential for the efficient operation of microturbines. Janesville employs an iron sponge, previously used with the engines, to remove hydrogen sulfide (H2S). A gas conditioning skid supplied by Unison has a glycol chilling unit to remove moisture, a compressor to increase gas pressure to 100-psi, a reheating unit to warm the gas and vessels containing carbon media to remove siloxanes. “The carbon media needs to be changed out once a quarter at a cost of about $3,500,” Zakovec explains. “Once a year the oil in the compressor is changed and filters on the skid are replaced.” After about 40,000 hours of operation (roughly 5 years) the engines on the microturbines need to be replaced. “In that timeframe with [a reciprocating] engine you will have at least one minor rebuild,” he adds.
Operation of the microturbines is controlled by a computer program to maximize power production during peak hours (8:00 am to 10:00 pm) when Janesville receives 12 cents/kWh for electricity sold to Alliant Energy. Off-peak electricity is sold for 7.5 cents/kWh. Programmatic controls automatically adjust power output across the microturbines, ramping units up or down and turning units on or off based on biogas production.
During off-peak hours biogas is first routed to a BioCNG unit, designed by Unison, to produce compressed natural gas for vehicle fuel (see “Energy Efficiency and Biogas Generation at Wastewater Plants,” July 2012). Excess gas not required to produce the fuel is sent to the microturbines. Heat captured from the exhaust of the microturbines warms water to heat the digesters. Currently heat is only captured off the 65-kW units. Zakovec hopes to start capturing heat from the 200-kW unit in the future.
Sheboygan, Wisconsin
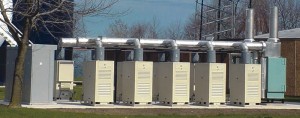
The Sheboygan, Wisconsin treatment facility was an early adopter of biogas-fired microturbine technology, installing ten 30 kW Capstone microturbines in 2006 that produce about 4,500 kW/day. (Photo courtesy of Sheboygan WWTP)
The microturbines installed at SWWTP were older generation systems purchased several years earlier by Alliant for use in natural gas-fired power projects. Some of the microturbines had different engine configurations and different computer programs, explains Dale Doerr, SWWTP plant superintendent. “They were really different so there were some maintenance issues early on.” Since working out the problems the engines have run well. In March 2012, Sheyboygan exercised an option in the Alliant agreement to purchase the engines for a little less than $100,000.
Based on the success of the first microturbines and the availability of additional digester gas generated by codigesting high strength food waste, SWWTP purchased two 200-kW Capstone microturbines in December 2010. From an operational standpoint, Doerr likes the flexibility of being able to maximize energy production with the microturbines given the available biogas. “The 200-kW units have a 50 percent turndown so if you do not have enough biogas to run at 100 percent and only have enough to run 150-kW it will run,” he explains. Low emissions are another plus. “They are clean burning and meet the California emission standards.” Sheboygan is in an air quality nonattainment zone for ozone.
Similar to Janesville, one downside to the microturbines is less electricity production when the weather is hot and humid. During a recent spell, the engines were generating at 76 percent of their rated capacity. The hot, humid weather only affects output three to four months a year in Wisconsin. While this is not a big concern for Sheboygan, it is a consideration for WWTPs located in regions with longer periods of sultry weather.
York, Pennsylvania
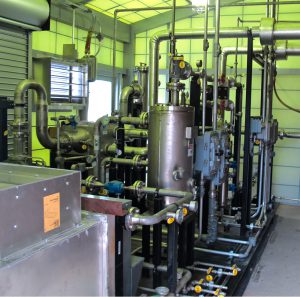
The gas conditioning skid at the York, Pennsylvania WWTP removes moisture, hydrogen sulfide and siloxanes from the biogas. (Photo courtesy of E-finity Corp)
Realizing it needed more efficient technology, the York City Sewer Authority investigated alternatives. Refurbishing the reciprocating engines was not cost-effective and did not take advantage of new technology on the market, Douglas explains. An evaluation found there was not much difference between the capital cost of microturbines and reciprocating engines while maintenance costs for the microturbines are estimated at or below the costs for the engines. Helping the economic case for the microturbines were incentives offered by the state of Pennsylvania. Funding for the $4.5 million system was provided in part by a $1.5-million low interest loan through state’s Alternative and Clean Energy program and a $500,000 Pennsylvania Green Energy Works grant.
Beyond the economics, Douglas was sold on the lower emissions of the microturbines. The microturbines produce less that 1,000-lbs/year of emissions compared to reciprocating engines that produced between 60 to 80 tons/year of nitrogen oxide (NOx), carbon monoxide (CO) and sulfur oxide (SOx). “What is really neat about microturbines is I do not need an air permit,” he says. “We do not need to report their emissions to our state.”
The installation, completed in October 2011, includes three 200-kW Capstone biogas-fired microturbines and a Unison gas scrubbing system that removes moisture, H2S and siloxanes from the biogas. Heat captured from the engine exhaust is used to heat the digesters and, during the winter, the plant’s buildings. Included in the installation is a backup power system composed of five 200-kW Capstone natural gas-fired microturbines. The facility participates in a number of demand response programs and generates revenue with the units by producing power during peak demand.
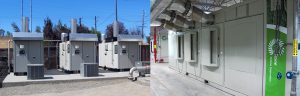
Microturbines manufactured by Flex Energy (left), which purchased Ingersol Rand’s 250 kW microturbine business, and Capstone (right) meet stringent air quality emissions requirements. (Photos courtesy of Flex Energy and E-finity Corp)
Diane Greer is a Contributing Editor to BioCycle.