Top: HDPE pipe from Windham Solid Waste Management District’s new aeration system (left). Recently built pile capped with 6-inch layer of screened compost to cover compostable bags and cardboard (right).
The Windham Solid Waste Management District (WSWMD), located in Brattleboro, Vermont, has been composting food scraps, leaves and other residuals for many years in turned windrows. The facility receives source separated curbside organics from around 2,000 residences in Brattleboro, and commercial and institutional food waste from restaurants, food manufacturers, colleges, and grocery stores. WSWMD also has a food waste drop-off site at its transfer station for households without curbside service. “In 2024, we received about 2,500 tons of food waste, with about 600 tons from the curbside program, 600 to 700 tons from the commercial/institutional generators, and 50 to 60 tons from the drop-off station,” notes Robert Spencer, WSWMD’s Executive Director.
The composting site is on a 3-acre parcel, and had been permitted by the Vermont Agency of Natural Resources (ANR) to receive 2,000 cubic yards (cy)/year of food waste, and 5,000 cy/year of all other organics. “The amount of food waste we were receiving was slowly increasing, and WSWMD wanted to upgrade the composting facility to handle more material on the same footprint,” adds Spencer. “To make that happen, we knew we had to switch to an aerated static pile (ASP) system for the active composting phase, versus our existing turned windrows. To facilitate operating during the cold weather months, the District also wanted to install a heat recovery system as part of the transition to ASP.” Agrilab Technologies Inc. (AGT), a Vermont-based company that fabricates and installs compost aeration and heat recovery systems, was selected for the project. AGT has several installations in Vermont, six other states and Canada on farms and commercial sites. WSWMD installed the AGT Compost Hot Box 250-4R unit, which includes an aeration blower, temperature, flow, pressure and oxygen sensors, remote internet access, and programmable controls for four reversing aeration ports. It is housed in an insulated 20-foot shipping container.
WSWMD applied for and received an ANR permit to accept 5,000 cy/year of food waste and 40,000 cy of all other organics. A permit amendment enables the facility to take soiled paper and cardboard. In addition, the District had to get a new storm water permit and regrade the entire site. The new storm water management system includes a vegetated treatment area (VTA) downslope of the active composting pad. “All water from the pad, curing and screening areas flows to the VTA and then to the transfer station storm water system, and ultimately to the Connecticut River. Per state regulations, storm water from areas upgradient of the compost pad is diverted around the compost pad to keep it from coming in contact with the compost area,” explains Spencer. “It then flows to a new storm water retention basin. We will need to test the storm water following the VTA to see if the buffer is removing what we need to remove. So far, it is working very well.”
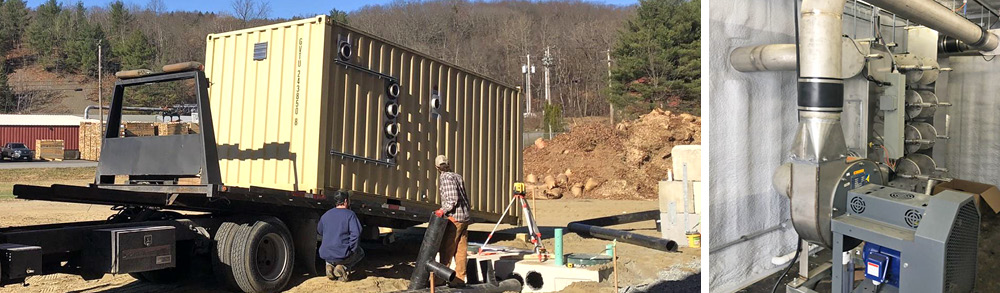
Arrival of Agrilab Technologies‘ Compost Hot Box 250-4R (left). Inside the Hot Box, blower, ductwork and valves for the aeration system (right).
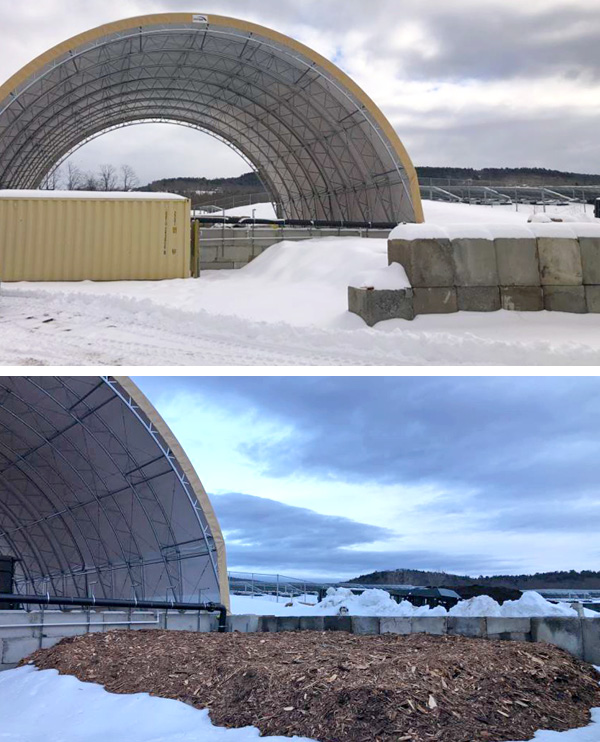
Snow that covered the biofilter at startup (top) melted, revealing bark sourced from local sawmill (bottom).
A new tipping area that includes a bunker with a gravel pad was constructed to receive food waste and mix in amendments. Active compost is added in a 1:3 ratio when mixing a batch to help inoculate the mix. Each batch is roughly 200 cy; a new batch is loaded weekly. A 6-inch capping layer of screened compost is placed on top of the piles to cover compostable bags and cardboard on the surface. The ASP system is in an open-ended 5,000 sq. ft. fabric building with a gravel pad. There are four zones, with pipe-on-grade HDPE aeration pipes that are coupled to the pipe stubs on the AGT Compost Hot Box. The pipes are covered with a layer of fibrous hardwood bark — roughly 1-to-2 inches wide and 3-to-12 inches long — from a nearby sawmill that debarks logs before milling them. The bark also was used to build the biofilter. Retention time in the active composting phase is roughly four weeks, after which the compost is moved to the curing area where it is placed in windrows and turned as needed.
“Oxygen concentration and temperature in the exhaust is measured, and the levels influence the on/off times for positive and negative aeration,” says Spencer. “Currently we are taking up to 10 minutes for positive aeration to increase the oxygen, and 25 minutes of negative aeration. At key stages the air pulled through the piles is recirculated into a new pile to jump start or maintain optimum temperatures. The temperature was below 0°F when the system started up in February, and the heat recovery has accelerated the composting process significantly.”
Capital costs for the new facility were about $800,000. The original design included putting the aeration pipes in concrete trenches, but the cost exceeded the available budget. Funding for the upgrade was provided by the WSWMD, USDA Rural Development, and the Vermont ANR. Heat recovery for finished product drying prior to screening, recessed channels in the working floor, additional sensors and a feedstock mixer are targeted for Phase 2 improvements.