An open-source, international field testing program is designed to determine real-world field disintegration of certified compostable packaging across Canada and the U.S.
Emily McGill and Cary Oshins
BioCycle January 2018
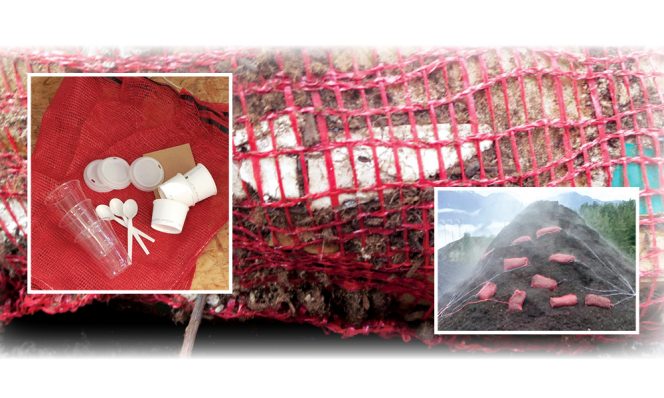
The same sample kit of certified compostable products (example in left inset) is provided to all compost manufacturers for field testing. Mesh bags with the products can be buried in a windrow or static pile (right inset) as it is being built. Contents of mesh bag mid-way through the composting process (background).
The commercial compost manufacturing industry is divided on acceptance of certified compostable food packaging. Some take it, some don’t — not without good reason. Certified compostable products don’t always disintegrate as hoped in commercial facilities, or at least may appear not to, which can be difficult to determine if they are mixed with conventional plastic contaminants.
The only way compost manufacturers can know for sure how the packaging performs in their facilities is if they test the products themselves. The International Field Testing Program, produced by the Compost Council Research & Education Foundation (CCREF) and BSIbio Packaging Solutions/BÉSICS® (BSIbio), with a steering committee involving members of the Biodegradable Products Institute (BPI), ASTM, and other experts in the compost manufacturing and compostables industry, provides that capability. Compost manufacturers receive the tools and methods to test certified compostable products on site. Their results are then anonymously posted in the testing program’s database for others to learn from. In short, they have the ability to answer their own questions about how specific materials may work in their operations, and at the same time contribute to a larger, broader understanding throughout the industry.
The International Field Testing Program (IFTP) is in Beta testing phase from 2017 through spring 2018. The testing method uses mesh sample bags and is suitable for aerobic composting facilities. The method can be adapted to a range of operating conditions, and has already been tested in facilities ranging from 38,580 to 220,500 tons/year.
Each facility’s operations may require slight modifications to the test method, which the IFTP will track and share with similar facilities. The more facilities that participate in the Beta stage of the program, the more widely the test methods can be evaluated and assessed. The IFTP is welcoming beta testers to refine the program and help adapt it to even more facility types.
It Starts With Certified Compostable
Testing with certified compostable products is essential, because the program focuses on disintegration, which is just one component of compostability. Certification means an independent third party has tested a product and it has biodegraded in a set time period, under commercial operating conditions simulated at a lab scale, and at a rate similar to natural materials.
Beyond disintegration, the ingredients in the products must also be biodegradable (i.e. microorganisms are actually digesting and processing the carbon in the products), should not contribute heavy metals, and should not impact the ability of the compost to support plant growth — all of which are verified in the lab, along with controlled disintegration, during the certification process. North American agencies certifying compostable products are the Bureau de Normalisation du Quebec (BNQ) in Canada, and the Biodegradable Products Institute (BPI) in the USA.
Field testing builds on this laboratory assurance to check whether products will still disintegrate within the time frame and operating conditions at a select facility, and if not, evaluate what may be causing a product to not successfully break down. This is ultimately what matters, to the customer, to the packaging industry, and especially to the compost manufacturer.
The same basic sample kit of products is provided to all compost manufacturing facilities undergoing testing. Using the same complimentary set of certified compostable products that are common on the market today helps to control the variability inherent in different certified products. This enables a baseline of test results to be established across facility types, and under different operating and environmental conditions.
Why Test?
Multiple groups across the compost manufacturing and certified compostable packaging industries are working on bringing field testing to the forefront. It’s a natural co-evolution for two industries that have experienced significant growth in the past two decades, and a necessary step to make sure that certified products continue to work in today’s compost manufacturing facilities, and to understand where the gaps may be.
“Rarely do we have a chance to use a robust scientific method across many facilities to fundamentally examine decisions,” notes Greg Dudish, a research scientist helping to coordinate field testing in the San Francisco Bay Area. ”This project is an opportunity to help our industry pause, examine, and make informed decisions regarding compostable plastics. The results aren’t theoretical — we don’t simulate composting conditions. These are composting conditions! We aren’t simulating products, we are using compostable products currently in use. Combined data from these tests at a variety of composting facilities gives our industry a map of the landscape at the intersection of Compost, [Compostable] Plastics, and Product Design, and creates shared knowledge between all the stakeholders, which can be used to navigate the next decisions.”
How To Test
The following steps are involved in conducting field testing at a compost manufacturing facility:
1. Express interest at the Field Testing Database webpage. (http://compostfoundation.org/fieldtesting).
2. Program team reaches out, and emails the test method and registration forms.
3. After filling out basic facility information, Program team mails a sample kit with basic materials required for testing.
4. Create a testing plan.
5. Test!
6. Upload the results.
7. Done! You can start another test if desired.
What To Expect
The IFTP equips facility operators and/or other research partners with the tools and methods to test common certified compostable products at their site. Any questions researchers and compost manufacturing facility operators have during testing can be directed to the program team. In the Beta phase, most of the data gathering is done by hand, and results can be scanned or mailed back to the IFTP.
As the Beta phase wraps up in mid-2018, the online database will be fully operational. At that point, composting facilities can directly upload photos, notes, and data from their testing while maintaining anonymity. The results database will be made open-source and available for widespread analysis once the quantity of data is sufficient to maintain anonymity of the results. “We need this type of information to create more robust resources throughout the composting value chain,” says Rhodes Yepsen, Executive Director of BPI and co-Chair of USCC’s Compostable Products Task Force (CPTF). “These data points will be used in CPTF decision guides for composters, and eventually will help inform a Standard Operating Practice, so that facilities being designed/operated to handle postconsumer organics can consistently break down incoming certified products.”
Ginny Black, Chair of the CCREF Board of Trustees, adds: “The CCREF is excited to be participating in this forward-thinking program. Providing a platform for collaborative research is exactly why the Foundation exists. No compost manufacturer operates under ideal conditions, as much as they’d like to. Yet the lab test for certification is done under ideal conditions. Our expectation is that by enlisting compost manufacturers in doing this field testing, we can better understand how far from ideal you can get and still achieve adequate disintegration of compostable products.”
Analyzing the testing results in the database will help identify correlations between operating conditions and disintegration rates. Collaborating across industries, the packaging and composting sectors will together be able to answer the question: “How do certified compostable products disintegrate in day-to-day composting facility operations?”
Getting engaged in the testing program isn’t just for composting facility operators. Students, interested parties and researchers within the industry or related fields are successfully filling the role of coordinating testing at their local facilities.
To learn more about the genesis of the program and test methods, read “Field Testing Protocol for Compostable Packaging”, September 2017 BioCycle.
Emily McGill is Manager of Research and Communications at BSIbio (compost@bsibio.com). Cary Oshins is Director of Education at the Compost Council Research and Education Foundation. Contact Emily for more information on testing, or express your interest in testing at compostfoundation.org/fieldtesting.