University utilizing a “characterize-implement-evaluate-adjust” approach to its Zero Waste pilot projects to optimize program performance and diversion. Part II
S. Leblanc, J. Kwasny, K. Yan and D. McCartney
BioCycle August 2016
The University of Alberta (UAlberta) is home to 39,000 students and 15,000 staff and faculty. UAlberta has four campuses in Edmonton and one in the nearby city of Camrose. As noted in Part I, the university has set a target to capture 75 percent of organics from its waste stream to contribute just over 1,600 tons of source separated organic feedstock to the City of Edmonton’s new anaerobic digestion facility that is in construction. It also outlined a goal to reach 90 percent waste diversion by 2020.
The Zero Waste initiative’s timeline and activities are summarized in Figure 1. The first three phases of program development — cost analysis, building characterization and conceptual design — occurred in early 2014 and were followed by implementation and evaluation in three pilot buildings. Two of these buildings were investigated more thoroughly and key results will be highlighted here.
The Students’ Union Building (SUB) is accessible 24 hours a day as a study space, about 12 hours a day as a cafeteria with multiple food outlets, and it houses services like the bookstore, health centre, pharmacy and student services offices. The Housing Union Building (HUB) is a four-block-long residence and mall with both retail and food vendors. SUB had some organics capture already occurring, while HUB had no existing organics collection prior to the Zero Waste program rollout.
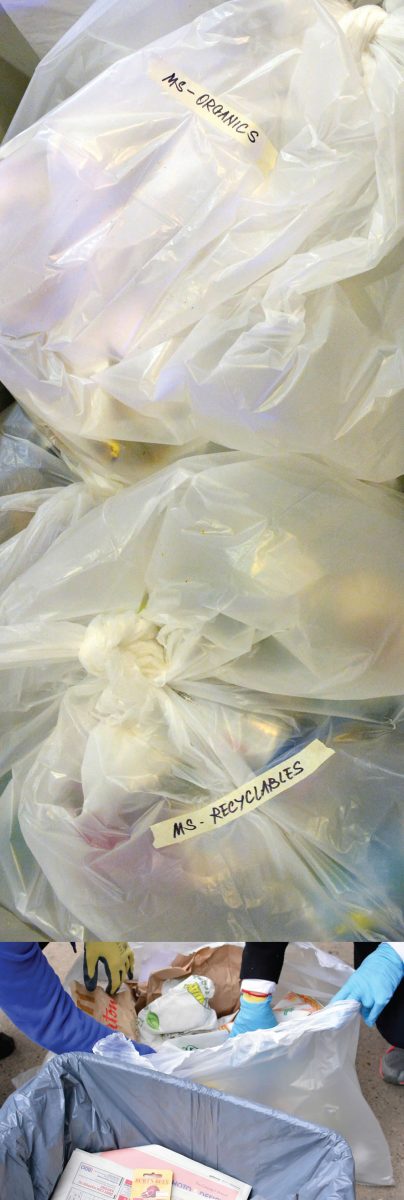
The mini audit sampled bin contents at select Zero Waste stations. Collected bags (top) and actual sorting (bottom) are shown. Photos courtesy of the University of Alberta Office of Sustainability
Evaluation Methods
Evaluation of SUB and HUB consisted of four primary methods: Actual weights from the hauler, mini waste audits, visual monitoring of people using the new stations, and visual inspections of food vendor waste containers. Hauler weights were tracked annually so that year-to-year comparisons could be made. The other activities were conducted in fall 2014 in SUB, and fall 2015 in both SUB and HUB. A third round of evaluation is planned for fall 2016 as follow-up.
Mini Waste Audits: Sustainable operations and building maintenance staff worked together to conduct mini waste audits. They selected a sample of Zero Waste stations, set aside the material generated from about half of a day, and then sorted and weighed it. These audits used simplified categories of “correct” or “impurity” to make them manageable and easy to repeat over a three month evaluation period with limited staff capacity.
Visual Monitoring: Sustainable operations staff and student volunteers also performed visual monitoring during busy periods such as over the lunch hour. They would station themselves in an inconspicuous location, observe and record how people used the Zero Waste stations, what they threw away and which container they used. This allowed the university to both verify what was seen in the mini audits and further identify key problem items that were often placed into the wrong container.
Food Vendor Waste Inspections: In HUB, this was the first time that food vendor organics collection was implemented so additional inspections were conducted. Sustainable operations or building staff would simply look inside the rolling carts that food vendors deposited their materials into, take pictures, and send quick tip sheets back to food vendors celebrating what was done correctly and giving tips for common problem items.
Results Highlights
The Edmonton Waste Management Centre of Excellence (EWMCE) completed all of the data analysis and provided the university with a summary report including some key recommendations for improvement. For example, it appeared that in HUB, a revised station design with a slot for Mixed Paper resulted in much higher purity (95% in HUB vs. 65% in SUB) in that container. The university is going to replace the openings in SUB and conduct further evaluation in the fall 2016 semester.
The two most encouraging findings come from the hauler weights and mini waste audits. According to the last three years of hauler data, landfill weights appear to be slowly decreasing, while organics volumes are increasing in both SUB and HUB (Figure 2). In fact in HUB, landfill material compactor pick-ups have been reduced from twice a week to once a week due to decreased volume. This was an expected result but to see it born out in the hauler data is very exciting.
Source separated organics collection has nearly tripled in SUB with expansion and improvement of the new Zero Waste program. HUB did not have any organics collection prior to 2015.
The mini waste audits have shown that the new Zero Waste stations are fairly successful because impurity levels are quite low in all but the SUB Mixed Paper container (Figure 3). The biggest challenge remains to increase capture because the landfill stream still consists of 20 to 30 percent recyclable or organic material.
Core System Changes For Organics Collection
In addition to building-specific implementation measures, some systemwide changes were also made to streamline the university’s organics collection system.
In January 2016, a 24-cubic yard organics compactor, complete with a tank heater and heat tracing, was installed at the on-campus Recycle Transfer Station (RTS), allowing for an improved organics collection system. Instead of having the contracted waste hauler tip individual rolling carts at each building, university staff now complete this pick-up and consolidate the material at the RTS. Internal recycling staff were already collecting recyclables in rolling carts from building loading docks so it was an easy transition to add the organics rolling carts to their existing schedules. This change has reduced both collection costs and the number of trucks on campus, and in turn reduced the overall environmental footprint.
To support this operational change, an indoor automatic rolling cart wash system was purchased and installed at the RTS in March 2016 to ensure clean rolling carts were always provided at the loading docks to reduce odors and pests. A full time staff member was hired to remove visible contamination in rolling carts, tip the full rolling carts into the appropriate compactors, operate and conduct basic daily maintenance on the cart wash system and keep the RTS looking its best.
Building A Culture Of Zero Waste
With all of the operational changes underway, it is easy to overlook the human side of Zero Waste. To include that aspect, UAlberta’s Office of Sustainability created the Green Spaces Certification. This program gives offices and dorms a chance to rate themselves on a sustainability checklist and then receive recognition as “Green & Gold,” “Silver” or “Bronze.”
As part of the Zero Waste initiative, Facilities and Operations worked with the Office of Sustainability to adapt the program for food vendors (e.g., eliminate Styrofoam, use bulk condiments to reduce waste). Over 95 percent of food vendors have participated to date and have received a Bronze rating. Each year they have a chance to make a few small changes and improve their rating. This is one way the university hopes to instill a culture change and Zero Waste mentality on campus.
Next Steps
With two buildings under its belt, UAlberta will be endeavoring in the 2016/17 year to implement the Zero Waste system in other buildings, starting with those that are high generators of organic waste. The university is committed to continuous improvement and will use a similar characterize-implement-evaluate-adjust approach to reach its Zero Waste aspirations.
Shannon Leblanc is Sustainability Coordinator and Jessie Kwasny is Waste Diversion/Recycling Coordinator, both with the University of Alberta. Kentson Yan is a Research Engineer and Daryl McCartney is the Executive Director at the Edmonton Waste Management Centre of Excellence.