Grinding strategies are driven by business priorities, feedstock types and quantities, compost mix ratios, product markets, sales seasonality and the weather.
Craig Coker
BioCycle March/April 2017
Particle size reduction is an important organic materials handling step that enhances the biological or chemical process by optimizing the particle surface area-to-volume ratio. Grinders, shredders and chippers are used for size reduction of wood wastes, yard trimmings, land-clearing debris, and in some cases, food waste. The primary objective of this equipment is to reduce large particles to small particles by physically breaking them apart, although it can be used for mixing, to some extent. Grinding equipment can be classified as chippers, shredders, hammermills, toothed rotor grinders, and screw-type cutting blades.
Grinding strategies are driven by business priorities, feedstock types and quantities, compost mix ratios, product markets and sales seasonality, and by related aspects such as weather. For operations that provide mobile contract grinding services to land clearing projects, the grinding strategy is much more production-oriented than for those facilities that accept brushy material for on-site grinding and usage. Whistler Composting, Calvert Wood Recycling, Living Earth and Royal Oak Farm illustrate how different operations approach size reduction and materials management.
Whistler Composting
Whistler Composting is in the ski resort region of British Columbia in western Canada at about 2,200 feet elevation. The facility is operated for the Municipality of Whistler by Carney Waste Systems, a regional waste hauler and management company. It processes about 7,000 tons/year (tpy) of biosolids and food waste, along with 8,000 tpy of woody wastes, using a Wright Environmental agitated tunnel reactor composting system. Carney Waste Systems does contract grinding at land clearing sites as well as grinds incoming woody material at the composting facility.
A Rawlings HZX electric horizontal grinder is used at the composting facility. The Rawlings line of grinders was developed for use in the timber industry for making hogged fuel. The horizontal grinder has a rotational speed of 565 revolutions per minute and is powered by two 400-hp electric motors mounted in parallel, so rotational torque is quite high. “The dual motor design allows for extra horsepower and torque to be applied from a secondary motor when needed,” explains Chris McMullen, Sales Manager at Rawlings Manufacturing. “Usually these dual motor set ups use the same size motor so operators can basically double the amount of available horsepower and torque without having to constantly run the second motor. Electric motors have the maximum torque they are rated for at 0 rpm, so this allows instantaneous extra power the moment the second motor energizes. Once the machine has cleared the infeed material and the amp load goes back down to the normal operating levels the second motor shuts off. This on-demand power saves electricity by only using the extra motor when needed.”
There was another key savings for Whistler Composting by using the electric grinder. “We went with the electric motor rather than a diesel motor because British Columbia imposes a $50/metric ton carbon tax on greenhouse gas emissions,” notes Patrick Mulholland, General Manager of Whistler Composting. “The Rawlings grinder is loaded from the outside of our composting hall with an excavator equipped with a rake, and the discharge belt inside the hall unloads directly into the wood storage bays. We use an overhead electric crane to move woody material to our mixing system prior to charging the Wright tunnels with fresh feedstocks.” Mulholland adds that Carney Waste Systems often grinds land clearing debris in the field with a CBI 1100-hp tracked horizontal grinder, which is better suited for those types of mobile processing jobs.
Routine production with the Rawlings grinder is about 50 cubic yards/hour using a 3-inch diamond-mesh screen. The cutting heads are mounted onto blocks bolted onto the rotor with a small profile so no cutting heads or teeth stick out far from the rotor. This reduces breakage when the rotor encounters tramp metal. “We have only broken one mount in eight years,” says Mulholland. “The machine will easily grind material up to about 12-inch diameter, and, while it can handle larger sizes, I prefer to use the CBI or one of our other grinders for larger woody fractions.”
Weather plays a role in the company’s grinding strategies, he adds. “We normally get about 30 feet of snow every winter, so I have to plan on having about 5 months worth of ground-up wood on hand before first snow. And, as a ski resort area, our population rises from a summer population of about 10,000 to a winter population of about 50,000, so the quantity of biosolids we have to handle goes up as well. The volume ratios of woody materials has to be adjusted seasonally to keep a 60 percent moisture content in the mix going into the Wright tunnels. All our ground wood piles are covered so we aren’t introducing snow and ice into the mixing and composting equipment.”
Calvert Wood Recycling
Many challenges create bottlenecks in the production of mulch. One of the most frustrating is the poor performance and failure of equipment. Maryland-based Calvert Wood Recycling wanted to eliminate that potential entirely, and recently purchased several new pieces of Doppstadt equipment from Ecoverse. Randy Whitsell, Calvert’s general manager, notes that quality and efficiency drove the decision to invest in a machinery overhaul. “The facility had an old tub grinder and deck screen, and the high costs of maintenance were not acceptable,” he explains. “We also knew that operational costs were far more than they should be and wanted to bring them into alignment with our efficiency goals.”
Calvert Wood Recycling sits on 121 acres in the largely-rural town of La Plata, about 20 miles south of the Washington D.C. metro area. “We have a contract with Charles County to handle all their leaves, grass, compost, topsoil and retention soil, which contributes quite a bit of supply and demand to our facility,” says Whitsell. “We’ve earned contracts with several large commercial landscapers and are pursuing some institutional contracts now too.”
Calvert took possession of the new equipment in late spring 2016. Its Doppstadt equipment includes a DW 3060K slow-speed shredder, an AK 530 high-speed grinder equipped with AR400 face-hardened hammers and an SM 720K trommel screen, equipped with a 2-inch screen mesh. Most of the material is processed directly in the AK grinder, which feeds the SM trommel to remove fines and stockpile a finished product. Whitsell saw an immense improvement immediately. “With our old tub grinder, there was no getting around sending everything through there twice,” he admits. “But the AK easily delivers 50 percent output on the first pass that can be screened and sold as double-ground quality mulch. The remaining 50 percent is sent back through again. In the end we only get about 2 to 3 percent total waste in fines, where before that could be as high as 20 percent.”
The DW 3060K shredder is employed to process heavier material, such as stumps and tree trunks, providing a primary reduction before feeding the AK grinder. Calvert often screens the discharge from the shredder through the SM720 trommel to remove dirt and fines before regrinding with the AK530. “I would like to add another trommel screen so we can run a more efficient operation,” note Whitsell. The higher efficiency equipment has lowered Calvert’s operating costs.
A more subtle benefit that Whitsell recognized is the increase wear time on the AK hammer tips. “The upswing design on the AK hammers gives us a very consistent 1.5-inch minus product, and they have only needed to be changed every three weeks or so. We were lucky to get a week out of our previous hammers in the old tub grinder.”
Much of Calvert’s source material has been traditional green waste and land clearing debris. But working with the Maryland Department of the Environment (MDE), the opportunity to begin a food waste recycling program is being explored. “We’ve recognized that this is a big opportunity,” acknowledges Whitsell. “But it is also a challenge. We know there is money to be made, but are still working through the economics of the whole process.”
Royal Oak Farm
Royal Oak Farm, a large industrial materials composter in south-central Virginia, expanded into wood waste grinding, as it found that sourcing wood chips for the composting facility was difficult due to competition from a wood biomass power plant, two paper mills and three engineered wood products companies.
Royal Oak purchased a Komptech Crambo 5000 slow-speed high-torque shredder in 2009. The machine is equipped with a 446 HP diesel motor and twin cutting shafts that rotate at 36 rpm. This shredder produces over 160,000 foot-pounds of torque and can grind stumps, large tree trunks, railroad ties, white goods, tires, and a wide variety of woody materials. The shredder can process up to 50 tons/hour.
Royal Oak transports the shredder, an excavator, and a trained operator to sites to grind up piles of stumps, logs, pallets, waste wood, tree limbs and/or brush. It provides this service at a very competitive price, provided it can keep all the ground woody material produced by the shredder for use at the composting facility. “This shredder has been a God-send for us,” notes Ken Newman, Managing Member of Royal Oak. “We now have enough grinding work that we keep one person in the field all the time and are rarely dealing with a shortage of carbon amendments for our composting feedstocks.”
Purple Cow Organics, LLC
Purple Cow Organics, based in Middleton, Wisconsin, near Madison, operates four composting and mulch production sites in the region. Started in 2011, it composts yard trimmings, leaves, perennial and annual clippings, brush and clean wood waste, processing about 60,000-plus tons/year in total. Purple Cow Organics produces organic OMRI listed compost and liquid biological products for farmers, gardeners and landscapers, as well as for green infrastructure applications. These products can be purchased in bulk and at the retail level. “We make and market premium products, which requires us to always pay close attention to our processes,” explains Jerod Reuter, Director of Operations. “It is critical to optimize moisture and oxygen levels in our windrows to provide the ideal breeding ground for biology, so grinding to a specific size is very important.”
Three years ago, Purple Cow Organics purchased a Rotochopper B66 horizontal grinder with a range of screen sizes that yield the desired control over particle size. “For our premium compost product, we need different screen sizes for different feedstocks,” notes Reuter. “Not only can particle size change based on the composition of the feedstock but also its moisture content. The screens help us achieve that precision, and the Rotochopper screen installation system gives us the capability to change out the screens quickly and simply.”
Changing the screens with its previous grinder required a separate piece of equipment to lift out the screen and put a different one back in, posing a potential safety hazard. “Now, everything needed to change screens is supplied with the machine,” observes Reuter. “This system locks the screen in place hydraulically without any fasteners. No overhead lifting equipment is required, and when we pull the screen away from the rotor, we gain access to the rotor and teeth for inspection and maintenance. We can change the screens in 15 to 20 minutes, versus several hours or more with our old machine.” The B66 also has integrated shear pin protection so if a large piece of steel or other “ungrindable” object enters the grinding chamber, the pins will shear and the screen falls away, which minimizes damage and Purple Cow’s downtime.
As Director of Operations, Reuter also appreciates the machine’s safety features, especially during grinder chamber maintenance. “The operator sets the machine to Maintenance Mode, which disables the engine and starts an auxiliary electric-powered hydraulic pump to perform the maintenance,” he explains. “In Maintenance Mode, we can unlock the grinding chamber access door. The engine and rotor remain disabled — and while the access door is open, the grinder cannot be returned to operating mode. These features allow us to have control over particle size, maximizing our products’ biology without having to sacrifice on safety or productivity.”
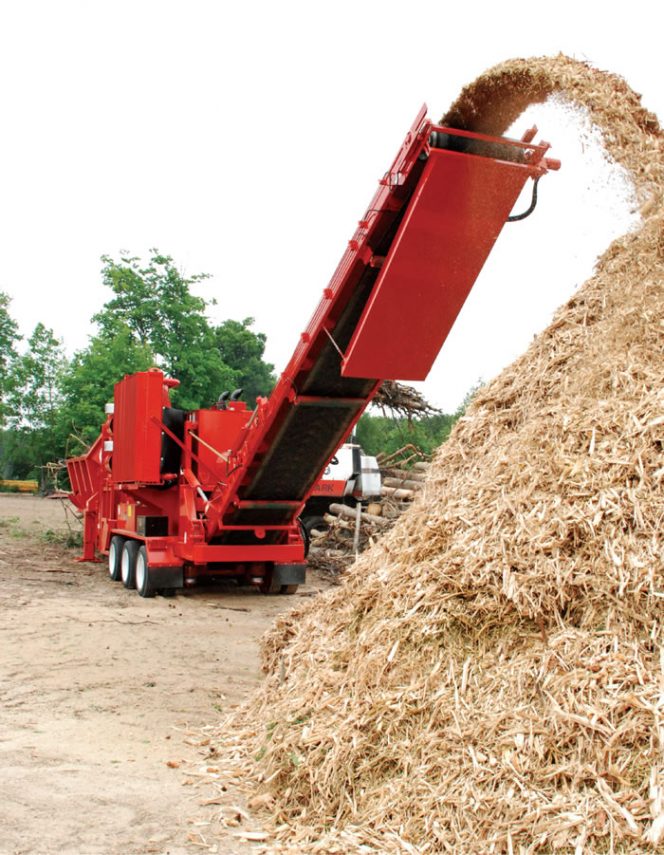
Morbark 6600 horizontal grinder powered by 1,200 hp 12 cylinder CAT engine at Tree Cycle Land Clearing Inc.
Tree Cycle Land Clearing
Tree Cycle Land Clearing, Inc., located in West Palm Beach County, Florida, runs two Morbark 6600 horizontal grinders and a Morbark 4036 chipper. The grinders are powered by 1,200 horsepower 12-cylinder Caterpillar diesel engines. “We are primarily in the land clearing business and in the contract grinding business, so throughput is very important to me,” notes Sean Casey, President of Tree Cycle. “When we are running to max out throughput, I run the grinders with two 6-inch screens in the top and two 8-inch screens in the bottom.” Casey adds that the Morbark grinders handle palm tree wastes with ease. These are often a problem due to the long stringy nature of palm wood fibers. Tree Cycle uses the Morbark 4036 chipper to make wood chips for biomass plants to burn, but Casey says that business is in one of its cyclical downturns.
Tree Cycle provides mulch to resellers on a wholesale basis. “When we’re making good quality products, we swap out the screens and use ones with a 2.5-inch hexagonal mesh,” explains Casey. While many think of Florida as having a continual growing season, he notes that mulch sales are definitely seasonal, with peak season between October and January, a second season between January and July, and a slow season between July and October.
Living Earth
Living Earth, a Texas-based composter, processes over 750,000 tons/year of yard trimmings, brush, preconsumer vegetative food discards, untreated wood wastes, stable bedding and herbivore manure. It composts the yard trimmings, manure and food scraps in large static piles. Brush and tree trimmings are processed separately into mulch. All Living Earth recycling facilities are open to the public and commercial businesses such as landscapers. In addition, the company has contracts with several municipalities to process curbside-collected brush and yard trimmings.
Living Earth’s municipal accounts include servicing the City of Houston’s every-other-month brush collection program. “Living Earth partnered with the City to process the tree debris collected by sanitation crews,” explains Lora Hinchcliff, Living Earth’s Municipal Solutions Manager. “With this guaranteed influx of new material, we opened another recycling facility to accommodate city trucks, reducing haul time, and providing the City with four recycling drop-off sites in each of its service quadrants.”
Rose has found that there is an adequate amount of woody material in the yard trimmings to keep the static piles porous enough during composting. “All of the brush is made directly into mulch as we don’t want that woodier material that looks ‘sticky or stemmy’ in our compost product,” he explains. “Residents can include small twigs with their yard trimmings, which is enough to give the composting piles porosity.”
Craig Coker is a Senior Editor at BioCycle and CEO of Coker Composting and Consulting (Roanoke, VA). He can be reached at ccoker@jgpress.com.