Rich Flammer
BioCycle October 2015
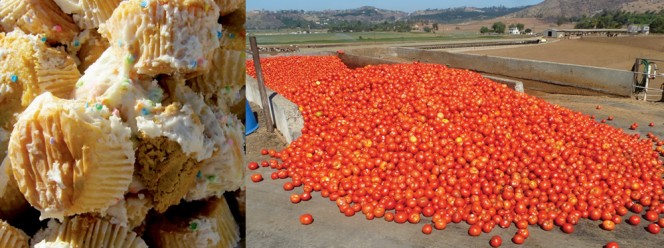
Suppliers of food scraps fed to the dairy herd include bakeries, bread factories, produce packaging facilities and breweries (cupcakes and tomatoes shown).
This is a triple win,” exclaims Frank Konyn Jr., co-owner with his wife Stacy of the Frank Konyn Dairy in San Diego, California, regarding the food scrap to feed program he has put together. “My herd and business benefit, the community benefits, and we’re diverting impressive amounts of food from the landfill.”
Konyn was born on this dairy farm, which his father began in 1962 in the San Pasqual Valley Agricultural Preserve. The San Pasqual Valley is the northernmost community of the City of San Diego, and borders the City of Escondido. “At one time there were more than 200 dairies in San Diego County, Konyn notes. “Now I’m one of only three.” He began working on the dairy nearly as soon as he could walk, and after getting a degree in Dairy Science from Cal Poly San Luis Obispo in 1992, purchased the business with his wife from his father, expanding the leasehold from 100 acres to its current day 250 acres. In 2002, the Konyns won the Outstanding Young Farmer and Rancher award from the California Farm Bureau, and in 2003, were selected first runners up in the country by the American Farm Bureau.
In 2007, they opened San Pasqual Valley Soils, a 13-acre composting facility on adjacent land. The composting site has helped turn what was once a major dairy liability and expense — manure management — into an asset, and a supplemental revenue stream. San Pasqual Valley Soils also accepts yard trimmings, agricultural residues, straw, wood shavings, and wood chips to compost with the dairy manure, and has developed a diverse line of composts, mulches and planting mixes, including an Organic Materials Review Institute (OMRI)-listed compost and raised garden bed blend. The facility is permitted for 77,375 cubic yards of feedstock annually.
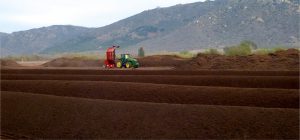
San Pasqual Valley Soils, a 13-acre composting facility, was started by the Konyns in 2007 to manage dairy manure. Adjacent to the dairy, it composts a variety of organics.
Food To Feed
The dairy has been collecting brewery grains to feed its herd of about 880 milking cows, plus its complete young stock replacement program, since 2000. Food scraps, fruits, vegetables and discarded bakery materials were added in 2012. It currently collects and feeds about 20 tons/day of this material. Fruit pulp collection began in 2014, and accounts for 270 tons/month. Discarded bakery products add up to another 130 tons/month, and finally, brewery grains exceed 320 tons.
Collection and feeding opportunities for these feedstocks grew to a point where Konyn decided to establish a third business, K.D. Farms Trucking, Inc. In addition to providing control of hauling costs and customer service, it allows him to improve the quality of the feed, especially bakery materials, which are often collected in a packer truck. Once compacted, contaminant removal is not possible. K.D. Farms Trucking collects the bagged bread and tortillas and other bakery discards loose. When the 3-cubic yard (cy) dumpsters of this material arrive at the dairy, they are emptied by a forklift with a rotator attachment, and everything is depackaged by hand.
“Between the truck and trailer used for collecting the dumpsters, the forklift and rotator, and personnel doing the collection, receiving and depackaging, it’s an equipment and labor intensive operation,” Konyn says. “But it’s excellent feed that far exceeds the equivalent of what’s available on the market.”
K.D. Farms Trucking collects seven days a week, and depending on the type of material and volume generated, a 3-cy dumpster, or a 20 or 40 cy roll-off is used. “My drivers are on the road fulltime,” he adds. “They are also encouraged to procure new accounts, so they’re my sales team too. We currently collect from about 30 locations, some of them multiple times a week, and that number is growing monthly.” Juice manufacturers, bakeries, bread factories, tortilla manufacturers, breweries, produce packaging facilities and farms are examples of the types of businesses serviced. These feedstocks do not need to be cooked prior to feeding the dairy herd, as they contain no meat.
The dairy’s feed bill is substantial, at about $250,000/month. The food scraps collection program has its own overhead, but does help offset a small percentage of total feed costs. “Overall, this program saves my business money, and those we collect from realize considerable savings in disposal costs, and it creates local jobs,” Konyn explains. “Add in the environmental benefits, and the dairy’s sustainability really moves to a higher level we’re proud to be at.”
Two nutritionists are on the dairy staff, one for young stock and one for the adults, constantly fine-tuning the dietary program for the herd. In addition to the bakery products, brewery grains and food scraps collected for feed, almond hulls, canola pellets, alfalfa, haylage, rolled corn, whole cotton seed, dried distillers grains, mill run and beet pulp are components of the recipe. Feed is adjusted to the nutritional requirements of the herd based on age, stage of pregnancy, and milk-producing status. The food scraps collected increase the feed’s nutrient diversity and help increase the protein of the herd’s diet as well.
“This is such a complement to our composting program, and resource management in the region in general,” notes Chuck Voelker, VP Sales & Operations at San Pasqual Valley Soils, Inc. “We’re going to need lots of efforts like these to help San Diego meet the requirements of AB 1826.” And this is certainly true, as currently there is little infrastructure in San Diego County for complying with the law, which requires California jurisdictions to implement an organics recycling program on and/or after January 1, 2016, and phases in mandatory compliance for the largest generators of compostable discards, beginning with businesses that generate 8 cy or more a week. Businesses that fall into this tier have to have collection or on-site composting commencing April 1, 2016.
Rich Flammer of Hidden Resources is a composting and zero waste consultant (www.compostingconsultant.com)