Rising costs and challenges of land application lead Wisconsin goat cheese producer to install a complete mix anaerobic digestion system to treat high strength wastewater.
Diane Greer
BioCycle May 2012, Vol. 53, No. 5, p. 38
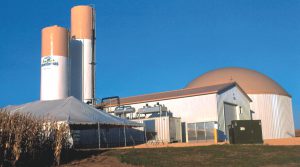
The 500,000-gallon anaerobic digestion system (in background on right) has the capacity to treat wastewater with 25,000 lbs/day of COD.
Producing all this cheese generates significant amounts of residuals. Over the years as volumes grew, so did the economic and regulatory challenges associated with hauling the waste to area farms for land application. “The problem was we needed too much land to apply our wastewater,” explains Rossard, a second generation cheese maker and manager of plant operations. Hauling costs rose as the need for additional land required the company to transport residuals further and further from the plant.
About seven years ago, Rossard and Solandt, president of the company, decided to find a more sustainable option. After exploring alternatives, Montchevré embarked on a $3.5 million project to install an anaerobic digestion system that produces electricity for sale to the grid. The project, completed in fall 2010, was financed in part with a $550,000 low interest loan from the Wisconsin Department of Commerce Energy Program, funded by the American Recovery and Reinvestment Act of 2009.
Regulatory Challenges
Montchevré produces a wide variety of fresh, soft-ripened and aged goat cheese and goat milk yogurt. The goat milk is purchased from 350 family farms in Wisconsin, Iowa, Minnesota and northern Missouri. Waste generated during production is composed of wash water, permeate and whey, a by-product of the cheese making process. (About 20 percent of the goat milk used in the process is whey.) In 2011, a total of 21 million gallons of this high strength waste was generated. It contains high levels of COD (chemical oxygen demand) and BOD (biological oxygen demand) (Table 1).
Under Wisconsin law, many farmers are now required to develop nutrient management plans that identify the location, rates and timing of manure, fertilizer, biosolids, wastewater and other applications to the land. “Requirements are such that they are not allowed to put on more nutrients then the crops can take in over a rotation,” explains Sara Wallling, bioenergy policy advisor at the Wisconsin Department of Agriculture, Trade and Consumer Protection. “In Wisconsin the land availability for spreading waste streams from food processors and cheese plants without prior treatment is becoming a very limited commodity. More and more farmers are less able or willing to take on those waste streams in land application scenarios and so our food processors and cheese plants are finding it more and more difficult and more and more costly to get rid of that waste stream.”
One of the limiting factors preventing farmers from taking some of these wastes is the high phosphorus content. Water quality concerns at the state and federal level are resulting in more stringent phosphorus regulations. “We are seeing phosphorus in all our Wisconsin lakes,” Walling explains. “Reducing phosphorus loads is going to be key to keeping the lakes from eutrophication and algae blooms in the summer.”
Spreading waste containing goat cheese whey faces an additional challenge. Goat whey is highly acidic, with a pH of around 4.3. “In some cases the land can’t accept these acid whey wastewater streams coming from the cheese plants for more than a few years before the potential is there for crop production decline,” Walling says.
Technology Selection
In 2007, Montchevré enlisted Procorp Enterprises LLC in Milwaukee to evaluate alternative wastewater management technologies. Procorp analyzed three options: sequencing batch reactors (SBR), conventional aerobic treatment systems and anaerobic digesters. Evaluations of the SBR and aerobic technologies looked at discharging effluent from the process to the Village of Belmont’s wastewater treatment plant (WWTP) for further treatment, or discharging fully treated water into a nearby stream. The anaerobic option evaluated discharging the effluent to the WWTP.
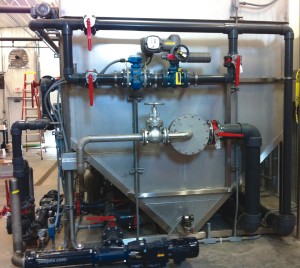
Effluent exiting the digester is separated into solid and liquid streams using a dissolved air flotation system (end view pictured above).
A subsequent evaluation of three types of anaerobic digestion systems — complete mix, UASB (upflow anaerobic sludge blanket) and fixed film — found the complete mix system preferable for dairy wastes high in solids and fats. “Pretreatment would be required prior to the waste entering UASB and fixed film digesters,” he says. “Pretreating the wastes removes the organics, which is the energy that we want to harness to produce methane.”
Procorp designed and installed the 500,000-gallon complete mix anaerobic digestion system composed of one digester tank with a capacity to treat 25,000 lbs/day of COD. The COD destruction rate is estimated at 93 to 95 percent; COD loading rates for the system, which is still in startup mode, are currently 10,000 to 15,000 lbs/day.
To allow room for future expansion of the cheese processing facility, the digester system is located one-quarter mile from the plant. A lift station, capable of handling flows from 70,000 to 120,000 gallons/day, captures and pumps the waste stream composed of whey and wastewater from the cheese plant to a 65,000 gallon equalization tank adjacent to the digester where the pH is adjusted and the waste is mixed. The equalization tank also balances the flow and loading rates to the digester.
Biogas is captured in the digester’s cover and piped to a gas conditioning system that employs an iron sponge and a chiller to decrease hydrogen sulfide (H2S) and moisture levels. Reducing H2S is critical since it can combine with moisture to form sulfuric acid, which is highly corrosive to pipes and engine parts. “The iron sponge is working very well and it is very efficient, reducing H2S levels from 5,000-ppm to 15-ppm,” Rossard says.
When fully loaded the digester is expected to produce 93,500 cubic feet per day (cf/d) of biogas. The biogas fuels a 335 kW GE Jenbacher engine capable of generating 5,270 kWh/day of electricity. At current flows and loading rates the digester is producing 180-kWh of electricity. Waste heat from the engine is used to heat the digester. Electricity is sold to Alliant Energy under a renewable buy-back program. “The price is very competitive,” Rossard notes. “That is something that pushed us to go ahead with the project.”
Effluent from the digester is separated into solid and liquid components using a DAF (dissolved air floatation) system. Most of the solids are returned to the digester. Any solids not returned are land applied. “The volumes will be very low,” Fessler explains. “The solids production is in the neighborhood of 7 to 10 percent. This means that 7 to 10 lbs of solids are produced for every 100 lbs of COD destroyed.”
A system to recover the phosphorus and ammonia in the solids by converting the material to struvite, a valuable fertilizer, is being considered. Current commodity pricing for struvite is around $300/ton. “Testing with the University of Wisconsin found that struvite performs well as a commercial starter fertilizer,” Fessler explains. “It is slow release, which further protects ground waters from nutrients leaching into the soil.”
The struvite system will help Montchevré meet the more stringent Wisconsin Department of Natural Resources’ direct discharge rules that are further limiting phosphorus and ammonia levels in land applied wastes. The ultimate goal is to eliminate land spreading entirely, cutting out the cost of hauling the solids for land application.
The company is installing an aerobic digester to further treat the liquid portion of the digester effluent. The system is designed to reduce the remaining organic and nutrient loading to less than household concentrations going to the WWTP, thereby reducing Montchevré sewage surcharges. The treated effluent will be sent directly to the village’s WWTP. If the company outgrows the WWTP’s capacity in the future the wastewater will be clean enough for discharge to a nearby stream.
Smooth Transition
Processing the company’s wastes in the digester is resulting in a 10-fold decrease in COD levels. “It is working,” Rossard says. “COD levels entering the digester of 20,000 to 30,000 mg/l range are reduced approximately to 3,000 mg/l in the effluent exiting the DAF.” Adding the digester resulted in minimal changes to the operation. Care is required to insure that chemicals used to clean the equipment do not kill the microbes in the digester. “We have a good chemical program,” he explains. “We did not have to change that much. We are always looking at the sanitizers we are using to make sure they do not kill the bugs.” Currently the cheese plant mainly uses chlorine with minimal amounts of other biocides.
When Rossard started making cheese, he never imagined that he would have to deal with a wastewater treatment system. “It is another challenge,” he says. “Making cheese is somewhat like running a digester. In both systems you need to be concerned with pH and dealing with the culture of microorganisms. It is a different world but it is interesting.” To help manage the system, Montchevré added a full time staff position and expects to add another job onsite once the aerobic system is completed at the end of 2012. And treating its own waste will allow the company’s continued expansion in its current location, which translates into more jobs.
Rossard is still discovering a few kinks in the system but is confident it will become more efficient and easier to run over time. The economics are also starting to look better. “We thought it was a good idea to make power with our own by-product and get some money back to pay some of the cost of the system,” Rossard explains. “But we really don’t.” The real value may well be cost avoidance in the future. “The idea is to get rid of the hauling,” he adds. “It is really huge and with the price of oil going up I am sure in the next few years we will be happy to have spent the time and money to build this system.”
Diane Greer is a Contributing Editor to BioCycle.