Wisconsin farm digester processes 82 percent manure, 12 percent bed pack/manure, and 6 percent food waste.
Dan Emerson
BioCycle May/June 2019
In April 2015, the anaerobic digester at Allen Farms in Oshkosh, Wisconsin began full-scale operation. Developed as a joint venture by the University of Wisconsin-Oshkosh (UWO), BioFerm/Viessmann Group (technology provider), Focus on Energy and the Wisconsin State Energy Office, the 130-cow dairy processes 18 tons/day or 6,500 tons/year of manure scrape, used bedpack and food waste. The total digester footprint is approximately 2,460 square feet, according to Brian Langolf, director of biogas systems and research development at the University of Wisconsin-Oshkosh.
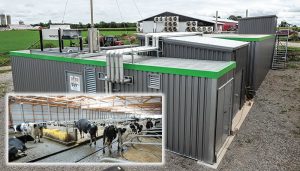
Allen Farms installed an anaerobic digester consisting of two fermentation vessels. Manure, used bed pack and crop residues from the 130-cow dairy operation are processed.
The system consists of two fermentation vessels (80,000 gallons total), a feeding hopper and a combined heat and power unit that can continuously power supply a 64 kW CHP (combined heat and power) unit supplied by 2G Energy of Midland, Texas. Its thermal capacity is 101 kW. According to the latest data from U.S. EPA AgSTAR, 25,900 cu ft/day of biogas are produced and 481,800 kWh/year are generated. All of the electricity is exported and sold to the local power utility, Wisconsin Public Service, and the heat is being used for the digester process, as well as adjacent buildings on the farm.
To help fund the installation, the Wisconsin Department of Administration and State Energy Office provided a $125,000 grant. Construction began in June 2012; filling of the tank began in April 2013. Allen Farms went through an upgrade in spring of 2015 with the addition of a new free stall barn and robotic milking technology. Feedstocks going to the digester include liquid manure from the free stall barn, solid bedding from nonmilking cows, crop residuals from on-site, and industrial food waste substrates from a nearby food processor.
UWO manages the feeding recipe, which is 82 percent manure, 12 percent bed pack/manure, and 6 percent food waste, explains Langolf. “The first priority is to manage all of the waste inputs from the farm (manure scrape, used bed pack, and other miscellaneous crop residues), then we supplement with some food waste to boost [biogas] production. We have to balance the recipe based on the Organic Loading Rate (OLR) and Hydraulic Retention Time (HRT) to ensure we keep the system in balance and all the microorganisms happy.”
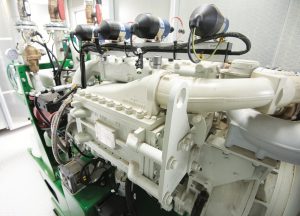
Electricity produced from the farm’s 64 kW combined heat and power unit is sold to Wisconsin Public Service. Recovered heat is used for the digester process and in adjacent buildings on the farm.
From the farmer’s perspective, owner Dave Allen says the most important thing in feeding the digester is “consistency. Moisture and dry matter content — all of those things matter,” he notes. “It’s very similar to feeding a cow.” Digester loading is done continuously throughout the day —solid material through a feed hopper system and liquid manure via a feed pump. The quality of the biogas produced ranges from 58 to 60 percent methane content, with a yield of 18 to 20 standard cubic feet per minute. All of the raw digestate (1.4 million gallons per year) is stored in an open lagoon and land applied as fertilizer to grow crops at the farm, which is about six miles northwest of Oshkosh.
“Everything that I have heard from Dave indicates that he has been very happy with the product and has seen benefits compared to applying raw manure,” Langolf says, citing low odor, better pathogen kill, better nutrient availability, and better crop growth. The revenue from the power purchase agreement goes directly to the university to help offset operations and maintenance of the digester system and support educational programs. The digester is used as a research and education tool for faculty and students, a “living learning laboratory,” he adds. The farm gets the manure management benefits and also the waste heat from the digester for heating needs on the farm.
Lessons Learned
Operating the system has involved a number of challenges throughout the years. “The initial primary challenge was to modify the system so that it was robust enough to operate continuously through a Wisconsin winter,” notes Langolf. “Some modifications had to be made to the original design. We also had to divert the wash water from the farm, since the chemicals being used were causing inhibition and foaming in the digester. Things are operating very well now and we just need to keep up with normal maintenance as well as monitor the biology and chemistry to keep the entire system in balance.”
Current challenges — similar to many digester operations in Wisconsin — are around costs to operate vs. what value can be realized, Langolf adds. “Barriers at the state and local level exist to cost-effectively develop behind the meter options [e.g., on-site consumption], net metering, and pipeline injection. And currently, no real monetary value is assigned to the environmental benefits anaerobic digestion can provide to the Wisconsin agriculture industry.”
For his dairy farm, Allen is realizing multiple benefits. ”There really is an endless list of advantages,” he says. “I’m taking the manure I already have, making energy, and methane isn’t being released into the atmosphere.”
Dan Emerson is a Contributing Editor to BioCycle.