Regional waste authority in New York State switches to extended aerated static piles in bunkers to manage food waste at existing yard trimmings composting facility.
Claire Siegrist
BioCycle November 2014
The Onondaga County Resource Recovery Agency (OCRRA), a nonprofit waste management organization in Onondaga County, New York, manages the waste for 33 out of 35 municipalities in the county and operates two composting facilities, one waste-to-energy (WTE) facility, and two transfer stations. As a nongovernmental agency, OCRRA does not receive tax support for its programs, and is funded primarily through tipping fees, sale of recovered recyclables and compost, and electricity revenues generated from its WTE facility.
OCRRA’s two composting sites are the Amboy facility in Camillus, about 10 miles west of Syracuse, and the Jamesville facility in the town of Jamesville. Both accept yard trimmings from the community and sell premium grade compost and mulch. The Amboy Site also accepts food waste from institutions and businesses.
EASP Pilot
The Amboy facility opened in 1994 at an abandoned Department of Transportation property. The 9-acre site used a turned windrow system to produce finished compost from yard trimmings. Piles were turned using a John Deere loader with a 3-cubic yard (cy) bucket. In 2005, OCRRA completed an audit of Onondaga County’s waste stream, including commercial, institutional and residential waste. The findings indicated that over 15 percent of the waste stream was food and over 20 percent was soiled paper. The waste audit made clear the need for a larger system for organic material collection and processing.
In 2008, the agency initiated a pilot project at the Amboy site, with the help of O2 Compost, to test an extended aerated static pile system for large-scale, high volume pre and postconsumer food waste composting with the already accepted yard trimmings. “The Extended ASP (EASP) method of composting is the same as ASP composting, except that new compost cells are constructed directly on the flank of the preceding compost pile,” explains Peter Moon of O2 Compost. Essentially, any interstitial spacing between piles or zones is removed.
OCRRA and O2 Compost incorporated principles of cover systems and aerated in-vessel containers into Amboy’s EASP system. The pilot focused mainly on the feasibility of operating an EASP system, especially through the harsh winter conditions of Central New York, and the mix ratios. The project proved the EASP system would operate efficiently, even with external weather events. The most appropriate mix ratio to negate odors and maintain a carbon-rich environment was three parts yard trimmings to one part food waste. OCRRA was able to utilize this $33,000 system for five years before commissioning the new facility. During the pilot project period, over 30,000 cy of yard trimmings and 4,000 cy of food waste were composted in the EASPs (the balance of yard trimmings were composted in windrows). “Once we began using EASPs for the food waste mix, we realized that the efficiencies and method provided to be of value, and we totally converted over to EASPs for composting all material at Amboy,” explains Greg Gelewski, OCRRA Recycling Operations Manager.
OCRRA hired GHD Consulting Engineers, LLC to redesign the composting operation at Amboy to an EASP system in order to be better equipped to handle larger volumes of food waste. The $2.4 million retrofit was funded through OCRRA’s operational and capital funds. OCRRA’s 15 member Board of Directors and the community were convinced by the pilot project that a retrofit was needed. After conceptual designs were drawn and the facility was permitted with the New York State Department of Environmental Conservation (DEC), construction began. The facility was completed about six months later, in November 2013.
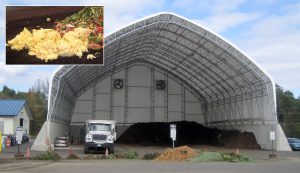
All food waste is unloaded in a ClearSpan fabric building to reduce storm water impacts on waste receiving and mixing operations. Among special loads of food waste processed was the 800-pound butter sculpture from the New York State Fair (inset).
Major modifications implemented under the retrofitting project included improved leachate collection, better odor controls, and an 80-foot by 100-foot materials receiving area covered by a ClearSpan High Series fabric building to create a more controlled environment and to reduce storm water impacts on waste receiving and mixing operations. The EASP system has enabled OCRRA to quadruple the amount of compost produced in the same amount of space due to elimination of turning aisles and less void space in piles. The energy efficient blowers use one-quarter of the energy that the turned windrow system consumed as diesel fuel for turning with a loader; less than 2,000 kWh of electricity are used each month to power blowers in the eight aeration bays. “We made Amboy Compost Facility’s operation as simple as possible so it could be replicated by other counties,” notes Gelewski. In response to the success of OCRRA’s pilot program and facility expansion, the agency’s counterparts in Ulster County, New York are currently working with O2 Compost on a similar EASP pilot project.
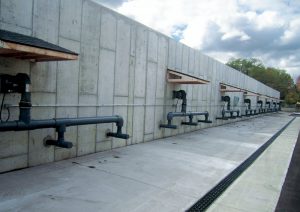
Energy efficient blowers use less than 2,000 kWh/month of electricity to aerate the bays. Material is composted in the bays for 28 days.
Food Waste Flow
The Amboy Compost Facility receives source separated organics from commercial facilities and institutions. OCRRA has three recycling specialists that educate the food waste generators and the community about proper sorting practices. Generators hire haulers to bring the food and yard waste to the Amboy Facility, where trucks are weighed in across an automated scale. Although there is no mandate in Onondaga County to divert organics from disposal combustion, OCRRA’s competitive pricing provides a financial incentive that attracts customers to their program. It charges $35/ton for organic waste compared to the $79/ton rate for standard municipal solid waste — a difference of $44/ton for composting food scraps.
Currently about 44 businesses and institutions in Onondaga County, including Syracuse University, Wegmans Supermarkets and the local shopping mall, participate in the food waste composting program. Although the Amboy Compost Facility receives approximately 6,000 commercial food waste and yard trimmings deliveries each year, OCRRA is looking to increase this number. Amboy is permitted to handle approximately 9,600 tons/year of food waste and 48,000 cy/year of yard trimmings, but according to Gelewski, the facility is currently operating at about one-quarter of its potential capacity.
Local community members can drop off yard trimmings at the Amboy and Jamesville Facilities for a $15 annual pass. With this pass, residents are also able to take up to 6 cy of OCRRA’s general compost product. In 2013, 4,000 residents purchased passes and made over 30,000 drop-offs. By the end of 2015, OCRRA hopes to expand this already successful program and begin a residential drop-off program for food waste.
Receiving And Composting Process
The new EASP system has reduced compost processing time by 60 percent, notes Gelewski. Finished compost is created in 90 days, a significant difference from the 9-month process of the turned windrow system. Upon entry to the Amboy Compost Facility, food waste is brought to the covered receiving area and is immediately mixed with three equal parts of shredded yard trimmings using a Kuhn Knight Maxx VTC 180 vertical mixer. This best management practice limits odors, and helps ensure that there are no complaints from the facility’s neighbors. Compostable bags (Biobags) and plastic film bags are torn, but not shredded, during this process. By mixing and not shredding, the noncompostable plastic bags remain large enough to be removed during the later screening process.
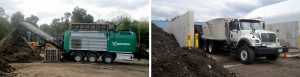
Yard trimmings are processed in a Komptech Crambo slow speed shredder (left). A Kuhn Knight vertical mixer blends 3 parts yard trimmings to one part food waste; the mix is unloaded directly into an aeratedbay (right). Photos by Claire Siegrist
Yard trimmings are processed in a Komptech Crambo 5000 Slow Speed Shredder for primary shred and volume reduction. The Crambo is equipped with a magnet that captures metal objects before they are added to the pile of shredded yard trimmings and other organics. OCRRA collects and recycles this scrap metal. A Vermeer HG6000 horizontal grinder is used for a secondary grind.
After mixing, material is added to one of eight 20-foot by 100-foot aeration bays, where it breaks down thermophilically for 28 days. “OCRRA places a 6- to 12-inch cover layer of finished/unscreened compost on top of the pile to work as a biofilter and as an insulative blanket to ensure that PFRP requirements are met for the materials,” says Gelewski. “This is done for both the primary (thermophilic) and secondary (curing) phases as the proposed Food and Drug Administration’s Food Safety and Modernization Act requires.” (See sidebar for explanation of the proposed USDA/FDA composting requirements; OCRRA decided to comply even though the rule is not final.)
After the first 28 days, the static pile is moistened and transferred to another bay for 28 days of curing. Throughout these eight bays, a system of pipes blow air through the piles at scheduled intervals to help accelerate decomposition and the composting process. Beneath the aeration bays is a leachate collection system that is tied to a 5,000-gallon tank. Leachate is stored and recycled back into the composting system. When heavy rain events occur, the excess water is sent to the local wastewater treatment plant. Once material in the curing bays cools down to below 110°F, it is moved to a finishing pile where it will mature for an additional 28 to 30 days.
The finished compost is screened using a McCloskey 621 trommel, with both half-inch and one-quarter inch screening drums, to create both a general purpose and a premium product. Following screening, the larger chunks of material, which typically include compostable plastic utensils and cups that have not broken down, are put back into the composting system for processing for a second and final time. These screened overs first go through the slow speed shredder and the mixer on the tip floor, and then are composted again.
The Amboy Compost Facility addresses film plastic contamination through education at the source and use of air separation during the trommel screening process. Operators working at the Amboy facility also watch loads and note the haulers who deliver materials with visible contaminants. Most of the time, they are able to trace the contaminant back to its source. OCRRA’s recycling specialists will visit the company or institution in question to educate employees and make sure signage is correct to help minimize future contamination. For the OCRRA program, use of compostable bags/liners is voluntary and is at the discretion of the food waste generator and hauler. Some generators prefer liners for in-house containers; others conduct a clean cart exchange and have no need for a bag or liner.
Compost Markets
Each year, the Amboy site produces over 36,000 cy of compost. OCRRA participates in the US Composting Council’s Seal of Testing Assurance (STA) program. Its premium compost is sold in over 22 local hardware and landscape stores. Using a Pro-Tech Compost Bagger, the Amboy facility can bag over 10 pallets per day and has the capacity to bag over 100,000 bags annually. “We cannot keep our compost in stock,” notes Gelewski about its high quality, consistent product, which leaves the Amboy facility faster than it can be made.
OCRRA’s participation in the US Composting Council Seal of Testing Assurance (STA) program has opened up a lot of private and public sector engineering projects for its compost; more engineers and Department of Transportation offices are specifying USCC STA composts for their projects. OCRRA’s finished compost has been used as more than just a soil amendment. Regionally it has been the prime source of organic material for many green infrastructure projects — from the green roof of Jacob Javits Center in New York City and the Rosamond Gifford Zoo in Syracuse, to engineered wetlands and the Onondaga Lake revitalization project, and the county’s nationally recognized “Save the Rain” program.
The agency sells compost in bulk to soil blenders, aggregate producers and specialty mix providers; OCRRA does not currently produce or market any blended products but anticipates entering that market to meet the industry’s demand. As for revenues, the agency projects that 2014 compost revenues will exceed $400,000 — light years ahead of traditional revenues of $50,000 in 2008 when the pilot project was commissioned.
“We are doing everything we can to be a flagship facility for New York State, from currently being the newest and largest permitted food waste facility, to handling special projects like composting zebra mussels and carp from a hydro plant cleanout, and [manually] depackaging a 53-foot trailer of lettuce, to closing the loop for the Marcellus School District — where they were able to put the compost they helped generate back onto a new softball field,” explains Gelewski. “The Amboy facility also composted the 800 pound Butter Sculpture for the New York State Fair and the American Dairy Association and Dairy Council!”
Claire Siegrist is studying Natural Resources Planning and Management at Cornell University. She also educates students about proper waste management practices through work as a Sustainability Coordinator at Cornell.