Optimizing space utilization is an issue composters must face when contemplating how to expand, particularly if there is limited room for a bigger pad.
Craig Coker and Gregg Hennigan
BioCycle June 2016
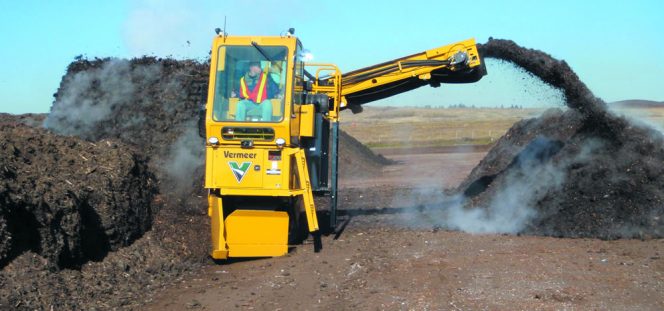
An elevating face compost turner aerates and moves the compost during each pass using lifting faces and transverse discharge conveyors. Photo courtesy of Two Rivers Marketing
This is what Rhode Island Resource Recovery Corporation (RIRRC) did when upgrading its yard trimmings composting operation on a fixed-size footprint at the state’s primary solid waste management facility in Johnston. “In 2007, we were turning with a loader, which took almost a month to turn all the piles,” notes Brian Card, Director of Operations for RIRRC. “We were hard-pressed to fit everything on our pad. We bought a Vermeer CT718 straddle turner and were able to get all our materials processed in six months or so, even with slightly smaller windrows, than we were with the larger windrows turned with a loader over 8 to 9 months.”
The RIRRC operation handles about 40,000 tons/year of yard trimmings, all of which are ground with a Diamond Z tub grinder and CBI horizontal grinders to prepare the feedstocks for composting. The compost had been used as alternative daily cover at the landfill, but in order to preserve airspace in the landfill, RIRR decided to start marketing and selling the product in 2009. That forced an evaluation of better turning methods, which led to the decision to purchase the Vermeer straddle turner. “We’re on the verge of starting a project to reevaluate, again, how we turn and manage our compost piles as the landfill is going to expand and use up part of our footprint,” says Card.
If turning is done with a tractor-pulled turner, upgrading to a straddle turner will produce similar increases in processing density. If the facility is already using a straddle turner, one option would be to upgrade to a larger machine. The largest turners on the market today have windrow tunnel sizes of 10-feet tall by 26-feet wide, so windrows contain almost 6 cubic yards of material per linear foot of windrow (cy/lf). Compared to a more traditional turner tunnel size of 7-feet tall by 18-feet wide (2.85 cy/lf), the processing density would go up more than 70 percent. However, there are significant cost implications of upgrading straddle turners that need to be compared to the cost of pad expansion, or even of relocation to a new site.
Another alternative is to consider converting to a continuous stack composting approach using an elevating-face turner to move materials across the composting pad. A continuous stack method most often uses one pile that is 8 to 9 feet tall and covers the whole processing area, eliminating the space between windrows. This approach has also been called trapezoidal pile composting, and is seen frequently at European facilities where land area is at a premium.
Elevating-face compost turning equipment aerates and moves the stack during each pass using lifting faces and transverse discharge conveyors. “With a continuous stack process, more material fits in a smaller amount of space because there aren’t gaps between windrows,” explains Jeff Bradley, recycling and forestry product manager at Vermeer. “Continuous stacking can allow a site to produce more compost per acre. This maximizes the footprint and the amount of material on the site. For sites in an urban setting with limited space, this is a big advantage to help address increased inflows of feedstocks.”
Elevating-face machines can be used to turn windrows as well. A wide conveyor with hundreds of teeth lifts compost up and over the top of the machine, inverting the windrow. “Basically, it breaks the compost off the pile into chunks and as those chunks travel up the face they are broken apart,” says Bradley. “The compost falls off the back of the machine into a windrow or is moved over by a transverse conveyor to a new stack.”
For a continuous stack configuration, the entire pile is laterally moved across the composting pad with each turning. “In the typical continuous stack setup, the incoming material comes in on one side of the site, and every time the stack is turned, the material moves away from that side and toward the screening plant,” he adds. “Loaders aren’t needed to move the material here and there, because by the time it gets to the other end of the site, the finished product has naturally moved to the screener area. The loader has minimal movement to the screen, which improves efficiency.”
Weighing The Options
A variety of factors must be considered when evaluating processing options. The geographic location of a facility, whether it has a dirt or a finished pad and the raw material it handles play a role. For example, very wet and heavy material should be lifted and aerated more than lighter material. A windrow process may be better at accomplishing that task. In areas that receive a lot of rainfall, the higher surface area-to-volume ratio of windrows would allow moisture to evaporate from the windrows faster. Composting facilities on large, rural sites may have little need to consider alternatives to turned windrows.
There also may be water savings with continuous stack composting, which could be particularly valuable in dry regions. Sites that don’t get a lot of rain have to water piles frequently. “With continuous stack, the compost is not exposed to the air as much as with windrows, so they’re not losing moisture to the atmosphere as quickly and may be able to reduce the number of times water needs to be added,” Bradley explains. In addition, continuous stack piles may absorb more rainfall and thus reduce the amount of storm water runoff that must be managed, which is becoming an increasingly complex problem for compost manufacturers.
Facilities interested in utilizing a continuous stack composting method need to gauge the size of its stack based on what Bradley calls the “dwell time” of the compost on that pad. For example, if the composting facility has a 10- or 12-week processing time, it has to allow for that much room on its site to be able to handle 12 weeks’ worth of material. If it has more than one stack, it needs room for that, too. He offers this general advice. First, look at the economics of a conversion. Estimate the cost of operation of continuous stacking versus windrows. Also, determine if any infrastructure changes might be needed. For instance, if the facility’s current pad is dirt, an asphalt or concrete pad may be needed to support the elevating-face compost turner.
A facility’s footprint could change in a continuous stack setup because less space is required to process the same volume of material in a windrow configuration. Layout of a facility may need to be altered. As mentioned, continuous stacking allows incoming materials to be placed on one side of the site. Every time a stack is turned, it should move the finished material toward the screening system, potentially reducing loader movements.
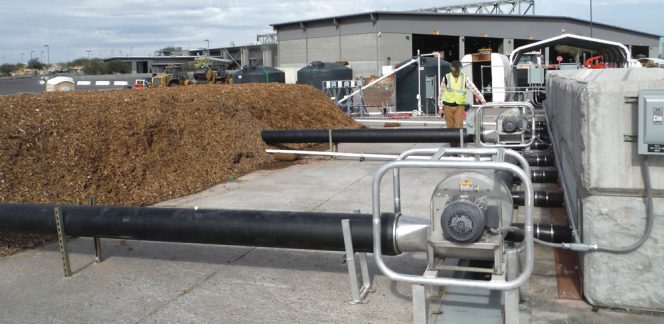
The City of Phoenix’s new turned aerated pile composting facility uses a continous stack design with an aeration floor system. The site has capacity to compost 220,000 tons/year of food scraps and yard trimmings. Photo courtesy of Green Mountain Technologies
Bradley points out that some windrow operations are adding hard-surface pads, like concrete. Here again the advantages of a continuous stack process show up. If a company or municipality can cut its facility footprint in half or more, then they will need less concrete. “Consider a 100-acre windrow site,” he explains. “By implementing continuous stack processing, that footprint potentially could be reduced to 50 acres. With a TAP system, that could go down to 32 acres. Continuous stacking has the potential to reduce the investment in land and still produce the same volume of compost or more in a faster timeframe.”
Craig Coker is a Senior Editor at BioCycle and a Principal in the firm Coker Composting & Consulting (www.cokercompost.com), near Roanoke, Virginia. He can be reached at ccoker@jgpress.com. Gregg Hennigan is a features writer with Two Rivers Marketing in Des Moines, Iowa. He can be reached at Greggh@2rm.com.