Top: Dried slurry after mechanical screening through 5/32-inch mesh. Several of the blue slivers were determined to be coated paperboard.
Craig Coker
In Part I of this article series, we defined microplastics (MPs) as small plastic fragments that are less than 5 millimeters (mm) in size, which is slightly larger than one-eighth inch. MPs can be introduced to agricultural soils through products engineered to be small, such as plastic-coated controlled release fertilizers, treated seeds, and capsule suspension plant protection products. They can be introduced via plastic mulching, contaminated soil amendments, irrigation water, atmospheric deposition, roads and litter. MPs can also be formed during and as a result of food waste depackaging.
Some states, like Vermont, are beginning to think about regulating microplastics in food wastes. In February 2023, the Vermont Agency of Natural Resources (ANR) issued a draft policy statement that said, in part, “…it is the Agency’s policy that source separated food residuals shall not be mixed with heavily packaged food residuals at the point of generation.” While the policy will apply to generators, haulers and processing facilities, the bulk of the compliance burden will fall on generators who will have to separate lightly-packaged food more suitable for manual depackaging from heavily-packaged food amenable to machine depackaging.
Depackaging source separated food wastes is very labor-intensive if done by humans. As a result, a number of depackaging equipment systems have been introduced to the U.S. organics recycling market. No data are available on which depackaging methods produce MPs or in what quantities, but it is reasonable to assume that machines exerting force on packaged foods risk production of MPs due to shattering of brittle plastics like some high-density polyethylene (HDPE) and polypropylene (PP) and plastics that are easy to break, like polystyrene (PS).
Microplastics Screening
One depackaging technology provider has invested in a solution to remove MPs from the extract derived from its depackaging systems. Scott Equipment Co., in New Prague, Minnesota, is a 55-year-old company specializing in agricultural and industrial processing equipment. It manufactures and sells the Turbo-Separator and THOR lines of depackaging equipment. About 200 of its units are installed at anaerobic digestion (AD) and composting facilities in North America, with another 400 in use worldwide.
Scott Equipment is introducing a new mechanical screening system that is an add-on to its depackaging systems. Named Cleansweep, the unit is 8-feet long, 3-feet wide and 6-feet tall, and is designed to operate adjacent to Scott’s depackaging models. The depackaged extract (slurry) is swept through a stainless-steel screen with 5/32-inch (0.15” or 3.9 millimeters) mesh holes and can process up to 20 tons/hour of extract. The machine operates as a fine mechanical screener and does not distinguish between organic and inorganic materials, only particle size. For the mechanical screener to operate effectively, the solids content of the organic slurry must be pumpable (e.g., poured out of a cup unassisted).
In addition to a series of alpha (i.e., internal) tests at its R&D lab, Scott Equipment has been running beta (i.e., external) tests on the Cleansweep at the AgriEnergy AD facility in Exeter, Maine, Reinford Farms in Mifflintown, Pennsylvania, and the City of Muscatine, Iowa’s Water Resources Recovery Facility (WRRF). All of the facilities utilize Scott’s depackagers. AgriEnergy’s main AD codigestion feedstocks are grocery store residuals. The only challenge it had with these tests was that corn husks in the grocery wastes tended to blind the 5/32-inch screen and stick/stalk foods tended to “spear” through the screen (similar to woody spears found in composts screened with a trommel).
Consequently, AgriEnergy set up the Cleansweep to process the digestate coming out of its continuous stirred-tank reactors prior to dewatering with a screw press. (AgriEnergy reuses the solids from dewatering for animal bedding at its partner’s location, Stonyvale Dairy Farm). The Cleansweep was able to capture MPs from digestate, which Scott Equipment filtered through cheesecloth. The remaining MPs were too small to be measured in a gram scale, meaning the result was estimated as at least 99.95% purity (by weight) of the filtered digestate, and 0.05% (by weight) rejected MP particles. The results of this trial led to a redesign of the Cleansweep agitator to incorporate a brush and spray nozzles to prevent screen blinding (see last section of article below).
Scott Equipment also ran tests on grocery store residuals and wastes from an ice cream manufacturer depackaged through a THOR installed at Casella Organics’ depack facility in Williston, Vermont. The extract was filtered through cheesecloth and the resulting rejects were weighed. Like the AgriEnergy trial, the Cleansweep was able to achieve 99.95% purity (by weight) on the filtered extract. Scott Equipment asked researchers at the University of Vermont (UVM), who have been studying microplastics in organics for several years, to examine both the feedstock and the filtrate from the Cleansweep. As was reported in Part II of this series, UVM researchers use a 40x microscope to look for, segregate, and count MPs.
The researchers found 5,000 MPs in the depackager extract, but also found 5,000 MPs in the Cleansweep filtrate — although the MPs in the filtrate were much smaller than the MPs in the extract. Essentially grains of sand and MPs less than one-eighth inch in size were passing through the screen; any MPs larger than 5/32-inch in size were captured in the reject stream. The reality may be that no mechanical filtration system can remove 100% of anything. Because most regulatory limits on inert materials in composts are based on weight, particle counts are useful but may not be as relevant when testing for presence of MPs in end products.
Muscatine Trials
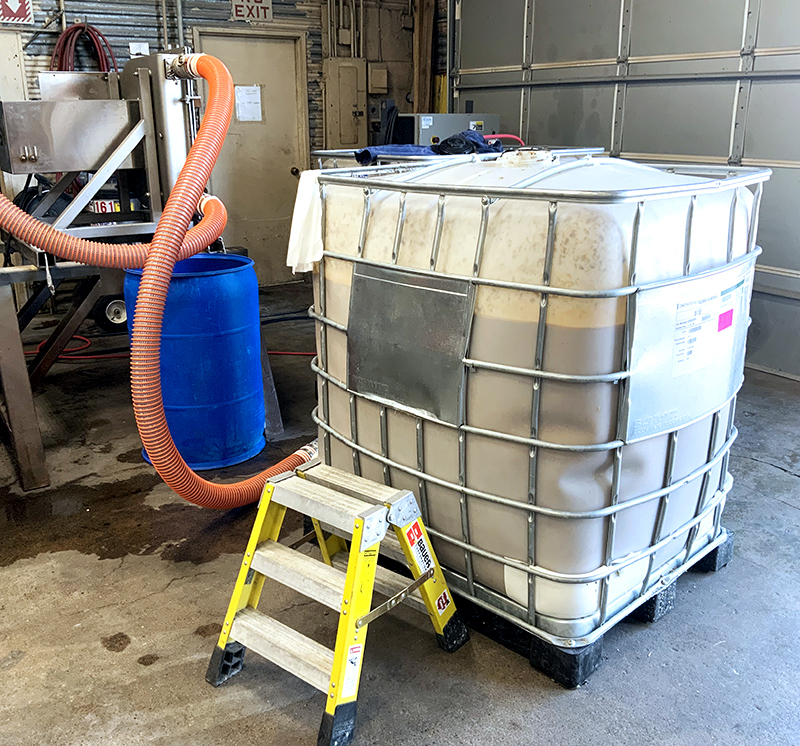
One of five IBC (bulk container) totes (275 gallons each) of grocery store slurry sent to Scott’s R&D lab by the City of Muscatine WRRF for testing Cleansweep enhancements. Photos courtesy of Scott Equipment Co.
At the City of Muscatine’s WRRF, Scott Equipment tested grocery residuals as well as packaged meat products and pet foods. The screen removed all fruit/produce stickers and rubber bands from the grocery residuals, but also pulled out plastic-like materials such as onion skins. The packaged meat products did not break down to very small particle sizes in Muscatine’s T42 Turbo Separator, so significant portions were rejected by the Cleansweep. The meats that passed through the screening unit were very clean. Pet foods that had high amounts of fat tended to turn into a thick peanut butter-like paste that clogged the screen. Muscatine staff are considering installing two of the screens, one on the front end to process depackaged extract and one on the back end to process the digestate because additional contamination may be introduced into the digesters in their FOG (fats, oils and grease) stream that doesn’t pass through the Turbo Separator.
Scott Equipment completed its enhancements to Cleansweep in May 2023, which are designed to keep the filter screens cleaner while processing chunky and pithy organic slurries, like recovered grocery food slurry. It did additional testing on grocery store slurries from the Muscatine WRRF. Five IBC (bulk container) totes (275 gallons each) of grocery store slurry were shipped to Scott Equipment’s test lab facility in New Prague. The totes were aerated due to stratification of the liquids and solids during shipment. There was a duration of four days between the collection, shipping, and processing of the slurry.
During the testing, each tote was placed next to the Cleansweep system; an LSM50 hose pump was used to pump the organic slurry from each tote to the unit. The overs were rejected at the end of the system and collected and weighed for each tote. The recovered, cleaned slurry was collected in a stainless-steel bulk tank.
In processing the grocery store waste, there was a discernable amount of woody stalks and cellulose from both floral and corrugated cartons, reports Kevin Pedretti, Business Development Manager in Scott’s Recycled Products Group. Since the screens used in the Model T42 were three-quarter inch, both organic and inorganic particles were in the recovered contaminants. The contaminants were collected, air dried, and set aside for analysis. The inorganic contaminants were removed with a tweezer and standard magnification (Figure 1), then separated by type. Photos were taken to create a visual record (Figure 2). Figure 3 illustrates that the screen removed a significant amount of residual contamination, including all produce labels and rubber bands, and almost all foil, film plastic and rigid plastic.
Three-gallon samples of the cleaned slurry were pulled for each of the five IBC totes and screened using two methods. The conventional method employed a 1mm sieve with water and hand agitation to remove the liquids and retain the solids, including any remaining contamination. The second method used a flour sack cloth with tight weave to squeeze out and remove the liquids while retaining the solids. The slurry was then dried over a three-day period and examined. Using a tweezer and standard magnification, small visible particles were removed from the cleaned organic slurry. The resulting amount from the 3-gallon sample was less than the gram scale could detect (see feature photo of air dried slurry at the top of this article) and Figure 4, the contaminants.
The Cleansweep will be commercially available for sale in the summer of 2023.
Craig Coker is a Senior Editor at BioCycle CONNECT and a Principal at Coker Composting and Consulting near Roanoke VA. He can be reached at ccoker@cokercompost.com