New Earth Compost and Soils upgraded its Conroe facility to process biosolids and added a mobile horizontal grinder to increase its off-site processing services.
Larry Trojak
BioCycle May 2013, Vol. 54, No. 5, p. 24
New Earth Compost and Soils — with facilities in San Antonio and Conroe, Texas — was born 15 years ago out of a local meat packing plant’s long-standing need to dispose of manure from its operation (see “Composting Integrated Into Family Business,” October 2009). It soon became evident that scores of other businesses in and around the San Antonio area, where the first composting facility was opened, shared equally challenging recycling demands. According to Rob Smith, general manager of the company’s Conroe site, New Earth today offers a full slate of products and services.
“Our company philosophy: ‘Pioneering waste solutions for future generations,’ really sets the tone for what we do,” says Smith. “We see the challenges that exist for disposing of green waste products, and have built a business around finding the best solutions possible to minimize their impact — today and down the road. We process a fairly sizeable volume of brush and tree waste to make that happen. In Conroe alone about 9,000 cubic yards (cy) of material get processed each week; the San Antonio location is almost three times the size of ours, so their volumes are obviously much larger, in the 25,000 cy/week range.”
Smith adds that, because New Earth’s customers have come to rely on the high quality nature of its products, both locations only accept clean debris for processing. “We don’t accept C&D wood waste, pallets or anything of that nature,” he explains. “We focus on only virgin material from area land clearing firms, landscapers, tree care services and so on. That has served us well.” New Earth products include a number of different sizes and colors of mulch, various bedding mixes, manure compost and other products that are sold in bulk, as well as 15 other products that it bags and palletizes.
Growing The Business
While the company’s San Antonio location has been accepting biosolids from local wastewater treatment facilities for about a decade, the Conroe site just began processing biosolids in the beginning of 2013, which it receives from several municipalities in the Houston area. Making that happen necessitated some major changes, including construction of a 16-inch-thick, 8-acre concrete pad and a 2.5-acre retention pond. A misting system, supplied by Piian Systems, was installed for odor control. Windrows are turned with a Backhus unit.
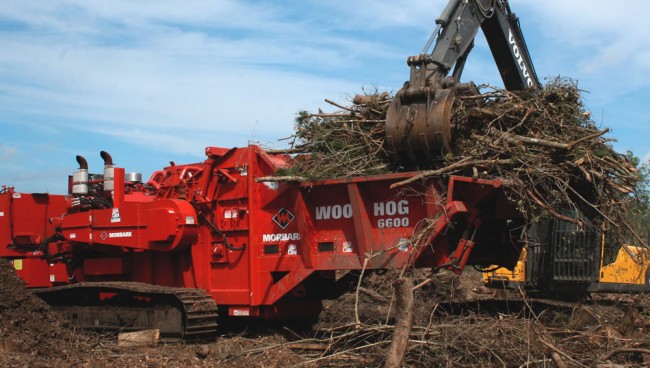
With last year’s drought and ban on burning, New Earth began doing off-site grinding. Its new Morbark horizontal grinder on tracks facilitates processing at other locations.
“The decision to go with a new mobile horizontal grinder was really based on a number of factors,” notes Smith. “For one, because of last year’s drought and ban on burning, we started doing some off-site grinding for land clearing firms — essentially going to their sites to grind the tops and undesirable timber. Our crews appreciated the fact that they can take the grinder to the material instead of vice versa. We had a smaller machine at the time, so we felt that, if we were to continue building that part of the business, a larger grinder would get us into and out of those jobs quickly, allowing us to get back here to support the main operation. Currently, such off-site work is only about 5 to 10 percent of our business, but we can see that growing. In addition, some of our bigger customers have grinding needs, so this fits that scenario as well. With that capability, we can become more of a solution provider than simply a vendor.”
He adds that although the new grinder burns more fuel than the older unit, those added costs are more than offset by the increase in productivity. “We are getting anywhere from double to triple the throughputs we were getting before — I’ll take that trade-off any time,” he says.
Screening And Bagging
New Earth has found that the Komptech star screen provides a much higher production rate than a traditional trommel, as well as enables screening of high moisture material. A PremiereTech AP Series High Level Palletizer, working in conjunction with the Conroe site’s bagging operation, rounds out New Earth’s process. In addition to ordering and stacking bags, each palletizer also tracks the number of pallets filled, units per minute, rejected bags and the total number of bags. “On average, we do about 90 to 100 pallets — roughly 5,400 to 6,000 bags — each day,” says Smith. “The system is so automated that we can run the entire bagging/palletizing operation with just two men.”
With the new biosolids composting operation coming on line in January, the Conroe operation essentially mirrors what is happening in San Antonio. “We are taking what they’ve learned at that location over the years — with regard to production, odor mitigation and so on — and putting it to practice here,” he adds. “Conversely, our owner, Clayton Leonard, is also taking what we’ve learned here, how we run our bagging operation, for example, and applying it to their operation.”
Larry Trojak is with Trojak Communications in Ham Lake, Minnesota.