Molly Farrell Tucker
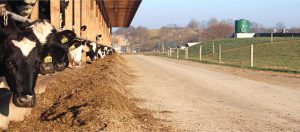
Reinford-Frymoyer Farm is a calf ranching business with 480 heifers and 30 dry cows. Photo by Brett Reinford
The benefits of an anaerobic digester installed at Reinford Farm in 2008, a dairy farm owned by Steve and Gina Reinford, inspired their son, Chad Reinford, to build a larger digester at his farm, the Reinford-Frymoyer Farm, down the road several years later. The digesters have greatly reduced both farms’ manure odors and energy costs, provided sources of revenue and improved the health of their herds.
Reinford Farm is located in Mifflintown in central Pennsylvania. The Reinfords purchased the farm in 1991, starting out with 57 dairy cows and 144 acres. Currently, there are 650 cows and 330 acres. Reinford Farm’s main dairy product is milk, which is sold to Land O’ Lakes.
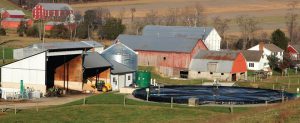
The complete mix anaerobic digester on Reinford-Frymoyer Farm manages about 210,000 gallons/month of manure, about 20,000 gallons/month of grease trap waste and about 110 tons/month of food waste. Photo by Brett Reinford
The Reinford’s oldest son Chad is the crops manager, middle son Brett is the office manager, and their youngest son Drew is the feed manager. Brett Reinford got his family interested in anaerobic digestion while taking an environmental studies class at Hesston College in 2005. “My professor challenged our class to be more environmentally friendly in our everyday life,” he explains. “I took this as a challenge for our farm and started doing research on different alternative energy sources that we could use. I decided that an anaerobic digester had way more benefits than wind and solar and it actually removes a harmful methane gas from the air — it would be a win for the environment and our farm.”
Reinford Farm hired Team Ag, Inc. of Ephrata, Pennsylvania to perform a $12,000 feasibility study in 2006. The Reinfords visited dairy farms in Washington State, just north of Seattle, that had installed anaerobic digesters, and attended a Dairy Summit, where they met representatives from RCM Digesters based in Berkeley, California. They hired RCM to design the digester; Team Ag Inc. provided the engineering services for the project.
Project Costs, Digester Operations
The first digester cost $1.1 million to build. RCM Digesters helped Reinford Farm apply for grants and financing, which included an Energy Harvest grant of $285,000 from the Pennsylvania Department of Environmental Protection; a U.S. Department of Agriculture (USDA) grant of $203,600; a $90,000 tax credit through the Resource Enhancement and Protection Tax Credit Program (REAP); $40,000 from the USDA Environmental Quality Incentives Program (EQIP); and a $135,000 loan through the Pennsylvania Department of Agriculture’s Machinery and Equipment Loan Fund (MELF). Remaining funds needed for the project were borrowed. Reinford Farm acted as the general contractor and hired a project manager to oversee construction, which started in August 2007.
The complete mix, mesophilic digester became operational in February 2008. It is a circular, heated, mostly below-ground tank with 526,000 gallons of capacity that is 80-feet in diameter and 16-feet deep. The digester is designed for 1,000 cows and currently receives manure from 620 cows of which 580 are milking and 40 are dry. The cows produce an average of 11,000 to 11,500 gallons/day of manure. “We are growing our herd from 650 cows to 800 cows by 2018,” says Brett Reinford. “We built a 300-cow freestall barn in January 2015 with plans to add onto the barn as our farm continues to grow.”
Skid loaders remove manure from the freestall barn and manure is scraped daily from the dry cow barn. All manure is loaded into a concrete holding tank, where gravity flow moves it through a 30-inch pipe to the influent tank that is 20-feet long by 20-feet wide by 12-feet deep. Each day, 11,000 gallons of manure are loaded into the digester. All milking parlor wastewater and copper sulfate footbath waste bypass the digester.
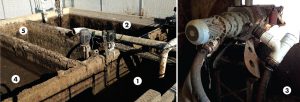
The four 10,000 gallon tanks (left) are utilized for different parts of the codigestion process: Influent tank mixes fresh scraped manure and ground produce waste, which is pumped into digester (1). Digested manure discharges into effluent tank (2). Manure is pumped to DODA solids separator (3). Liquid manure flows out of separator to tank (4). Liquid food waste and grease trap are stored in middle tank (5). Photos by Brett Reinford
The manure is mixed with expired produce and used coffee grounds from more than 30 Wal-Mart and Sam’s Clubs stores, as well as a few other grocery stores in north central Pennsylvania. Organix Recycling collects and delivers approximately 100 tons/week of food scraps; Reinford Farm receives a tipping fee for the material.
Three Houle mixers, each with two 10 hp motors, mix the contents of the digester. To help maintain the temperature at 101°F, recovered heat from the CHP unit is used to heat water that circulates through pipes inside the digester. Two inches of insulation cover the outside of the digester and four inches of insulation cover the top.
The complete mix digester is designed for a hydraulic retention time (HRT) of 21 to 24 days at 10 to 12 percent solids, and currently operates at about a 48-day HRT with about 14 percent solids. Biogas is produced and collected under the tank’s nonexpanding flexible cover made of a black, 60-mil-thick plastic material. Manure influent, effluent and digester temperatures are recorded daily from probes within the digester. Influent and effluent, manure total and volatile solids and nutrients are analyzed twice per year.
Digestate Management
The digested manure flows to an effluent storage pit measuring 20-feet long, 20-feet wide and 12-feet deep. A Houle 7.5 hp pump (with a Baldor Farm Duty motor) directs the effluent to the solids separation building. The solid/liquid separation room is above the separated solids storage bay. A DODA manure separator with a 10 hp motor is used. Digested solids fall directly into a storage bay. All are used as bedding for the cows.
The herd somatic cell count — an indicator of milk quality — has continuously declined since the farm began using the separated solids for bedding. Counts now range between 70,000 to 100,000, whereas previously, they were around 175,000 to 200,000. “This lowered count is beneficial because we get paid a premium for our milk and it makes our milk more marketable,” explains Reinford.
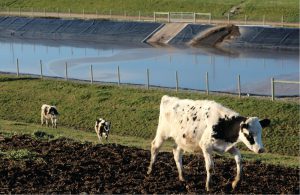
Digested liquid manure is pumped into a storage pond and is land applied on crop fields by both drag hose and tanker haul. Photo by Brett Reinford
The separated liquid stream gravity flows to a 2.5 million gallons storage pond. The effluent is land applied on the farm’s crop fields by both drag hose and tanker haul when needed and according to Reinford Farm’s nutrient management plan.
Biogas System
Biogas is piped underground through PVC pipe to the engine generator set, a reconditioned, 1,200 rpm Caterpillar G342 engine coupled to a 220 volt, AC, 60hertz, single phase 130 kW generator purchased from Martin Machinery Inc. The combined heat and power (CHP) unit runs continuously, except during maintenance. A hydrogen sulfide removal system pretreats the biogas before it enters the engine. Biogas production measured on the Fox Thermal Instrument gas meter averages 50,000 to 60,000 ft3/day. An auto flare burns any excess biogas not consumed by the biogas engine set.
A Bacharach Fyrite® Gas Analyzer is used to manually measure the CO2 concentration in the biogas, which is typically 36 percent. The calculated methane concentration is 64 percent. The hydrogen sulfide content in the untreated biogas measures in the range of 2,500 ppm.
Heat recovered from the engine also heats water for the milking parlor and a calf milk pasteurizer, as well as domestic water. “We do not buy any fuel oil,” notes Reinford. “All the heat that our farm and farmhouse needs is produced by our CHP engine. We have an oil furnace in the house as a backup in case anything would happen to the digester.” The hot water also is used as radiant heat in the floors of the work shed and office. A grain bin installed in November 2008 uses waste heat from the radiator of the engine to dry grain.
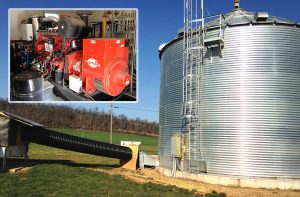
Reinford-Frymoyer Farm installed a Guascor engine (inset) that can produce up to 225 kWh. Excess heat from the engine heats the farmhouse and is used to custom-dry corn in the farm’s 10,000 bushel drying bin (black heat pipe above). Photos by Brett Reinford
“Using the heat from the CHP unit to heat the farmhouse saves us about $500/month on heating costs and $2,000/month on our farmhouse and farm’s electric costs,” he adds. Reinford Farm also receives about $500/month for its Renewable Energy Certificates (RECs), which it sells to 3Degrees, an environmental attribute broker.
The farm has a power purchase agreement (PPA) with Pennsylvania Power & Light (PPL) to sell all of the electricity produced through the digester to the utility. Daily power production averages 140 kWh. “We net meter our electricity and usually get paid six to ten cents per kWh,” says Reinford.
The Pennsylvania Public Utility Commission has been considering lowering the cap on the amount of electricity that PPL can purchase from farm digesters. “This is a really important issue that we are still working on,” he adds. “As of right now, there is a proposal for the cap to be at 200 percent. This would mean that half of the electricity produced on our farm could not be sold to the grid — making our digester as well as most other digesters in Pennsylvania economically unfeasible. We are still working to get legislation passed that does not put a cap on how much electricity farmers with digesters can produce.”
Second Generation, Second Digester
Chad Reinford owns Reinford-Frymoyer Farm LLC, a calf ranching business located three miles from his parents’ farm. He has 510 animals, including 480 heifers, and 30 dry cows from Reinford Farm. “The plan is to always keep the heifers on my farm and also some dry cows when my dad needs a place to house them,” says Chad Reinford. “The heifers and cows are managed by employees from my parents’ farm.”
He is the crop manager for both farms. “We crop a total of about 1,200 acres on the two farms, including about 1,000 acres of corn and about 200 acres of hay,” he adds. “We also double-crop our corn acres with triticale and rye in the fall.”
Construction on the Reinford-Frymoyer Farm complete mix digester (also from RCM) started in December 2011; it became operational about a year later. The digester is 96 feet in diameter and 16 feet deep, compared to the Reinford Farm’s digester that is 80 feet in diameter and 16-feet deep. “Although my digester is not double the size, it can produce about twice as much electricity,” explains Chad Reinford. “The major difference is my digester has a Guascor engine and can produce up to 225 kWh. The other farm has a 140 kWh Cat engine.”
About 80 percent of the Reinford-Frymoyer Farm’s digester costs were covered by grants, including a USDA grant of $377,720 in 2011 and a Section 1603 award from the U.S. Treasury Department for $427,000 in March 2014. Total cost of the digester was $1.4 million, which Chad Reinford expects will be recouped in four to five years.
About 210,000 gallons/month of manure are produced on his farm. About 20,000 gallons/month of grease trap waste and about 110 tons/month of food waste are codigested with the manure. Manure solids are separated from the liquid after digestion. The older heifers and dry cows are bedded with manure solids. The younger heifers are housed on a slatted floor barn, so no bedding is needed. Extra digested solids are sold to local farmers for bedding.
Excess heat from the biogas engine is used to heat the farmhouse and to custom-dry corn in the farm’s 10,000 bushel drying bin. “Most farmers that need to dry their shelled corn take it to a corn elevator or mill to have it dried,” explains Brett Reinford. “Most grain driers use propane to dry the corn to below 15 percent moisture. Chad does the same thing, but uses the heat from the engine to dry the corn. He doesn’t raise any of his own corn, so he is able to dry corn for other farmers. Chad probably saves around $500/month by not having to buy propane or fuel oil.”
Reinford-Frymoyer Farm also has a PPA with PPL. Daily power production averages 150 kWh/hour or about 3600 kWh per day. Chad Reinford sells his farm’s RECs to 3Degrees as well. “I am happy with the design of my digester,” concludes Chad Reinford. “We were able to learn from some of the issues we were having from the first one, and corrected them on the one I built. The only design change I made was to install a ram pump that feeds my digester, and not a chop pump. The chop pump kept clogging, so I ended up purchasing a GEA ram pump.”
Molly Farrell Tucker is a Contributing Writer to BioCycle.