Top: Overview of Brady Trucking’s yard and food waste composting facility. Photos courtesy of Brady Trucking
Nora Goldstein
Brady Trucking Company in Shelton, Washington, has run a successful mulch production facility and trucking company for decades. It was started by Jeff and Nancy Brady in 1982, hauling bark, wood chips and sawdust in Washington and Oregon. Raw bark is purchased from mills and hauled to Brady Trucking’s manufacturing facility where it is processed into finished landscaping products. “For years we’ve been purchasing compost in bulk to have availability for our mulch clients who also need compost,” explains Evan Brady, who along with his wife Ashley, now own the business his parents started. “We did some small-scale composting of green waste in windrows, but it wasn’t organized. We recognized an opportunity to compost green waste more intentionally on a commercial scale, but the primary source of green waste is what is being collected curbside with food waste in communities in nearby Thurston and Pierce counties. In addition, Washington State’s law that mandates food scraps collection, effective in a few years, also was a driver in our decision.”
Their 15-acre bark and mulch facility in Shelton was able to accommodate a composting operation. Because the area receives about 70 inches a year of rainfall, the Bradys knew much of the new facility would need to be under cover to avoid having to manage high volumes of leachate along with storm water. “We investigated our options, looked closely at the numbers and conceptual operating plans, and decided to move forward with a Green Mountain Technologies covered aerated static pile system (cASP),” says Brady. “GMT outlined the steps we had to take to get the facility permitted by the Washington Department of Ecology (WA DOE) as well as Mason County Public Health (MCPH). We wanted to get the permit fairly quickly, and GMT assisted us with the process.”
Design And Permitting
The composting facility is designed and permitted to process 50,000 tons/year, of which 10% can be food waste. Its current constructed peak capacity of 30,000 tons/year allows time to optimize the process before expanding. With GMT’s assistance, the permitting process took under a year. “To get started, we needed to develop the facility design concepts and to identify key regulators and stakeholders at the state and local level whom we needed to meet with to identify and clarify key issues,” explains Rik Langendoen, a Senior Environmental Consultant at GMT. “Next, we took action to address the issues/gaps as effectively as possible in a timely manner. A pre-application onsite meeting was held with WA DOE and Mason County Public Health (MCPH). Meetings also were held with Mason County Commissioners, and we communicated with the local tribe to keep the leaders apprised of our plans. It was important to leave room for the regulators to contribute to the design.”
Open walled active composting pad and Green Mountain Technologies aeration system. Video courtesy of GMT
Another key step, says Langendoen, was to hire an odor consultant/modeler to investigate and assess potential local impacts. Air quality is regulated by the Olympic Region Clean Air Agency (ORCAA). “The consultant and the odor modeling that was conducted were critical to the permitting success, facilitating the regulators’ more expedited decision-making process,” he adds. “The design includes having a biofilter layer of wood mulch on the top of the active composting piles to treat odors. ORCAA was satisfied with that method of control. Brady Trucking was allowed to begin construction before final composting and air permits were issued.”
Facility Operations
The new composting facility opened in May 2023. Currently, about 5% of incoming feedstocks are food scraps, primarily from the residential sector. All household food scraps are accepted, but no food-soiled packaging or certified compostable products are allowed — primarily to mitigate the potential for contamination. The facility receives regular inquiries from commercial generators about taking their food waste; some also would need the material to be collected. “We are getting asked about hauling food waste from their facilities in roll-off bins but we are not set up for that,” notes Brady. “We are talking with a local collection company to provide that service and will consider it as opportunities arise. Right now, food waste from the commercial sector is accepted on an “as approved” basis.
Brady Trucking has two retail sites where it receives and grinds green waste dropped off by the public. About 20,000 tons/year are brought to these sites from neighboring Thurston County. After grinding, it is brought to Brady’s mulch and composting facility. Loads that contain food waste are hauled directly to the composting site, where they are mixed and ground. These feedstocks are incorporated into an active composting pile the same day they are received.
Active composting is done in aerated static piles (ASP) inside the open-sided building for 30 days, followed by 30 days of curing on a pad outside of the structure. Aeration pipes are built into the concrete floor of the building. “Half of the covered building is set up as the primary phase of active composting,” notes Brady. “The other half is the secondary phase. After two weeks in the primary phase, the material is mixed and water is added if necessary. About 1,000 cubic yards of compost are moved to curing from the secondary pile to make room for the material being moved from the primary phase.”
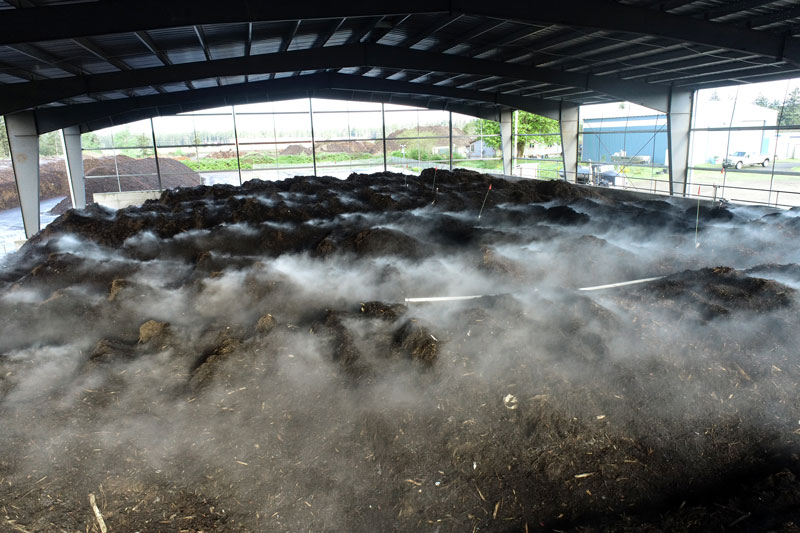
Active composting piles are inside a covered structure and aerated in a positive mode. Piles are covered with a layer of wood mulch that serves as a biofilter.
Moisture content is adjusted as needed before material is added to an active ASP with a bucket loader. Wood chips can be mixed in if it gets too wet. Leachate can be used to add moisture prior to meeting pathogen and vector control requirements. Once a pile has met those requirements, water is used instead of leachate to add moisture as needed. Piles are aerated in a positive mode; mulch is layered on top of the piles to serve as a biofilter.
Brady Trucking served as the general contractor and did the utility work, which provided significant savings. GMT’s WebMacs computer-controlled aeration system optimizes temperatures across multiple zones to manage the composting process and keep pile temperatures at the optimum levels. “The interface is user-friendly and is accessible via our phones so the process can be monitored constantly,” explains Brady. “Now that I’m getting more composting experience under my belt, we know that if the pile takes a long time to heat up that our recipe needs adjusting, or moisture should be added. We would panic at first but over the last year, we’ve got it dialed in.”
Brady Trucking uses a trommel screen to size the finished compost and a vibrating deck screen to blend compost and soils. Almost all the compost and blends are sold in bulk. The company’s two retail outlets sell compost, blends, bark, and gravel. Its primary customers, however, are other retailers that buy screened compost and bark products wholesale from Brady Trucking.
Looking down the road to 2027 when Washington State jurisdictions in urbanized areas will be required to provide residential food scraps collection, Brady believes they are in a good position to be a processing solution in the region. “We would like to be, as much as our system will be able to keep up with demand,” he says. “It is important that municipalities do a good job with program implementation to keep the organics stream clean, and to make sure it stays that way.”