Top: Mixing of wet waste and browns (center), compost curing in crates (background).
Sandya Narayanan
Bangalore, located in southern India, is one of the fastest growing cities in the world. In the past two decades, it has seen a massive shift in the city landscape from bungalows with gardens into a global city with high rises and large residential complexes, tech parks and corporate campuses that are self-contained, providing all the in-house amenities and facilities. Not surprisingly the city’s infrastructure has not been able to keep pace with this meteoric expansion of population, the volume of vehicles on the roads, and the waste generated.
The municipal system responsible for managing solid waste was not able to do much beyond collection, transporting and dumping the mixed waste in so called landfills — essentially large tracts of land in the outskirts of the city with none of the measures required in a standard landfill (e.g., liners). This led to rampant unregulated pollution with leachate from the landfill dumps destroying all the surrounding water tables within a radius of three miles, causing an uproar and widespread protests from surrounding villages. Regulatory authorities and the courts — in response to litigation filed by civil society organizations — shut down the landfills in 2012. In response, the municipal laws were modified, mandating three way segregation into trash, recyclables and organics by all citizens and defining large apartment complexes, commercial organizations and campuses as bulk generators that are responsible for managing the waste generated. This requirement applies to multi-dwelling housing with >100 units or total developed area >53,820 square feet. Organic waste must be managed within the bulk generators’ premises to reduce the pressure of waste to landfills.
It is estimated that Bangalore generates about 6,700 tons/day of waste; bulk generator waste is about 1,650 tons of that total. The dry waste fraction is about 990 tons/day, which is collected by 170 neighborhood dry waste recovery centers that sort collected materials. Dry waste with market value is sold. The nonrecyclable fraction is either landfilled or co-processed with other wastes.
In Situ Organics Management Origins
In 2007, a small group of people, who later formed the Solid Waste Management Round Table (SWMRT), started experimenting with utilizing private service providers to offer doorstep service to apartment complexes to collect their dry waste weekly and the sanitary waste (e.g., soiled diapers, hygiene products, household hazardous wastes) daily. This left only the organic fraction (kitchen and garden waste) to manage. SWMRT took advantage of the already existing regulatory framework making it incumbent on the builders to provide waste management facilities in-house — primarily to provide solutions for organic waste management. Experiments started in a few willing apartment complexes with different composting solutions. In new apartments, services were provided by the builders but in the older apartments residents had to set up their own composting solutions. There was a lot of learning on what did and did not work. Valuable lessons also were learned about how segregation needed to be carried out by the individual residents and nature and frequency of collection by the housekeeping staff.
From 2007 to 2012, practices were standardized, with clear directions on the requirements for residents and the housekeeping staff. This standardized practice was tested at apartment complexes by size: small (<300 units), medium (300 to 800 units), and large (>800 units and typically up to 1,200 units). SWMRT played a crucial, catalyzing role in this entire process of testing, monitoring, evaluating and documenting the practices, while working closely with the apartment management committees. It served as the bridge between the apartments and the services and solution providers, and promoted and publicized new successes through citizen networks, print media and the just emerging social media platforms.
The upheaval caused by the landfill closures in 2012 created an opportunity for the SWMRT to present the new practices that were gaining ground at the apartment complexes. It provided reassurance to the municipality that the approach to managing bulk generators’ organics was feasible and in situ solutions were available, even though capacity building of the services would be necessary.
Case Studies
Brigade Regency
In 2007, the Brigade Regency, a small apartment complex with 63 units, was the first to voluntarily set up a composting process on the premises, though it was not required by law. About 58 units started waste segregation. Collected organics are processed in a unique aerobic digester tank built out of brick and mortar and equipped with a 0.5 hp blower to ensure air flow. The tanks are covered by perforated sheets to deter rodents and retain heat. The lids have charcoal on the top to filter odors. About 77 lbs/day of vegetative food scraps and dairy are added using a layering system; no mechanical shredding is used. The campus has a surfeit of dry leaves which are liberally added for carbon. Collection is done by the housekeeping staff and the layering and harvesting of finished compost is done by the gardeners. Security staff control aeration frequency and are required to run the blower system for about 30 minutes each day. Compost is used in the apartment complex’s garden.
The system is a low cost set up that is affordable for a small apartment complex. Operations, which don’t involve much turning or handling of materials, are supervised by the residents themselves, one of whom is a member of SWMRT. It has been running successfully to date. Occasionally composting is discontinued to do maintenance work, which includes repainting, replacing of blower pipes, etc. The apartment complex recovers about 350 lbs/month of dry waste. About 1.3 tons/month of wet waste are composted and diverted from landfill.
Purva Venezia
Purva Venezia, in the Yelahanka zone in Bangalore, is an example of a large apartment complex (about 1,330 units) adoption of in situ management of organics that has been sustained for over a decade — despite challenges related to changing management committees, the highs and lows of space and resource management, and changing technologies. It started segregating waste in 2013 into about seven streams including wet, dry, rejects, electronic, garden wastes and reusable items. The dry waste and other streams are picked up by various service agencies that either recycle or dispose of the materials.
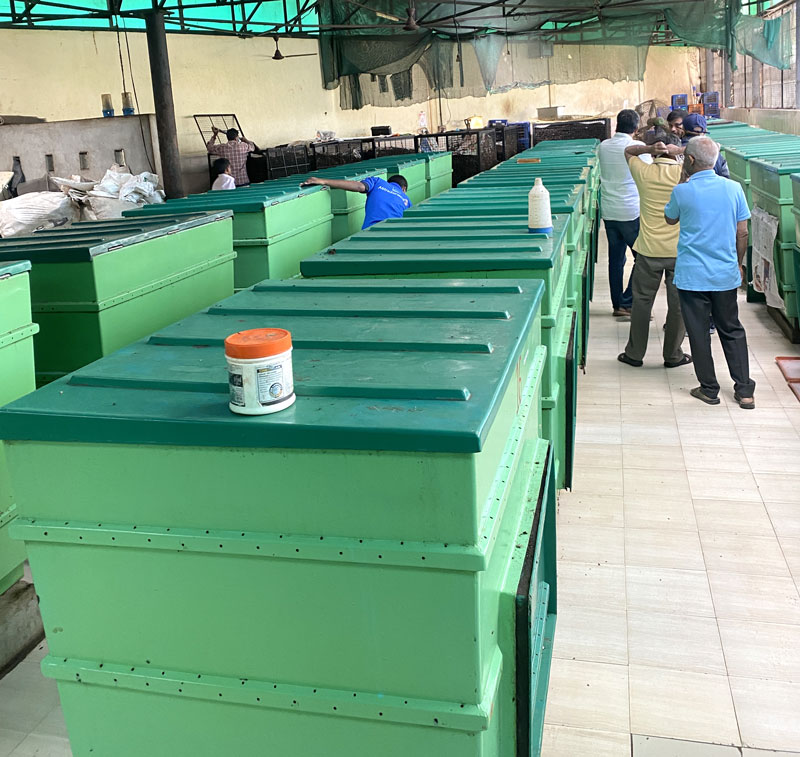
Fiberglass reinforced plastic composting bins are in a centralized shed. Meat, fish, dairy and vegetative material are processed. Photos courtesy of Sandya Narayanan
The wet waste, inclusive of meat, fish, dairy and vegetative material, is managed in situ in a closed fiberglass reinforced plastic compost bin system comprised of 29 composters housed in a centralized shed on the premises. Each composter — 3.4-feet long, 3.5-feet wide and 4-feet high — processes 66 to 110 lbs/day. Collected wet waste is first emptied and spread out to remove plastic contamination then is chopped manually before being mixed with cocopeat, microbial accelerators, finished compost and dry leaves and fed to the shredder. Meat, fish and dairy can be included because materials are shredded prior to composting.
A single batch takes about 30 to 40 days to compost. About 1,540 lbs to 1,760 lbs are managed daily. Finished compost is used in the community garden and landscaping, given to friends and families, and/or sold to farmers at minimal cost. Daily operations are managed by a composting committee comprised of residents. Door-to-door wet waste collection is carried out by a housekeeping team of 50 people of which about 6 people are engaged in the sorting and composting. The apartment manages about 13 tons of dry waste and about 26.5 tons of wet waste a month. Around 42 tons of waste are diverted from the landfill every month.
Shobha Dahlia
Not all apartment buildings have smoothly functioning composting systems, including Shobha Dahlia (about 236 units), located in Bellandur in Bangalore. This case study explains the struggles of composting, which were successfully addressed by guidance and troubleshooting support offered by SWMRT. It illustrates the value of specialists who can assist and reverse failures and problems, such as odors and flies, that can develop while composting. These are typically avoidable when following best practices and the support helps ensure that communities don’t give up on the process.
Shobha Dahlia managers reached out to SWMRT when facing a fly infestation in the composting area. They have been composting for the last nine years using a shredder, mechanical mixer and composting in either crates or tanks. More recently, larger capacity closed mesh bins were acquired and complete active composting in 8 to 10 days. The composting system was observed and changes made, such as the addition of dry leaves when layering material into the bins. Some bins were overfilled resulting in the formation of maggots. Additional mesh bins were added to increase composting capacity; partially composted material was moved from the crate system into the mesh bins. This step was met with partial success in getting rid of the flies and after two months of constant monitoring, the final breakthrough came with the use of lemon grass oil in the composting area. The fly infestation problem was resolved and the apartment resident team was confident enough to continue the composting system.
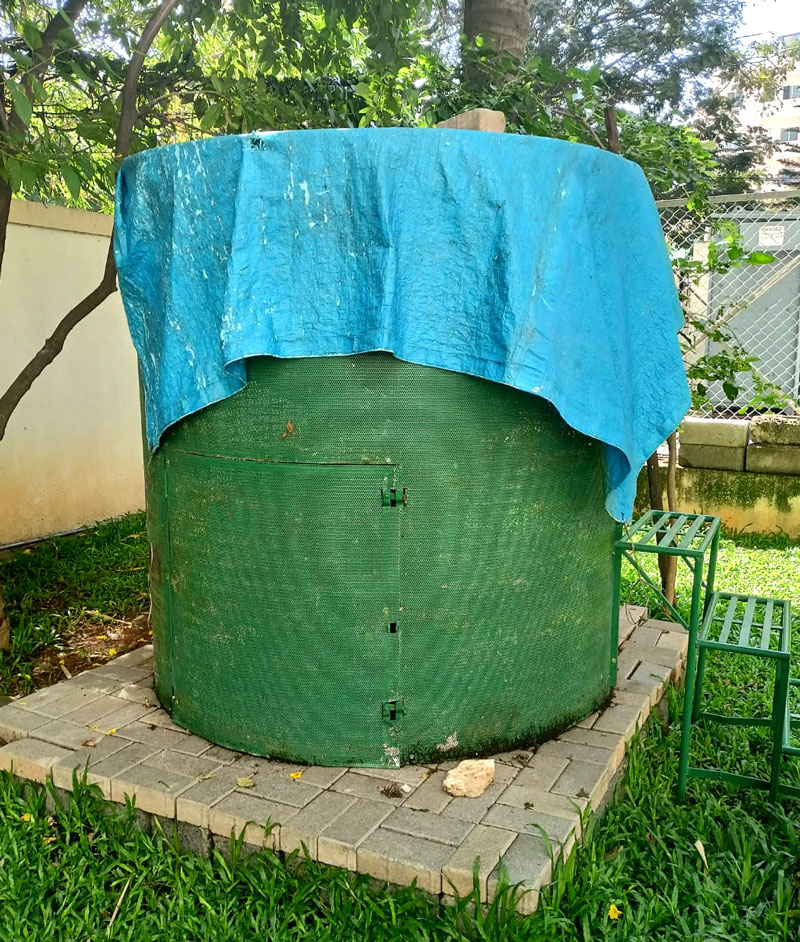
Mesh bin composters were installed to increase composting capacity at Shobha Dahlia apartment complex.
During this time the resident champions had to ward off naysayers who were resisting the composting process. It was their determination to find a solution, with the help of specialists, that led to preventing derailment of a composting process which had been in place for close to a decade. This apartment complex’s composting system processes about 500 lbs/day and diverts about 7.7 tons of wet waste from the landfill a month.
Resilience And Commitment
All three case studies illustrate the resilience and commitment of the residents as either champions or managing committee members. They also highlight the unique approaches to wet waste management, along with the challenges and how they have been overcome. The key lesson drawn from Bangalore’s experience is the critical role these resident champions — along with guidance and mentoring from practitioner organizations — have played in ensuring that the in situ composting systems continue while staying compliant to government policies.
It has been about 15 years since the experiment with redefining how waste is managed by bulk generators in Bangalore started. The critical need was to ensure that the bulk generators manage their waste independently with access to private (non-municipal) service providers for some streams of waste and more importantly handle their organic waste in situ. The first notification by the municipality to bulk generators in 2012 was followed by adoption of municipal by-laws in 2020 recognizing bulk generators and their roles in managing their waste. Most recently, Bangalore issued a notification in 2024 requiring bulk generators to submit a self-declaration on processes being followed, so that the City can confidently conclude that the generators are in compliance with its mandate for in situ waste management.
The existence of the mandate means that the developers of these bulk generator apartments, tech parks and mixed use complexes have to provide the necessary infrastructure for organic waste management, much like they would provide other facilities like swimming pools or gyms. This takes away the need for any financial subsidies to be given by the municipality or government for setting up composting facilities. The role of practitioner organizations like SWMRT and social entrepreneurs who have stayed committed to ensure the success of decentralized waste management through in situ processing has also been one of the key reasons for the continued success and adoption.
Sandya Narayanan worked as a finance professional for close to two decades and has been working as a member of Solid Waste Management Round Table (SWMRT) — a collective of solid waste management practitioners in Bangalore — for over 13 years . She is an analyst and expert on the economy of waste.