Increasing its feedstock volume with paper currency manufacturing waste brought challenges — and new opportunities.
Marsha Johnston
BioCycle February 2017
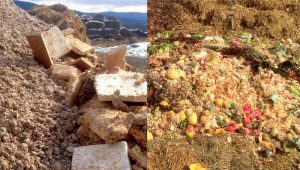
TAM Organics receives short cotton fiber from Crane Currency, which it blends with a dry feedstock from Ecovative Design (left, in chunks next to pile) and commercial food waste (above).
TAM Organics has been composting source separated organics, including commercial food waste, in Bennington, Vermont since 2013. The company is a division of TAM Waste Management, Inc., which Trevor Mance founded as TAM Inc. in 1996 while he was in high school. TAM Waste Management provides waste hauling and recycling services, in addition to composting.
Permitted to process 40,000 cubic yards (cy)/year but only composting 26,000 cy/year, the company was looking for more feedstock sources. It landed on short cotton fiber and flax waste from Crane Currency, based in Dalton, Massachusetts, which has printed U.S. currency for over 200 years. “We started receiving the material in May 2016,” notes Mance. “As a result, we anticipate processing about 38,000 cy in total in 2017. That includes all of the feedstocks we compost.” He adds that Crane Currency was already diverting its organics to composting and changed to TAM for the service.
TAM’s compost became certified for use on organic farms in March 2016, but contamination from the food waste stream has been a challenge to meeting the certification’s compost quality requirements. The currency printing waste cannot be included in TAM’s certified organic compost, so Matthew Proft, TAM’s Organics Coordinator, decided to compost that stream with the food waste, eliminating the contamination entirely from its certified product. “Our organic compost is made from manures, leaves and bedding material,” explains Proft. “We are using compost made with the food and currency wastes in our topsoil mix that is used for lawn reclamation and landscaping. We did some trials with this [Crane] material and some other paper by-products a couple of years ago, and have used it on demolition sites to put in some really nice lawns.”
The company receives food waste from 35 to 40 generators, including area supermarkets. This stream will only continue to grow as Vermont’s organics ban, Act 148, applies to more entities each year. In 2017, generators of 18 tons/year (one-third ton/week) of food waste must divert material to any certified facility within 20 miles of the generator.
Proft works constantly with customers to reduce contamination, using his smart phone camera and a quick email the same day he receives any contaminated food scraps as educational tools. “By and large, they are eager to make adjustments,” he notes.
Managing Feedstock Moisture
TAM Organics’ 7-acre parcel in Shaftsbury includes a concrete mixing pad, and a gravel bed with PVC pipe for aerated static piles. After 2 to 3 weeks under aeration, piles are moved to windrows for curing. The aerated piles and windrows are both about 8 to 10 feet tall and 16 to 20 feet long. TAM uses two John Deere loaders for mixing, turning and loading material, and a dump truck for creating windrows. Throughput, from receiving material to salable compost, is at least 12 months.
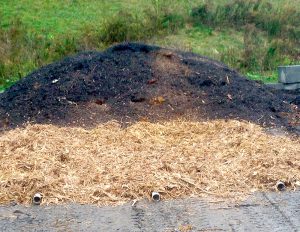
After blending, material is placed in aerated static piles on a gravel bed with PVC pipe. It remains under aeration for 2 to 3 weeks, before being put into windrows for curing.
Mixing food and currency printing waste made logical sense, but posed operational challenges. First, Proft had to adjust the composting recipe to break down the cotton fibers. “I tell people to envision putting a dollarin one jeans pocket and a pad of paper in the other when you wash them,” he says. “The dollar just comes out cleaner, and the paper is in a wad. The lignin in the cotton is a bit more resistant to breakdown, so we’ve had to adjust our recipe to make a mix that will go after the cotton fiber a little more aggressively.”
The bigger challenge is the high moisture content in the Crane waste. “The material we’re getting is anywhere from 50 to 75 percent moisture, in some cases,” explains Proft. “It’s more on the wet side than the drier side, but we have no control over that.” And mixing food waste with it adds another feedstock with fairly high moisture content. To manage excess moisture TAM uses “a fair amount” of dry matter, including a sterile, organic stream from Ecovative Design, which grows a mushroom-inoculated alternative to Styrofoam using corn stubble, flax and straw. “They have a lot of material that comes in here very dry,” says Proft. “Some is large chunks of the test pieces of the foam, but a lot is the ground-up product before it is put into molds.”
A recipe using a 2:1 wet-to-dry ratio worked well through the summer and into October but winter conditions make it difficult to reduce the initial 68 to 75 percent moisture content. As a result, Proft has increased to a 1:1 ratio of dry and wet feedstocks. The extra time and material it takes to produce compost during the winter months also makes the finished product more expensive.
Finished compost is screened two or three times using a Rawson Manufacturing Model 633 half-inch trommel screen. TAM Organics sells it only in bulk, primarily at its yard, in quantities as small as 5 gallons up to a dump truck load.
Marsha W. Johnston, an editor with Earth Steward Associates, is a Contributing Editor to BioCycle.