Marsha Johnston
In September 2014, the U.S. Environmental Protection Agency’s Office of Research and Development released a report, “Food Waste to Energy: How Six Water Resource Recovery Facilities (WRRFs) are Boosting Biogas Production and the Bottom Line.” The report details the codigestion project development and practices of six WRRFs. Five of the six WRRFs participated in a March 2015 EPA webinar, sharing their experiences with improving energy efficiency and implementing or expanding codigestion.
Part I of this article series (“Boosting Biogas And The Bottom Line At WRRFs,” June 2015) profiled two of the five facilities on the webinar — Central Marin Sanitation Agency in San Rafael, California (CA) and East Bay Municipal Utility District in Oakland, CA. This article profiles the Hill Canyon Wastewater Treatment Plant in Thousand Oaks, CA (HCTP), the West Lafayette Wastewater Treatment Utility (WLWTU) in West Lafayette, Indiana and the Sheboygan Regional Wastewater Treatment Facility (SRWTF) in Sheboygan, Wisconsin.
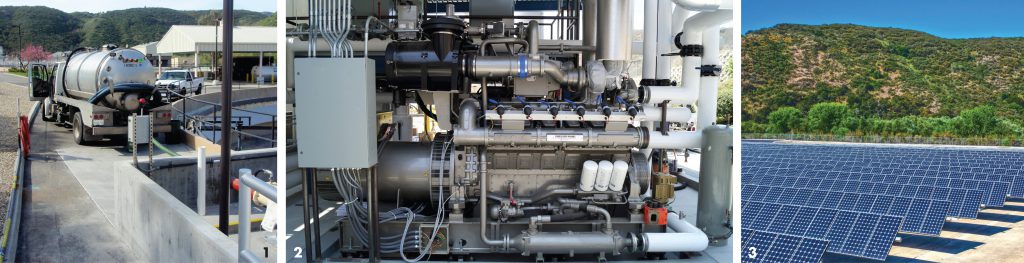
The Hill Canyon Wastewater Treatment Plant in Thousand Oaks, California receives 10,000 to 30,000 gallons/day of high strength organics (1). The plant has two biogas cogeneration engines (2) and a 500 kW solar array (3). Photos courtesy of Hill Canyon WWTP
Hill Canyon Wastewater Treatment
HCTP’s 14-million gallons/day (mgd) advanced tertiary facility provides wastewater treatment for 90 percent of the 128,000 residents of Thousand Oaks (CA) treating an average daily flow of 8.5 mgd during the current drought. The digester design capacity is 2.8 million gallons. Biogas produced from digested solids and food waste fuels two Mann biogas engines (295 kW and 630 kW).
Chuck Rogers, Plant Superintendent, began HCTP’s foray into renewable energy generation in 2007 with 500 kW of biogas cogeneration and 500 kW of solar. The wastewater treatment facility works with CHP Clean Energy, which owns and operates the renewable energy equipment, and through a power purchase agreement (PPA), sells the electricity back to HCTP at rates typically lower than utility retail rates. Heat recovered from the CHP units is utilized for digester heating. ”CHP Clean Energy is an expert on cogeneration engines,” Rogers explains. “The company had to sign a contract with HCTP guaranteeing output, it has to pay for everything and get all the permits, and it gets a fair return on investment, and so does our City.”
With the PPA, HCTP pays 7.2 cents per kWh for cogeneration, or about half the current rate from Southern California Edison (SCE); its contract with CHP Clean Energy has 2 percent annual increases. “With the renewable mandate for California, I can’t imagine that the utility will be limited to 2 percent increases,” Rogers adds. “Each year, the gap between what we would be paying the utility and what we pay for self-generation keeps getting better.” HCTP now has 900 kW of cogeneration along with the 500 kW of solar.
After committing to the Oak Park City Council to work towards taking HCTP off the SCE grid, Rogers realized that even with more conservation and optimization, getting to 100 percent self-generation would require greater volumes of high strength organics to generate more biogas. The utility used a $400,000 American Recovery and Reinvestment Act grant and an estimated $400,000 of city money to construct a new receiving station for FOG (fats, oils, grease) and other biogas-producing loads. The receiving station included a rock trap, tank, mixing pumps, and a metering pump for the digesters. A simple odor control system was added after the fact. As the staff’s knowledge has evolved over the years, HCTP modified the system to add, for example, a much larger rock trap and manual bar screen in front of the FOG pumps. Rogers notes that HCTP will soon further automate the process by installing an automatic bar screen that will discharge trash from the FOG into a dumpster to be hauled off.
After securing local FOG contract and experiencing its wildly variable BTU value, Rogers devised a computer program to manage it. “It basically does a compound loop with our digester so that we can set a number and, surprisingly enough, it works,” he explains. “You look at how the gas is being produced, feed a bunch of information into the PLC (Programmable Logic Controller) and lo and behold you’re not spiking all the time.” Avoiding gas spikes avoids having to flare it off, he added.
Although Rogers maintains that FOG is valuable, he says WRRF managers need to recognize that it has the potential for tremendous odors and contamination. It also has a very low pH level that eats up pipes and pumps unless they are stainless steel.
Today, HCTP averages between 10,000 to 30,000 gallons/day of high strength organics, comprised of different feedstocks that over the years have included FOG, biodiesel residuals, beer and coffee waste, and yogurt. Lately, says Rogers, they are getting salad dressing, which “smells nice and has great gas production.”
The facility makes approximately $500,000/year from tipping fees and $600,000 from sale of reclaimed water. Despite being 100 percent energy self-sufficient, HCTP continues to adhere to the City Council’s 2 percent annual energy use reduction goal. “We routinely meet and beat that, with 4 and 5 percent reductions each year,” Rogers says.
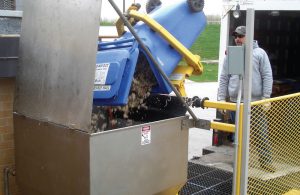
The West Lafayette (Indiana) Wastewater Treatment Utility installed a receiving station with a platform, integrated cart tipper (left) and a JWC Environmental Macho Monster grinder to handle preconsumer food scraps such as melon rinds and banana peels. Photo courtesy of West Lafayette WTU
West Lafayette Wastewater Treatment Utility
The smallest of the spotlighted WRRFs in the EPA report is West Lafayette’s activated sludge facility that treats an average daily flow of 7.8 mgd, and has the capacity to treat 10.5 MGD. The WLWTU serves West Lafayette’s 29,000 residents and nearby Purdue University. Its original codigestion project was designed around adding a FOG receiving station and upgrading its digesters to allow the plant to digest FOG. The FOG receiving station was comprised of a repurposed pumping station, a 20,000-gallon grit tank and a truck scale. The digesters were upgraded with new lids, mixing pumps, control equipment and new housing. While the preliminary engineering report estimated the plant would get 3,000 gallons/day of FOG from grease haulers, that volume was never attained, notes Dave Henderson, WLWTU’s manager. “Deliveries have steadily decreased over the years, as they find other outlets, providing competition for us.”
Seeking other sources of grease, West Lafayette launched a free residential service called “Save Your Pipes, Save the Earth,” which it marketed at farmers markets, city hall, and recycling centers. Customers are provided a one-gallon bottle container that they drop off at recycling centers. But the residential FOG contribution was not sufficient to fill West Lafayette’s digester capacity, so Henderson began looking for another fuel source: food waste. Reading the Purdue student newspaper, Henderson learned that food waste from its five dining facilities was no longer going to a composting operation but to a landfill. He called the university sustainability director, and visited the food service facility, where the food waste was going through a macerator, Hobart pulper, and classifier, and into 35-gallon totes. “All of the infrastructure set up for the composting project was still in place, and staff were still separating and processing the food waste,” says Henderson. “The waste was like cole slaw, or ‘baby food’ for digesters.”
In May 2009, WLWTU established a pilot program with Purdue, collecting the totes and emptying them into its FOG receiving tank. “The results were impressive,” he adds. “We were just starting up the digesters after a retrofit for the larger project, which included the FOG. The digesters came up to normal operating parameters probably faster than the engineers had expected.”
Bolstered by initial success, West Lafayette designed a more permanent station with a platform, integrated cart tipper and a JWC Environmental Macho Monster grinder to handle preconsumer food scraps such as melon rinds and banana peels. The upgrade cost less than $100,000, and was paid out of WLWTU’s improvement fund.
Today, its two mesophilic anaerobic digesters, with a combined capacity of 1.0 million gallons, are getting 1 to 2 tons/day of food scraps from Purdue University’s 5 dining courts, Purdue Agricultural Research and the local Food Finders Food Bank. Henderson notes that although source separation at the dining courts is “pretty good,” staffing changes every semester mean that some of the institutional knowledge inevitably isn’t transferred to incoming staff. “We have tours at the facility periodically so they know why it’s important to keep plastic knives and rubber gloves out of the waste stream,” he says.
Two 65 kW Capstone turbines are generating 20 percent of WLWTU’s electricity needs, or approximately 679 MWh per year. “We have a lot of room to advance,” he adds. “It got us thinking about the potential from food waste throughout the community. Our municipal solid waste department picks up 25 to 30 tons/day of MSW, which is maybe 18 percent food waste, so 4.5 to 5.4 tons/day.” Diverting those organics, however, would require WLWTU establishing its own collection program, providing the organic waste containers, personnel and other equipment to collect it.
In the meantime, some improvements have been made to the codigestion system — adding a PHI pulsed-air mixing system to better mix grease and food waste, a heavy object trap to the FOG inlet and improved screening ahead of the pumps. On his future wish list, Henderson says, is a separate dedicated receiving tank for food waste and a third microturbine.
Sheboygan Regional Wastewater Treatment Facility
The SRWTF began its codigestion program in 2005, and is currently receiving 60,000 gallons/day of high strength organics, producing 500,000 cubic feet/day of biogas. In 2013, the facility received an Engineering Excellence Grand Award for Net Zero Energy from the American Council of Engineering Companies. BioCycle has reported on codigestion at SRWTF over the years (see “High Strength Wastes Boost Biogas Production,” March 2009 and “Microturbines Fill Biogas Utilization Niche,” August 2012).
The plant has 700 kW of electrical generation equipment (microturbines); in 2013, it produced just over 5 million kWh and 42,000 therms of thermal energy — providing 90 percent of the plant’s electrical and 85 percent of its heating requirements — saving SRWTF $270,000/year. The treatment plant is required to have 180 days of biosolids storage, and found itself in need of 10 million gallons of storage (in part due to increased biosolids production from the added organics), but had only 6 million gallons available. Consideration was given to stopping the high strength organics program, but ultimately the city opted to keep it and installed dewatering and drying technology, notes Sharon Thieszen, plant superintendent.
“We procured a medium temperature belt dryer, so we can use the excess biogas and extra waste heat from the turbines to dry the biosolids,” she explains. “We have already produced Class A material.”
Marsha Johnston, principal of Earth Steward Associates in Arlington, Virginia, is a Contributing Editor to BioCycle.